This article explores the different types of winding arrangements used in high-frequency transformers, including the primary and secondary winding configurations. It also discusses the benefits and drawbacks of each type of winding arrangement and provides examples of where they may be used. If you’re interested in learning more about high-frequency transformers, this article is a must-read.
What are the different types of winding arrangements used in high-frequency transformers?
For high-frequency transformers, there are various coil configurations, including:
1.Layered winding: For winding, the same-turn count wires are split into a number of layers. To lower the capacitance and reciprocal inductance of the winding, an insulating layer separates the layers.
Advantages:
- Reduced capacitance: The insulation between the winding’s layers lowers the transformer’s capacitance, which can increase its effectiveness and cut down on energy losses.
- Lessened leakage inductance: The insulation in the winding’s layers also lessens leakage inductance, which can enhance the transformer’s efficiency at high frequencies.
- Layered winding is a winding arrangement that is comparatively easy to manufacture and is frequently used in many high-frequency transformers.
Disadvantages:
- High winding resistance: Using numerous layers may result in an increase in winding resistance, which can lower transformer efficiency and raise operating temperature.
- Difficult to repair: It can be challenging to fix a fault in one layer of the winding without impacting the others.
- Limited current capacity: Using numerous layers can reduce the transformer’s current capacity because smaller wire gauges are needed to fit into the constrained space between layers.
2.Helical winding: An insulating layer is placed between each turn of the wire as it spirals around the magnetic center. This is appropriate for transformers with minimal power.
Advantages:
- High current carrying capacity: Helical winding has an excellent capacity for heat dissipation and is able to withstand high current loads without overheating.
- Lower leakage inductance: In high-frequency uses, the helical winding’s configuration results in a lower leakage inductance.
- Ease of manufacture: By spiraling the wire around the magnetic center, helical winding can be produced with ease.
Disadvantages:
- High capacitance: Due to the close proximity of the turns, helical winding creates a high capacitance, which could be troublesome in some high-frequency applications.
- Lower voltage rating: The transformer’s voltage rating may need to be lowered as a result of the greater capacitance.
- Limited capacity for handling power: Helical winding may not be appropriate for high-power applications because it is more challenging to cool and can become saturated if not designed correctly.
3.Tapered winding: To lower the capacitance and inductance of the winding, the cross-sectional area of the winding gradually rises or decreases from one end of the magnetic core to the other.
Advantages:
- Reduced capacitance: By using different wire sizes, tapered winding lowers the capacitance between turns, which can enhance the transformer’s efficiency at high frequencies.
- Reduced leakage inductance: Tapered winding uses various wire diameters to lower leakage inductance, which can increase the transformer’s effectiveness and cut down on energy losses.
- Better voltage control: By reducing the voltage drop across the winding, tapered winding can provide better voltage regulation.
Disadvantages:
- Difficult to manufacture: Compared to other winding arrangements, tapered winding needs precise control over the winding process, making it harder to manufacture.
- Increased winding resistance: Due to the use of various wire sizes, tapered winding may increase winding resistance, which can lower the transformer’s efficiency and raise its working temperature.
- Limited current handling capacity: The transformer’s ability to handle current loads may be restricted by the use of various wire sizes, as the smaller wire sizes used for winding may not be able to support high current loads.
4.Parallel winding: To boost the transformer’s output power, several windings are connected in parallel.
Advantages:
- Increased power handling capacity: By enabling multiple winding sections to handle the load in parallel, parallel winding increases the transformer’s power handling capacity.
- Improved voltage regulation: By lowering the voltage loss across the winding, parallel winding can enhance voltage regulation.
- Lower winding resistance: By carrying a smaller current load through each section of the winding, parallel winding lowers the total resistance of the winding.
Disadvantage:
- Increased leakage inductance: Parallel winding may result in a rise in leakage inductance, which lowers the transformer’s efficiency.
- Greater capacitance: Due to the close closeness of the parallel winding sections, parallel winding can increase the capacitance of the transformer.
- Parallel winding is more challenging to make than other winding arrangements because it requires precise control over the winding process.
6.Dual winding: To improve the transformer’s electrical separation performance, one winding is split into two separate windings.
Advantages:
- 1) Improved electrical isolation: Because the two windings are entirely separate and isolated from one another, dual winding improves electrical isolation between the two windings. This could increase the transformer’s dependability and safety.
Better voltage regulation: Dual winding can provide separate windings for the main and secondary sides, which can help with voltage regulation.
Flexible output voltage is possible with dual winding because each winding can be made to provide a distinct voltage level.
Disadvantage:
- Increased winding resistance: Because each winding is independent and separate, dual winding can result in a rise in winding resistance, which raises the transformer’s overall resistance.
- Increased leakage inductance: Dual winding may result in a rise in leakage inductance, which lowers the transformer’s efficiency.
