What is a welding inductor coil?
A welding inductor coil is an electromagnetic device used in welding applications to induce a high-frequency current into a workpiece. The inductor coil is typically made of copper wire wound around a magnetic core. This creates a magnetic field when current is passed through it. This magnetic field then induces a current in the workpiece, which can be used to weld metals together.
The inductor coil can be designed to produce a range of different frequencies, depending on the specific welding application. Higher frequencies are typically used for thinner materials and more precise welds, while lower frequencies are used for thicker materials and more robust welds.
How does a welding inductor coil work?
A welding inductor coil works by generating an electromagnetic field that induces high-frequency current in the workpiece. The inductor coil is typically made of copper wire wound around a magnetic core. This creates a magnetic field when current is passed through it. This magnetic field then induces a current in the workpiece, which can be used to weld metals together.
The high-frequency current induced in the workpiece generates heat through resistance, which is used to melt and fuse the metal together. By controlling the shape and intensity of the electromagnetic field, welders can control the shape and quality of the weld.
The geometry of the inductor coil, such as the number of turns, diameter, and spacing of the wire, affects the strength and shape of the electromagnetic field. The current frequency also plays a critical role in the welding process. Higher frequencies are typically used for thinner materials and more precise welds, while lower frequencies are used for thicker materials and more robust welds.
What are the common materials used to make welding inductor coils?
Welding inductor coils are made of copper wire and magnetic cores. Copper wire is preferred for its high electrical conductivity and flexibility, which allows it to be easily wound into the desired shape. Magnetic cores are made of materials such as iron, cobalt, or nickel, which are magnetically soft and can carry a magnetic field.
The type of magnetic core used in a welding inductor coil depends on the specific welding application. For example, iron cores are commonly used in low-frequency welding applications, while ferrite or powdered iron cores are used in high-frequency welding applications.
Other materials may also be used in the construction of welding inductor coils, depending on the specific requirements of the application. For example, insulation materials such as varnish or enamel may be applied to copper wire to protect it from heat and wear. Heat-resistant materials may also be used to protect the inductor coil from high temperatures generated during welding.

What are the benefits of using welding inductor coils in welding?
Welding inductor coils have several benefits. Here are some of the most important ones:
- Improved Efficiency: Welding inductor coils can improve the efficiency of the welding process by reducing the amount of heat required to melt the metal. This results in a shorter welding time and less energy consumption, making the welding process more efficient.
- Improved Weld Quality: Welding inductor coils can help improve the quality of the weld by creating a more uniform and controlled heating process. This can result in a stronger and more consistent weld with fewer defects.
- Versatility: Welding inductor coils can be used in a wide range of welding applications, including spot welding, seam welding, and induction brazing. This makes them a versatile tool for welders.
- Reduced Distortion: Welding inductor coils can help reduce welding distortion by providing a more even heat distribution. This can result in a more precise and accurate weld with less warping or distortion.
- Cost-Effective: Welding inductor coils can be a cost-effective solution for many welding applications, as they can reduce the amount of time and energy required to complete a weld. This can result in lower production costs and increased profitability.
What are the potential dangers of welding inductor coils?
Welding inductor coils can be dangerous if not used properly. Here are some potential hazards associated with welding inductor coils:
- Electrical Shock: Welding inductor coils can carry high electrical currents, which can be dangerous if proper safety precautions are not taken. It is important to wear appropriate personal protective equipment (PPE) and to follow safe electrical practices to avoid the risk of electrical shock.
- Fire and Explosion Hazards: Welding inductor coils can generate high levels of heat, which can pose a fire hazard if they come into contact with flammable materials. It is important to keep the work area clean and free of debris, and to avoid using welding inductor coils near combustible materials.
- Burn and Heat Hazards: Welding inductor coils can become very hot during use, which can pose a burn hazard if proper precautions are not taken. It is important to wear appropriate PPE, including heat-resistant gloves and clothing, to protect against burns.
- Chemical Exposure: Welding inductor coils can generate fumes and gases during the welding process, which can be hazardous if inhaled. It is important to use appropriate ventilation and respiratory protection to avoid the risk of chemical exposure.
- Mechanical Hazards: Welding inductor coils can be heavy and awkward to handle, which can pose a risk of injury if proper lifting techniques are not used. It is important to use appropriate lifting equipment and to follow safe handling practices to avoid the risk of injury.
How can you prevent accidents and injuries when using welding inductor coils?
Welding inductor coils can pose several hazards if not used and maintained properly. Here are some steps you can take to prevent accidents and injuries when using welding inductor coils:
- Proper training: It’s crucial to receive proper training on how to use welding inductor coils safely. Ensure that you are well-trained in welding equipment operation and maintenance, including inductor coils.
- Personal protective equipment (PPE): Always wear appropriate PPE, such as welding helmets, gloves, and safety glasses. This will protect you from welding flash, sparks, and debris.
- Proper ventilation: Ensure that the welding area is well-ventilated. Welding fumes and gases can be harmful to your health, and proper ventilation will help prevent exposure.
- Check for damage: Regularly inspect the inductor coils for damage or wear. If you notice any issues, such as cracks or breaks, replace the coil immediately.
- Use proper grounding: Ensure that welding equipment is properly grounded to prevent electric shock. Use insulated welding cables and check them regularly for damage.
