In the world of high-frequency transformers, magnetics are king. Magnetics are the invisible force that makes these transformers work. They play a critical role in the performance and efficiency of these transformers. From magnetic cores to winding techniques, magnetics are designed to maximize energy transfer, minimize losses and ensure these transformers work in high-frequency applications. Understanding the role of magnetics is key to unlocking the full potential of high-frequency transformers and will change the way we use electrical power.
In this blog post, we will explore the world of high-frequency transformers and explain why magnetics are so important. We will explain the relationship between magnetics and high-frequency transformer performance, talk about the challenges of designing magnetic components and discuss the latest cutting-edge techniques to overcome these challenges. By the end of this blog post, you will have a better understanding of how critical magnetics are to the efficiency, reliability and power of high-frequency transformers.
Why are magnetics important in high frequency transformers?
Firstly, the choice of magnetic materials is crucial for efficient operation. High-frequency transformers require core materials with low magnetic losses, high permeability, and minimal hysteresis losses. These properties allow the core to store and transfer magnetic energy efficiently, reducing power dissipation and improving overall transformer efficiency. Proper selection of magnetic materials ensures optimal performance at high frequencies.
Secondly, magnetic flux density is a critical consideration in high-frequency transformers. These transformers operate at elevated frequencies, often in the kilohertz to megahertz range. At such frequencies, the magnetic flux density within the transformer core experiences rapid changes. Magnetic materials with high saturation flux density are essential to prevent core saturation and maintain the transformer’s performance under these dynamic conditions.
Eddy current losses are another important factor to consider. In high-frequency transformers, eddy currents induced in the core material can lead to significant power losses. To mitigate these losses, magnetic cores are often designed using laminated materials or powdered cores. These designs minimize the formation of large eddy currents, reducing energy losses and improving transformer efficiency.
Magnetic coupling is crucial in high-frequency transformers, especially in applications where space and weight are critical. Magnetic coupling between the primary and secondary windings of the transformer ensures efficient power transfer and maintains signal integrity. Careful selection of magnetic materials and core design ensures a high degree of magnetic coupling and minimizes leakage inductance.
Lastly, the frequency response of high-frequency transformers is essential to handle rapid changes in voltage and current. Magnetic materials with high permeability, low core losses, and controlled frequency-dependent behavior enable the transformer to accurately maintain voltage and current levels across a wide range of frequencies.
In summary, the choice and optimization of magnetic materials and components in high-frequency transformers are crucial for achieving high efficiency, minimal power losses, compact size, and excellent performance in various electronic and power applications.
How do magnetics affect the performance of high frequency transformers?
Magnetics, specifically the design and materials used in high frequency transformers, have a significant impact on their performance. Here are 6 keys points to affect the performance of high frequency transformers:
1.Core Material:
The choice of core material is crucial in high frequency transformers. Soft magnetic materials, such as ferrites or powdered iron, are commonly used due to their high permeability and low core losses at high frequencies. These materials help minimize energy losses and improve the efficiency of the transformer.
2.Core Geometry:
The geometric configuration of the core, such as its shape and winding arrangement, plays a vital role in high frequency transformers. The core design must minimize the leakage flux and maximize the coupling between the primary and secondary windings. This helps to enhance the transformer’s efficiency and reduce electromagnetic interference (EMI).
3.Winding Design:
The winding structure of a high frequency transformer must be carefully designed to minimize resistance, inductance, and parasitic capacitance. These parasitic elements can cause losses and distortions at high frequencies. Special attention should be given to the insulation between windings to avoid inter-winding capacitance, which can adversely affect the transformer’s performance.
4.Skin Effect:
At high frequencies, the skin effect becomes more prominent. It causes the current to concentrate near the surface of the conductor, increasing the effective resistance. To mitigate this effect, high frequency transformers often use litz wire, which is composed of multiple individually insulated strands. Litz wire reduces the resistance and distributes the current more evenly across the conductor.
5.Magnetic Field Distribution:
High frequency transformers operate with rapidly changing magnetic fields. It is crucial to carefully design the windings and core to ensure that the magnetic field is distributed evenly, minimizing core losses and maximizing efficiency. Proper shielding and magnetic materials selection can help control and shape the magnetic field to achieve optimal performance.
