High-frequency transformers are an essential component in a wide range of electrical applications, from power supplies to medical equipment. These transformers operate at high frequencies, typically in the kilohertz or megahertz range, and are crucial for converting voltage levels to match the requirements of different devices. However, like any electrical component, high-frequency transformers can develop internal faults over time, which can cause significant problems if not diagnosed and fixed promptly.
In this blog post, we’ll discuss the importance of diagnosing internal faults in high-frequency transformers and provide an overview of diagnostic methods used to identify these faults. We’ll cover techniques for inspecting magnetic core joints, windings, insulation, wiring boxes, and outer casings, as well as common diagnostic tools and techniques. By understanding the diagnostic methods for high-frequency transformers, you can better diagnose and troubleshoot internal faults, ensuring that your equipment runs smoothly and reliably.
The internal fault diagnosis methods for high-frequency transformers include:
- Inspection of magnetic core joints: to eliminate faults such as loose or poor contact of magnetic core joints by checking whether they are connected properly.
- Inspection of windings: to determine whether the windings are normal by checking for faults such as short circuits, open circuits, or poor contact.
- Inspection of insulation: to determine whether there is insulation failure by checking the insulation status between the windings and the magnetic core.
- Inspection of wiring boxes: to eliminate faults such as poor wiring by checking the wiring conditions inside the wiring box.
- Inspection of the outer casing: to determine whether the external environment affects the normal operation of the transformer by checking for damage or deformation of the transformer’s outer casing.
Inspection of magnetic core joints methods
When diagnosing internal faults in high-frequency transformers, inspecting the magnetic core joints is an essential step as they can often be a source of issues. Here are the steps you can take to inspect magnetic core joints for faults:
- Visual Inspection: Conduct a visual inspection of the magnetic core joints to identify any physical damage such as cracks, corrosion, or discoloration. If you notice any visible damage, it is likely that there is a fault.
- Resistance Testing: Use a multimeter to measure the resistance across the magnetic core joints. If there is a significant difference in the resistance readings between the different joints, it could indicate a fault.
- Eddy Current Testing: Eddy current testing is a non-destructive testing method that can be used to identify surface cracks or other faults in the magnetic core joints. This method works by inducing an alternating magnetic field in the core, which generates eddy currents. Any flaws or cracks in the joints will produce a change in the eddy currents, which can be detected by the testing equipment.
- Flux Leakage Testing: Flux leakage testing is another non-destructive testing method that can be used to identify faults in the magnetic core joints. This method works by measuring the magnetic flux leakage around the joints. If there is a fault in the joint, it can cause a disruption in the magnetic flux, which can be detected by the testing equipment.
Inspection of windings methods
When diagnosing internal faults in high-frequency transformers, inspecting the windings is an essential step as they are a crucial component of the transformer. Here are the steps you can take to inspect the windings for faults:
- Visual Inspection: Conduct a visual inspection of the windings to identify any physical damage such as cracks, corrosion, or discoloration. If you notice any visible damage, it is likely that there is a fault.
- Insulation Resistance Testing: Use an insulation resistance tester to measure the insulation resistance of the windings. If the insulation resistance is lower than the specified value, it could indicate a fault.
- Power Factor Testing: Power factor testing can be used to identify any issues with the insulation system or the windings themselves. This testing method works by measuring the power factor of the transformer under load. If there is a fault in the windings, it can cause an increase in the power factor.
- Partial Discharge Testing: Partial discharge testing is a non-destructive testing method that can be used to detect any insulation defects or voids within the windings. This testing method works by measuring the electrical discharge that occurs within the transformer’s insulation. If there is a fault in the windings, it can cause an increase in partial discharge activity.
- Turns Ratio Testing: Turns ratio testing can be used to identify any issues with the winding turns or connections. This testing method works by measuring the ratio of the primary to secondary winding turns. If there is a fault in the winding turns or connections, it can cause an imbalance in the turns ratio.