- Follow safety guidelines: Always follow the safety guidelines provided by the welding equipment manufacturer. This includes information on how to use the equipment, recommended maintenance procedures, and safety precautions to take.
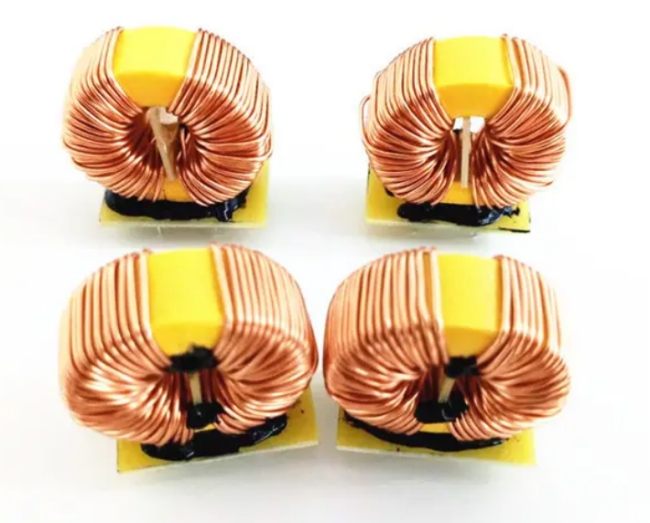
What are some common mistakes to avoid when welding inductor coils?
When working with welding inductor coils, there are several common mistakes that you should avoid to ensure safety and proper usage. Here are some examples:
- Improper grounding: One of the most common mistakes is improper grounding. It’s essential to ground the welding equipment correctly to prevent electric shock. Ensure that you use insulated welding cables and check them regularly for damage.
- Using the wrong inductor coil: Different inductor coils are suitable for different applications. Using the wrong inductor coil can lead to poor welding quality or even damage to equipment.
- Inadequate ventilation: Proper ventilation is crucial when working with welding inductor coils. Failure to ensure adequate ventilation can lead to the accumulation of welding fumes and gases, which can harm your health.
- Poor maintenance: Proper maintenance is essential to ensure your welding inductor coil functions correctly. Failure to maintain the coil can lead to damage or malfunction, which can be dangerous.
- Inadequate personal protective equipment: Welding can produce intense heat, bright light, and sparks that can cause eye and skin damage. Proper personal protective equipment such as welding helmets, gloves, and safety glasses must be used to prevent injuries.
- Lack of training: Welding inductor coils is complicated equipment that requires adequate training to use correctly. Lack of training can lead to improper usage, which can be dangerous.
How do you maintain and repair welding inductor coils?
Maintaining and repairing welding inductor coils involves several steps. Here are some general guidelines to follow:
- Regular Inspection: It is essential to inspect the inductor coils regularly for signs of wear and damage. Check the insulation for cracks, breaks, or worn spots. Also, look for any signs of corrosion or rust on the coils.
- Cleaning: Dirt and debris can accumulate on the inductor coils over time, leading to damage or reduced performance. Cleaning the coils regularly using a soft-bristled brush or compressed air can prevent this.
- Repairing Damaged Insulation: If you notice damaged insulation, it is crucial to repair it as soon as possible. Remove any damaged insulation and replace it with new insulation.
- Replacing Coils: If the coils are severely damaged or cannot be repaired, they may need to be replaced entirely.
- Testing: Once you have completed the repairs or maintenance, test the inductor coils to ensure they function correctly. You can use a multimeter to check the coils’ electrical resistance.
How do you choose the right welding inductor coil for your welding project?
Choosing the right welding inductor coil for your welding project depends on several factors such as the type of material being welded, the thickness of the material, the type of weld joint, and the welding process being used. Here are some general guidelines that may help you choose the right welding inductor coil for your project:
- Determine the type of material being welded: Different materials require different welding inductor coils. For example, if you are welding aluminum, you will need a different inductor coil than steel.
- Determine the thickness of the material: The thickness of the material being welded will also affect the type of inductor coil needed. Thicker materials require larger inductor coils to provide heat input.
- Determine the type of weld joint: The type of weld joint can also affect the choice of inductor coil. For example, a butt joint may require a different inductor coil than a lap joint.
- Determine the welding process: Different welding processes require different inductor coils. For example, a TIG welder may require a different inductor coil than a MIG welder.
- Consult with a welding expert: If you are unsure about which inductor coil to use, it’s best to consult with a welding expert who can help you choose the right one based on your specific welding project.
What are the costs associated with welding inductor coils?
There are several costs associated with welding inductor coils, including:
- Equipment Cost: The cost of purchasing the welding inductor coil itself, which can vary depending on the size and complexity of the coil.
- Maintenance Cost: Regular maintenance is required to keep the welding inductor coil functioning properly. This can include cleaning, inspections, and repairs.
- Energy Cost: Welding inductor coils requires a lot of energy to operate, which can lead to higher energy bills.
- Labor Cost: Welding inductor coils requires skilled labor, which can be expensive.
- Material Cost: The cost of the materials used in the welding process, such as electrodes, wire, and gas, can add up quickly.
- Safety Cost: Welding inductor coils can be dangerous if not used properly. Safety measures, such as protective clothing and equipment, can also cost money.
The cost of welding inductor coils will depend on various factors, including the size and complexity of the coil, the frequency of use, and local labor and material costs.