6.Losses and Efficiency:
High frequency transformers are subject to various types of losses, including core losses (hysteresis and eddy current losses), copper losses (resistive losses in windings), and stray losses (caused by leakage flux). Minimizing these losses is essential to improve the overall efficiency of the transformer.
What role do magnetic materials play in high frequency transformer design?
Magnetic materials play a crucial role in the design of high frequency transformers. Here are 5 keys roles they play:
1.Flux Conduction:
Magnetic materials, such as ferrites or powdered iron, are chosen as the core material in high frequency transformers because they have high permeability. This high permeability allows for efficient conduction of magnetic flux, enhancing the transformer’s performance.
2.Core Losses:
Magnetic materials help minimize core losses in high frequency transformers. Core losses occur due to hysteresis and eddy currents when the magnetic field changes rapidly. By selecting magnetic materials with low coercivity and high resistivity, these losses can be reduced, resulting in higher efficiency.
3.Saturation Behavior:
Magnetic materials have a saturation point where their magnetic properties become non-linear. In high frequency transformers, it is important to choose magnetic materials with a high saturation flux density. This ensures that the core does not saturate under operating conditions, preventing excessive core losses and maintaining efficient operation.
4.Temperature Stability:
Magnetic materials used in high frequency transformers should exhibit good temperature stability. They should retain their magnetic properties over a wide temperature range, ensuring consistent performance under varying operating conditions.
5.EMI Reduction:
Magnetic materials can help mitigate electromagnetic interference (EMI) issues in high frequency transformers. By using materials with high magnetic permeability, the magnetic flux can be contained and directed within the core, reducing its impact on surrounding circuitry and minimizing EMI.
How do magnetic cores impact the efficiency of high frequency transformers?
Magnetic materials play a crucial role in the design of high frequency transformers. Here are 5 key roles they play
1.Flux Conduction:
Magnetic materials, such as ferrites or powdered iron, are chosen as the core material in high frequency transformers because they have high permeability. This high permeability allows for efficient conduction of magnetic flux, enhancing the transformer’s performance.
2.Core Losses:
Magnetic materials help minimize core losses in high frequency transformers. Core losses occur due to hysteresis and eddy currents when the magnetic field changes rapidly. By selecting magnetic materials with low coercivity and high resistivity, these losses can be reduced, resulting in higher efficiency.
3.Saturation Behavior:
Magnetic materials have a saturation point where their magnetic properties become non-linear. In high frequency transformers, it is important to choose magnetic materials with a high saturation flux density. This ensures that the core does not saturate under operating conditions, preventing excessive core losses and maintaining efficient operation
4.Temperature Stability:
Magnetic materials used in high frequency transformers should exhibit good temperature stability. They should retain their magnetic properties over a wide temperature range, ensuring consistent performance under varying operating conditions.
5.EMI Reduction:
Magnetic materials can help mitigate electromagnetic interference (EMI) issues in high frequency transformers. By using materials with high magnetic permeability, the magnetic flux can be contained and directed within the core, reducing its impact on surrounding circuitry and minimizing EMI.
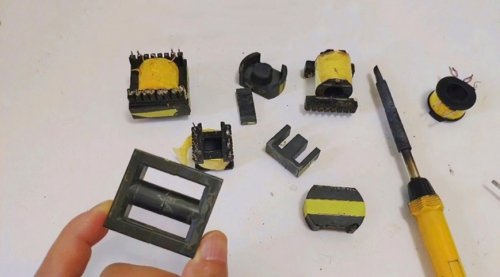
What are the key factors to consider when selecting magnetic materials for high frequency transformers?
When selecting magnetic materials for high frequency transformers, below 7 key factors should be considered:
1.Core Losses:
Core losses, including hysteresis and eddy current losses, are a crucial consideration. High frequency transformers operate with rapidly changing magnetic fields, making core losses a significant concern. It is important to choose magnetic materials with low coercivity and high resistivity to minimize these losses and enhance overall efficiency.
2.Permeability:
The permeability of the magnetic material influences its ability to conduct magnetic flux. Higher permeability allows for better flux conduction and improved coupling between windings. Selecting materials with appropriate permeability ensures efficient energy transfer and reduced energy losses.