- Larger size: Dual winding necessitates a larger physical size for the transformer in order to fit the two distinct windings, which increases the transformer’s overall size and weight.
What is a primary winding and what is its role in a high-frequency transformer?
A primary winding is a coil of wire in a high-frequency transformer that is connected to the input voltage source. Its role is to transfer electrical energy from the input voltage source to the transformer’s core, where it induces a magnetic field that is used to transfer energy to the secondary winding.
The primary winding is typically wound around one leg of the transformer’s core, with the other leg used for the secondary winding. The number of turns in the primary winding is determined by the input voltage, the desired output voltage, and the transformer’s design specifications.
The main winding of a transformer produces an alternating current that expands and contracts to form a magnetic field around the core. The secondary winding, which is linked to the load, experiences an electrical current as a result of the shifting magnetic field.
The transformer’s main winding, which determines the voltage transformation ratio and the effectiveness of energy transfer from the input voltage source to the load, is essential to its operation. To make sure the transformer works effectively and safely, it’s crucial to carefully choose the primary winding’s insulation, wire gauge, and number of turns.
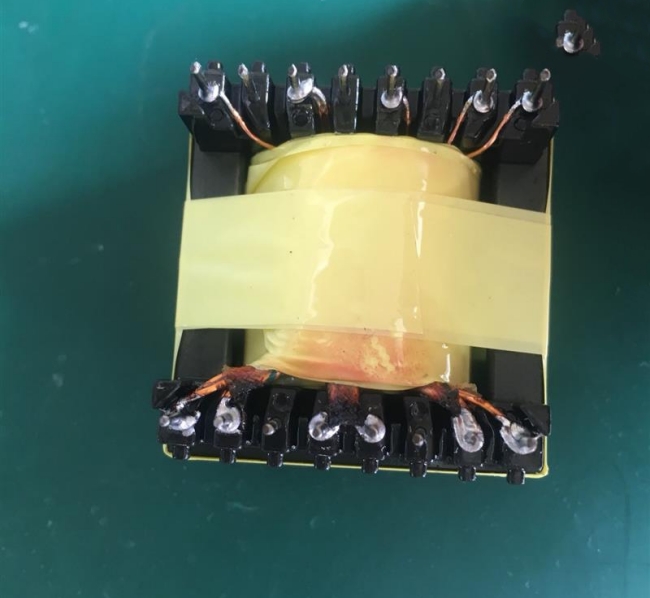
What is a secondary winding and what is its role in a high-frequency transformer?
A high-frequency transformer’s secondary winding is the coil of wire that is attached to the load. Its function is to transmit to the load the electrical energy that the main winding induces in the transformer’s core.
In contrast to the primary winding, the secondary winding is usually wound around the other leg of the transformer’s core. The intended output voltage, the input voltage, and the transformer’s design requirements all influence how many turns there should be in the secondary winding.
The main winding of a transformer produces an alternating current that expands and contracts to form a magnetic field around the core. The secondary winding, which is linked to the load, experiences an electrical current as a result of the shifting magnetic field.
Because it controls the transformer’s output voltage and current, the secondary coil is essential to its functionality. To guarantee the transformer works effectively and safely, it is crucial to carefully choose the number of turns, wire gauge, and secondary winding insulation.
Multiple secondary windings connected to various loads may be present in some transformers, providing for multiple outputs. In these transformers, the secondary winding(s) still have the same function, which is to deliver the electrical energy that the primary winding has generated in the core to the loads.
What advantages do series windings have over parallel windings in a high-frequency transformer?
What advantages do series windings have over parallel windings in a high-frequency transformer?
When the main and secondary windings of a high-frequency transformer are wired together in a series circuit, this is referred to as a series winding arrangement. The load is linked to the secondary winding, which is connected to the input voltage source.
In a high-frequency transformer, using a series coil configuration has several advantages.
- Better voltage regulation: Because the secondary winding’s voltage is proportional to the winding’s fixed number of turns, the series winding arrangement offers better voltage control. As a result, it is simpler to keep the output voltage stable even when the input voltage changes.
- Increased effectiveness of energy transfer: Because the main and secondary windings are linked in series, the current flowing through each of them is the same. This increases the effectiveness of energy transmission by lowering the losses brought on by current passing through the internal resistance of the transformer.
- Compact design: The primary and secondary windings of the transformer are wrapped on the same core leg thanks to the series winding arrangement, which makes the transformer smaller and lighter.
- Less expensive: Since the series winding arrangement uses fewer components than other winding arrangements, it makes it possible to build a transformer at a lower cost.
How does a parallel winding arrangement differ from a series winding arrangement in a high-frequency transformer?
The main and secondary windings of a high-frequency transformer are linked together in a parallel circuit when using a parallel winding arrangement. This indicates that the transformer’s load and input voltage source are linked in parallel. A series winding configuration, on the other hand, connects the main and secondary windings in a single circuit.