Inspection of insulation methods
When diagnosing internal faults in high-frequency transformers, inspecting the insulation is a critical step as it is the primary protection against electrical breakdown. Here are the steps you can take to inspect the insulation for faults:
- Visual Inspection: Conduct a visual inspection of the insulation to identify any physical damage such as cracks, holes, or discoloration. If you notice any visible damage, it is likely that there is a fault.
- Insulation Resistance Testing: Use an insulation resistance tester to measure the insulation resistance of the transformer. If the insulation resistance is lower than the specified value, it could indicate a fault.
- Dielectric Absorption Testing: Dielectric absorption testing can be used to identify any issues with the insulation system or the windings themselves. This testing method works by measuring the time taken for the insulation resistance to recover after being subjected to a voltage pulse. If there is a fault in the insulation, it can cause a slow recovery time.
- Partial Discharge Testing: Partial discharge testing is a non-destructive testing method that can be used to detect any insulation defects or voids within the transformer. This testing method works by measuring the electrical discharge that occurs within the transformer’s insulation. If there is a fault in the insulation, it can cause an increase in partial discharge activity.
- Hipot Testing: Hipot testing can be used to identify any issues with the insulation strength of the transformer. This testing method works by applying a high voltage to the transformer and measuring the current flow. If there is a fault in the insulation, it can cause an increase in current flow.
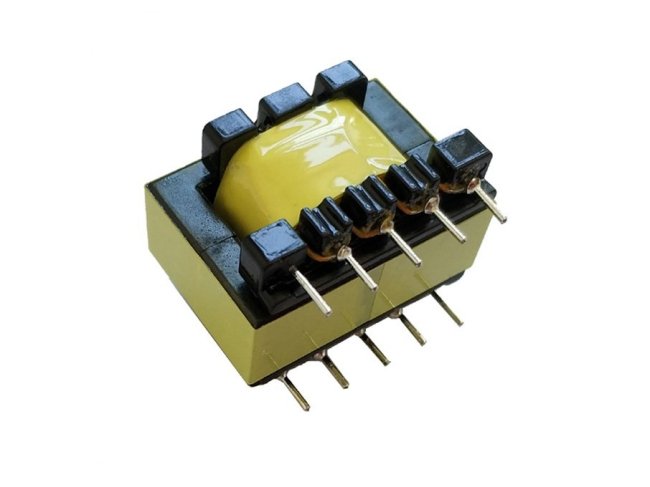
Inspection of wiring boxes methods
When diagnosing internal faults in high-frequency transformers, inspecting the wiring boxes is also an essential step, as they contain the connections between the transformer’s windings and the external circuitry. Here are the steps you can take to inspect the wiring boxes for faults:
- Visual Inspection: Conduct a visual inspection of the wiring boxes to identify any physical damage such as cracks, corrosion, or loose connections. If you notice any visible damage, it is likely that there is a fault.
- Resistance Testing: Use a multimeter to measure the resistance between each of the wiring box connections. If there is a significant difference in the resistance readings between connections, it could indicate a fault.
- Continuity Testing: Use a continuity tester to check the continuity of each of the wiring box connections. If there is an open circuit, it could indicate a fault.
- Insulation Resistance Testing: Use an insulation resistance tester to measure the insulation resistance between each of the wiring box connections and the transformer’s core or housing. If the insulation resistance is lower than the specified value, it could indicate a fault.
- Temperature Testing: Use a thermal imaging camera to check the temperature of the wiring boxes during operation. If any of the connections are significantly hotter than others, it could indicate a fault.
Inspection of the outer casing methods
When diagnosing internal faults in high-frequency transformers, inspecting the outer casing is also an important step as it can provide valuable information about the condition of the transformer’s internal components. Here are the steps you can take to inspect the outer casing for faults:
- Visual Inspection: Conduct a visual inspection of the outer casing to identify any physical damage such as cracks, dents, or corrosion. If you notice any visible damage, it is likely that there is a fault.
- Leakage Current Testing: Use a leakage current tester to measure the current flowing through the outer casing of the transformer. If there is a significant current flow, it could indicate a fault in the insulation or winding.