3.Saturation Flux Density:
Magnetic materials have a saturation point where their magnetic properties become non-linear. It is essential to choose materials with a high saturation flux density to prevent core saturation under operating conditions. Core saturation leads to increased losses and decreased efficiency
4.Temperature Stability:
Magnetic materials used in high frequency transformers should exhibit good temperature stability. They should maintain their magnetic properties over a wide temperature range to ensure consistent performance. It is important to consider the Curie temperature, which is the temperature at which a material loses its magnetic properties.
5.Frequency Response:
Magnetic materials may exhibit frequency-dependent characteristics. It is important to select materials that maintain their magnetic properties at the operating frequency of the transformer. Some materials may experience increased losses or changes in permeability at higher frequencies, which can impact transformer performance.
6.Cost and Availability:
Cost and availability are practical considerations when selecting magnetic materials. Some materials may be more expensive or harder to source than others. It is important to balance the desired magnetic properties with cost-effectiveness and availability.
7.Manufacturing Process:
The ease of manufacturing and shaping the magnetic material into the desired core shape should also be considered. Some materials may be more suitable for specific manufacturing processes, such as powder metallurgy for powdered iron cores or ceramic processing for ferrite cores.
How do losses in magnetics affect the overall efficiency of high frequency transformers?
Losses in magnetics have a significant impact on the overall efficiency of high frequency transformers. Here’s how losses affect efficiency:
- Core Losses: Core losses in high frequency transformers include hysteresis and eddy current losses. Hysteresis loss occurs due to the energy dissipated when the magnetic core undergoes magnetic reversals. Eddy current loss occurs due to circulating currents induced in the core material by the changing magnetic field. These losses result in energy being converted into heat, reducing the transformer’s efficiency.
- Copper Losses: Copper losses occur in the transformer windings due to the resistance of the wire. When high frequency currents flow through the windings, resistance leads to power dissipation and heat generation. Copper losses can be minimized by using low-resistance conductors, optimizing the winding design, and reducing skin and proximity effects.
- Stray Losses: Stray losses refer to energy losses that occur due to flux leakage or coupling with surrounding components. These losses can occur in the transformer core, windings, or other nearby conductive components. Stray losses can be mitigated by proper design techniques such as magnetic shielding, interleaving windings, and optimizing the core structure.
- Total Losses: The sum of core losses, copper losses, and stray losses constitutes the total losses in a high frequency transformer. These losses contribute to energy inefficiency and heat generation. Minimizing total losses is crucial for improving the overall efficiency of the transformer.
Reducing losses is essential to enhance the efficiency of high frequency transformers. This can be achieved through careful selection of magnetic core materials with low core losses, optimizing winding designs to minimize copper losses, and implementing effective strategies to mitigate stray losses. Advanced simulation and modeling techniques can aid in accurately predicting and optimizing the losses to achieve higher efficiency.
Efficiency improvement not only reduces energy wastage but also helps in reducing operating costs and environmental impact. Therefore, comprehensive loss analysis and optimization play a critical role in designing high-performance high frequency transformers.
What are the challenges in designing magnetics for high frequency transformers?
Designing magnetics for high frequency transformers poses unique challenges that require careful consideration and expertise. Here are 6 key challenges:
1.Core Selection:
Selecting the appropriate magnetic core material is crucial. High frequency transformers require materials with low core losses, high permeability, and good saturation characteristics. Finding a balance between these properties can be challenging, as materials with high permeability often have higher losses.
2.Core Saturation:
High frequency operation can lead to increased core saturation. When the core saturates, it loses its ability to efficiently conduct magnetic flux, resulting in higher losses and reduced efficiency. Managing core saturation by selecting suitable core materials and optimizing the design becomes critical to ensure optimal performance
3.Skin and Proximity Effects:
At high frequencies, skin and proximity effects become more pronounced. Skin effect refers to the tendency of high frequency currents to concentrate near the surface of conductors, increasing their effective resistance. Proximity effect occurs when magnetic fields from adjacent conductors interact, affecting the current distribution and increasing losses. Minimizing these effects requires careful consideration of conductor size, insulation, and winding configurations.
4.Thermal Management:
High frequency transformers often generate significant heat due to core losses, copper losses, and proximity effects. Ensuring proper thermal management is crucial to prevent overheating and maintain efficient operation. Adequate cooling mechanisms, such as thermal conduction paths, heatsinks, and cooling fluids, need to be incorporated into the design.
5.Electromagnetic Interference (EMI):
High frequency transformers can be a source of electromagnetic interference. The fast switching of currents and magnetic fields can generate EMI, which may interfere with other components or systems. Designing effective shielding, grounding, and filtering techniques is necessary to mitigate EMI issues.
6.Parasitic Capacitance and Inductance:
Parasitic capacitance and inductance can significantly impact the performance of high frequency transformers. These parasitic elements can cause unwanted resonances, voltage spikes, and waveform distortions. Careful layout and design techniques, such as minimizing trace lengths and optimizing component placement, are crucial to minimize their effects.
Designing magnetics for high frequency transformers requires a thorough understanding of electromagnetic theory, material properties, and circuit behavior at high frequencies. It involves striking a balance between core selection, managing core saturation, addressing skin and proximity effects, ensuring thermal management, mitigating EMI, and minimizing parasitic elements.
How do winding techniques influence the behavior of magnetics in high frequency transformers?
Winding techniques have a significant impact on the performance and behavior of magnetics in high frequency transformers. Here are 6 key points to consider:
1.Proximity Effect:
The proximity effect refers to the phenomenon where the magnetic fields of adjacent conductors interact with each other. In high frequency transformers, this effect becomes more pronounced, leading to increased resistance and losses. By carefully selecting the winding technique, such as interleaved or transposed windings, the proximity effect can be mitigated, resulting in reduced losses and improved efficiency.
2.Skin Effect:
At high frequencies, current tends to flow predominantly near the surface of conductors, known as the skin effect. This behavior increases the effective resistance of the conductor, leading to higher losses. By employing stranded conductors or Litz wire (which consists of multiple thin strands insulated from each other), the surface area available for current flow is increased, reducing the skin effect and its associated losses
3.Leakage Inductance:
Leakage inductance refers to the portion of the magnetic field in a transformer that does not link both the primary and secondary windings. It can negatively impact the transformer’s performance by reducing coupling efficiency and causing voltage spikes or ringing. Proper winding techniques, such as tightly coupled windings or using magnetic shields, can help minimize leakage inductance and enhance overall transformer behavior.
4.Interwinding Capacitance:
Interwinding capacitance is the inherent capacitance between adjacent windings in a transformer. At high frequencies, this capacitance can affect the transformer’s electrical behavior, leading to resonances or voltage distortions. Techniques like layer insulation or placing insulation between windings can help reduce interwinding capacitance and mitigate its adverse effects.
5.Impedance Matching:
Impedance matching is critical for efficient power transfer in high frequency transformers. By carefully selecting the turns ratio and optimizing the winding technique, the impedance seen by the source and load can be matched, maximizing power transfer efficiency and minimizing reflected impedance.
6.Parasitic Elements:
Winding techniques can influence the presence of parasitic elements, such as parasitic capacitance and inductance. These elements can impact the transformer’s behavior, causing ringing, voltage spikes, or resonances. Proper winding configurations and insulation techniques can help minimize parasitic effects and improve overall performance.
How can I minimize losses and improve efficiency in high frequency transformers through proper magnetic design?
To minimize losses and improve efficiency in high frequency transformers through proper magnetic design, consider implementing the following techniques:
- Core Material Selection: Choose a magnetic core material with low core losses, such as ferrites or powdered iron, to reduce hysteresis and eddy current losses. Materials with high resistivity and low coercivity are preferred for high frequency applications.
- Core Geometry: Optimize the core geometry to minimize air gaps, reduce flux leakage, and improve magnetic coupling. Using toroidal or distributed air-gap cores can help enhance efficiency by reducing stray magnetic fields and losses.
- Core Saturation: Select a core material with a high saturation flux density to ensure the core does not saturate under operating conditions. Saturation leads to increased losses and decreased efficiency. Properly sizing the core and conducting saturation analysis can prevent this issue.