- Temperature Testing: Use a thermal imaging camera to check the temperature of the outer casing during operation. If any areas of the casing are significantly hotter than others, it could indicate a fault in the internal components.
- Humidity Testing: Use a hygrometer to measure the humidity level inside the outer casing. If the humidity is too high, it could indicate a fault in the insulation, causing moisture to accumulate.
- Vibration Testing: Use a vibration meter to check the level of vibration coming from the transformer. If there is excessive vibration, it could indicate a fault in the internal components.
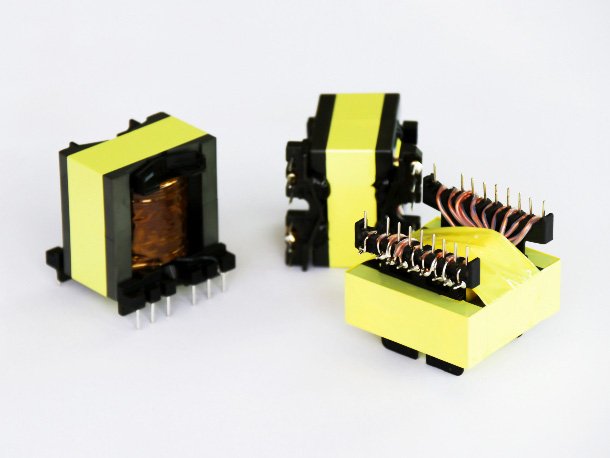
Diagnostic Tools and Techniques for Identifying Internal Faults in High-Frequency Transformers
When diagnosing internal faults in high-frequency transformers, there are various diagnostic tools and techniques that you can use to identify the root cause of the fault. Here are some commonly used diagnostic tools and techniques:
- Insulation Resistance Test: This test involves measuring the insulation resistance between the transformer’s windings and the transformer’s core or housing. The insulation resistance test can identify faults such as insulation breakdown, contamination, or moisture.
- Turns Ratio Test: This test involves measuring the ratio of the number of turns in the primary winding to the number of turns in the secondary winding. The turns ratio test can identify faults such as shorted turns, open turns, or incorrect connections.
- Winding Resistance Test: This test involves measuring the resistance of the transformer’s windings. The winding resistance test can identify faults such as shorted turns or open circuits.
- Leakage Inductance Test: This test involves measuring the leakage inductance of the transformer. The leakage inductance test can identify faults such as shorted turns or insulation breakdown.
- Frequency Response Analysis: This technique involves analyzing the frequency response of the transformer’s output signal to identify changes in the transformer’s characteristics. Frequency response analysis can identify faults such as winding deformation, core damage, or insulation breakdown.
- Visual Inspection: This involves visually inspecting the transformer for signs of physical damage, such as cracks, corrosion, or loose connections. Visual inspection can identify faults such as mechanical damage, loose connections, or environmental damage.
- Thermal Imaging: This technique involves using a thermal imaging camera to detect any abnormal temperature variations within the transformer. Thermal imaging can identify faults such as hotspots, insulation breakdown, or incorrect connections.
In conclusion, high-frequency transformers play a critical role in many electronic devices, and diagnosing internal faults in these transformers is crucial to ensure their proper functioning. Regular maintenance and inspection are of utmost importance to identify any potential issues before they become a bigger problem. Ignoring regular maintenance can lead to transformer failure and can ultimately result in costly downtime and equipment damage.
Fortunately, there are a variety of diagnostic methods and tools available that can be used to identify and diagnose internal faults in high-frequency transformers. Some of the commonly used methods include visual inspections, insulation resistance tests, power factor tests, and partial discharge measurements. It is important to choose the appropriate diagnostic method and tool based on the specific application and type of transformer being tested.
It is essential to prioritize regular maintenance and inspections, along with using appropriate diagnostic methods and tools, to ensure the longevity and reliability of high-frequency transformers. By taking these measures, the risk of failure can be minimized, leading to improved efficiency, reduced costs, and increased safety.