- Windings and Conductors: Use low-resistance conductors with larger cross-sectional areas to minimize copper losses. Consider stranded conductors or Litz wire to mitigate skin and proximity effects. Properly design the winding layout to minimize leakage inductance and maximize coupling.
- Cooling: Adequate cooling is crucial to maintain optimal operating temperatures and improve efficiency. Ensure efficient heat dissipation by incorporating cooling mechanisms such as heatsinks, fans, or liquid cooling. Proper thermal management prevents excessive temperature rise, which can increase losses.
- Minimize Parasitic Elements: Reduce parasitic capacitance and inductance by carefully designing the winding layout, insulation techniques, and shielding. Minimizing parasitic elements helps avoid resonances, voltage spikes, and waveform distortions that can impact efficiency.
- Loss Analysis and Simulation: Utilize advanced simulation tools and modeling techniques to analyze losses and optimize the design. Perform detailed electromagnetic and thermal simulations to identify areas of improvement and validate the design’s efficiency.
- Magnetic Shielding: Incorporate magnetic shielding to minimize external magnetic field interference and reduce losses caused by stray magnetic fields. Shielding materials like mu-metal can effectively redirect magnetic flux and improve efficiency.
- Operating Frequency Optimization: Properly select the operating frequency of the transformer to match the characteristics of the core material and minimize losses. Operating at the resonant frequency of the core material can maximize efficiency.
- Quality Control: Implement rigorous quality control measures to ensure consistent manufacturing and reduce variations that can impact efficiency. Verify the material properties, core dimensions, and winding parameters to meet the desired specifications.

What are some common techniques to overcome challenges related to magnetics in high frequency transformers?
When it comes to overcoming challenges related to magnetics in high frequency transformers, 9 common techniques can be employed. Below common techniques for your reference:
- Core Material Selection: Choose magnetic core materials that are specifically designed for high frequency applications. Materials such as ferrites, powdered iron, and nanocrystalline alloys are commonly used due to their low core losses and high permeability at high frequencies.
- Core Design Optimization: Optimize the core geometry to minimize air gaps, reduce flux leakage, and improve magnetic coupling. This can be achieved through techniques such as toroidal cores, distributed air gaps, or employing advanced core shapes that maximize the magnetic field confinement.
- Winding Techniques: Implement specific winding techniques to address challenges associated with high frequency transformers. Interleaved windings, where primary and secondary windings are distributed throughout the core, can help reduce leakage inductance and improve coupling efficiency. Additionally, using stranded conductors or Litz wire can mitigate skin and proximity effects.
- Insulation and Shielding: Proper insulation between windings and layers, as well as shielding techniques, are essential to minimize parasitic capacitance and inductance. Insulating materials with high dielectric strength and low losses should be used, and magnetic shields can help reduce external magnetic field interference and stray losses.
- Cooling and Thermal Management: High frequency transformers can generate significant heat due to core losses and copper losses. Effective cooling mechanisms such as heatsinks, fans, or liquid cooling should be implemented to maintain optimal operating temperatures and improve overall efficiency.
- Advanced Simulation and Modeling: Utilize electromagnetic and thermal simulation tools to analyze the behavior of magnetics in high frequency transformers. These tools can help optimize the design, predict losses, and identify areas for improvement, saving time and resources in the design process.
- EMI Mitigation: High frequency transformers can be a source of electromagnetic interference (EMI). Implement proper grounding, shielding, and filtering techniques to minimize EMI. Careful placement of components, optimized layout, and the use of EMI filters can help mitigate unwanted electromagnetic emissions.
- Quality Control and Testing: Implement stringent quality control measures throughout the manufacturing process to ensure consistency and reliability. Thoroughly test the transformers to verify their performance, efficiency, and adherence to specifications.
- Collaboration and Expertise: Seek collaboration with experienced engineers, transformer designers, and experts in the field of high frequency magnetics. Their knowledge and expertise can provide valuable insights and guidance in overcoming challenges and optimizing the transformer design.
How does temperature affect the magnetic properties and performance of high frequency transformers?
Temperature has a significant impact on the magnetic properties and performance of high frequency transformers. Here’s how temperature affects them:
Core Material Properties: The magnetic properties of core materials, such as permeability and magnetic saturation, can be temperature-dependent. As the temperature increases, the permeability of certain materials may decrease, resulting in higher magnetic losses and reduced overall transformer efficiency. Additionally, the magnetic saturation level of the core material can be affected by temperature, leading to a decrease in the maximum magnetic flux density the core can handle before saturating.
Core Losses: Temperature can affect the core losses in high frequency transformers. Core losses consist of hysteresis losses and eddy current losses. Hysteresis losses occur due to the magnetization and demagnetization of the core material, while eddy current losses result from circulating currents induced within the core. Both types of losses tend to increase with temperature, leading to decreased efficiency and increased temperature rise within the transformer.
Copper Losses: The resistance of the winding conductors increases with temperature, leading to increased copper losses. This is known as the temperature coefficient of resistance. The increase in copper losses can impact the overall efficiency of the transformer. Additionally, high temperatures can cause thermal expansion and stress on the winding conductors, potentially leading to mechanical failures or increased resistance due to poor connections.
Insulation Properties: Temperature can affect the insulation properties of materials used to insulate the windings. If the operating temperature exceeds the designed temperature rating of the insulation, it can lead to insulation breakdown, reduced dielectric strength, and increased risk of electrical faults or short circuits. Proper selection of insulation materials and consideration of their temperature rating are essential to maintain reliable performance.
Impedance and Frequency Response: Temperature variations can affect the impedance and frequency response of high frequency transformers. Changes in temperature can alter the winding resistance, which directly impacts the transformer’s impedance. This can lead to variations in the voltage and current transfer characteristics of the transformer, affecting its performance in terms of frequency response and signal integrity.
Thermal Management: Efficient thermal management becomes crucial as temperature rise can negatively impact the transformer’s performance. Excessive heat can accelerate aging, degrade the insulation, increase losses, and reduce overall efficiency. Proper cooling mechanisms, such as heatsinks, fans, or liquid cooling, should be employed to maintain the operating temperature within acceptable limits and ensure reliable operation.
What are the advancements and trends in magnetic materials for high frequency transformers?
Advancements and trends in magnetic materials for high frequency transformers are driven by the increasing demand for higher efficiency, smaller size, and improved performance. Here are 8 notable advancements and trends:
- Soft Magnetic Materials: The development of new soft magnetic materials has been a significant trend. These materials exhibit low core losses and high saturation flux density, making them ideal for high frequency applications. Examples include advanced ferrite materials, nanocrystalline alloys, and amorphous alloys. These materials offer improved magnetic properties and reduced losses compared to traditional materials like laminated iron cores.
- Powdered Core Materials: Powdered core materials, such as powdered iron or powdered ferrites, are gaining popularity for high frequency transformers. These materials are made by mixing fine magnetic particles with insulating binders. They offer excellent magnetic properties, low core losses, and good thermal conductivity. Powdered cores enable compact designs with reduced weight and improved efficiency.
- Nanocrystalline Alloys: Nanocrystalline alloys are emerging as promising materials for high frequency transformers. These alloys exhibit extremely high permeability, low core losses, and good thermal stability. They are particularly suitable for high-frequency applications due to their superior magnetic properties and excellent frequency response.
- Composite Materials: Composite materials, which combine different magnetic materials, are being explored to optimize the performance of high frequency transformers. These composites can combine the strengths of different materials, such as high permeability and low core losses, to achieve improved efficiency and enhanced magnetic properties.
- Hybrid Core Designs: Hybrid core designs involve combining different magnetic materials within the same core structure. This approach allows for a tailored magnetic response to specific frequency ranges, optimizing efficiency and reducing losses. Hybrid cores can be composed of different materials such as ferrites, nanocrystalline alloys, and powdered iron, strategically placed to achieve the desired magnetic characteristics.
- Thin-Film Magnetic Materials: Thin-film magnetic materials are gaining attention for high frequency applications. These materials are deposited as thin layers on substrates, offering the advantage of precise control over material properties and reducing core losses. Thin-film technology allows for the design of compact and high-performance transformers.
- Advanced Modeling and Simulation: Advancements in electromagnetic modeling and simulation tools are enabling more accurate predictions of the behavior of magnetic materials in high frequency transformers. These tools aid in optimizing core designs, predicting losses, and evaluating the performance of different materials, accelerating the design process and reducing development costs.
- Green Magnetic Materials: With the increasing focus on sustainability, there is a growing interest in developing environmentally friendly magnetic materials for high frequency transformers. Researchers are exploring options such as recyclable materials, materials with reduced rare-earth content, and materials with improved energy efficiency.
These advancements and trends in magnetic materials for high frequency transformers are aimed at achieving higher efficiency, smaller form factors, and improved performance. They enable the development of transformers that meet the demands of modern applications while reducing energy consumption and environmental impact.
How can I improve the power density of high frequency transformers through magnetic design?
Improving the power density of high frequency transformers through magnetic design involves maximizing the power output while minimizing the size and weight of the transformer. Here are 9 key strategies to achieve higher power density:
- Core Material Selection: Choose magnetic core materials with high saturation flux density and low core losses. Materials like nanocrystalline alloys, powdered iron, or advanced ferrites offer favorable magnetic properties for high frequency applications. High saturation flux density allows for smaller core sizes, while low core losses minimize power dissipation.
- Core Geometry Optimization: Optimize the core geometry to reduce core losses and maximize magnetic coupling. Use compact core shapes such as toroids or distributed air-gap cores to minimize magnetic leakage and enhance efficiency. Additionally, design the core to minimize air gaps and maximize the magnetic flux path within the core material.
- Winding Techniques: Utilize winding techniques that maximize the copper fill factor and reduce losses. Implement interleaved windings or transposed windings to mitigate skin and proximity effects, reducing winding resistance and improving efficiency. Additionally, consider the use of stranded conductors or Litz wire to minimize losses at high frequencies.
- High-Frequency Design Considerations: High frequency transformers require careful consideration of parasitic elements. Minimize parasitic capacitance and inductance by optimizing insulation and spacing between windings. Use proper shielding techniques to reduce electromagnetic interference and eddy currents.
- Cooling and Thermal Management: Efficient cooling mechanisms are crucial to handle the increased power density. Implement effective heat dissipation techniques, such as heatsinks, fans, or liquid cooling, to maintain optimal operating temperatures. This allows the transformer to handle higher power levels without compromising reliability.
- Advanced Simulation and Modeling: Utilize electromagnetic and thermal simulation tools to analyze and optimize the transformer design. These tools can help identify areas for improvement, predict losses, and optimize the design parameters. Advanced modeling techniques aid in achieving higher power density by accurately assessing performance and identifying optimization opportunities.
- Advanced Magnetic Materials: Consider utilizing advanced magnetic materials such as nanocrystalline alloys or high-performance ferrites. These materials offer improved magnetic properties and lower losses, enabling higher power density designs.
- Optimization of Losses: Minimize core losses, copper losses, and stray losses through proper material selection, core design optimization, and winding techniques. Each loss component contributes to the overall power dissipation and reduces power density. Reducing losses through careful design considerations leads to higher power density.
- System Integration and Component Placement: Optimize the integration of the transformer within the overall system. Carefully select the location and arrangement of the transformer to minimize losses and optimize performance. Consider factors such as electromagnetic interference, cooling, and space constraints to achieve maximum power density.
Throughout this blog post, we have explored the captivating world of magnetics in high frequency transformers. We learned that magnetics, from magnetic cores to winding techniques, are the vital components that shape the performance, efficiency, and reliability of high frequency transformers. We discovered how the selection of magnetic materials, the management of losses, and the optimization of magnetic design can significantly impact the overall operation of these transformers. Magnetics truly hold the power to unlock the full potential of high frequency transformer technology.
Understanding the intricate world of magnetics is crucial for achieving efficient and reliable high frequency transformer designs. By grasping the underlying principles, challenges, and design considerations related to magnetics, we can overcome obstacles, optimize performance, and push the boundaries of what high frequency transformers can achieve. Ignorance of magnetics limits our ability to harness the true potential of these transformers and can lead to suboptimal designs. Therefore, delving into the realm of magnetics is essential for engineers, designers, and enthusiasts seeking to make significant advancements in high frequency