The way the two coil configurations impact the transformer’s voltage and current is the main distinction between them. The voltage across the main and secondary windings in a parallel winding configuration is the same, whereas the current in each winding is proportional to the number of turns in the winding. In other words, the output voltage is identical to the input voltage and the transformer only offers a current gain—not a voltage gain.
On the other hand, in a series winding configuration, the current through both windings is the same, but the voltage across the main and secondary windings is proportional to the number of turns in each winding. The output voltage is greater than the input voltage, indicating that the transformer gives a voltage gain but not a current gain.
The way the two winding configurations impact the transformer’s impedance is another distinction between them. The transformer’s low impedance in a parallel winding configuration makes it ideal for high current applications. In comparison, the transformer’s impedance is high in a series winding configuration, making it appropriate for high voltage applications.
In a nutshell, the decision between a parallel and series winding configuration in a high-frequency transformer is based on the particular requirements of the application, such as the intended voltage and current levels, the available input voltage, and the load impedance.
What are the advantages and disadvantages of using a bifilar winding arrangement in a high-frequency transformer?
A type of winding arrangement called a bifilar winding arrangement involves winding two different wires in parallel and near proximity. The following are some benefits and drawbacks of a bifilar coil configuration in a high-frequency transformer:
Advantages:
- Lessened leakage inductance: Bifilar coil can lessen leakage inductance, boosting the transformer’s effectiveness.
- Tighter coupling: Bifilar winding causes the primary and secondary windings to be more tightly coupled, which can enhance the efficiency of the transformer.
- Bifilar winding can decrease parasitic capacitance between the windings, which can enhance the transformer’s high-frequency response.
Disadvantages:
- More challenging to wind: Winding a bifilar takes precision and care, which can be more challenging than winding a single wire.
- Greater resistance: By doubling the wire’s resistance, bifilar winding can raise costs and lower efficiency.
- Higher price: Since a bifilar winding needs more wire, the transformer’s price may go up.
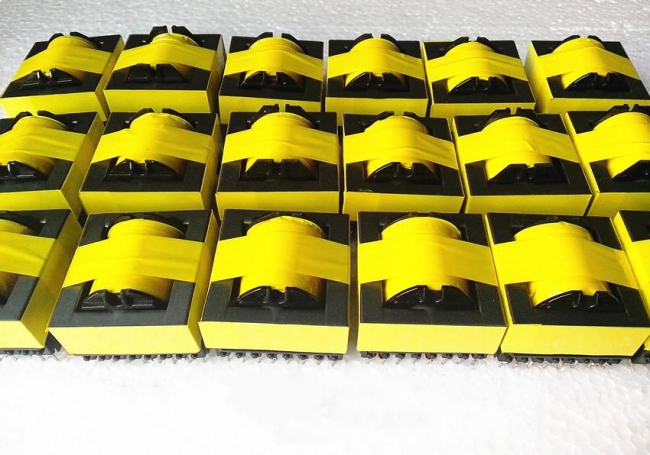
How does the selection of the winding configuration in a high-frequency transformer depend on the frequency of the incoming voltage?
When selecting the winding configuration for a high-frequency transformer, the frequency of the incoming voltage is a crucial factor. The following are some ways in which the incoming voltage’s frequency can influence the winding arrangement:
- Skin effect: The skin effect can result in current being focused on the wire’s surface at high frequencies, which reduces the wire’s useful cross-sectional area. Due to increased resistance and wire losses, the transformer’s efficiency may be impacted. For this reason, at high frequencies, litz wire or other winding arrangements that reduce skin effect may be favored.
- Eddy current losses: Eddy currents can be induced in the conductive materials of the transformer at high frequencies, which results in extra losses. Eddy current impacts can be diminished by specific winding configurations, such as helical winding.
- Capacitance: The capacitance between the transformer’s winding sections can play a big role at high frequencies. Bifilar winding can lower capacitance while layered winding can enhance it.
- Leakage inductance: The frequency of the input voltage may also have an impact on the transformer’s leakage inductance, which may have an impact on the transformer’s efficiency. Bifilar winding can lower leakage inductance, whereas layered winding can raise it.
What factors should be considered when designing a high-frequency transformer with a specific winding arrangement?
The coil configuration must be carefully taken into account when designing a high-frequency transformer. When designing a high-frequency transformer with a particular winding configuration, some important variables to take into account are as follows:
- Frequency: The transformer’s working frequency must be taken into consideration when deciding on the winding configuration. To accomplish the desired inductance and impedance at the operating frequency, the winding’s turn count and wire diameter must be carefully chosen.
- Voltage and current requirements: The transformer’s voltage and current specifications will determine the number of turns in each winding and the necessary cable size. To handle the increased power, a higher voltage or current will take more turns and a larger wire diameter.
- Core material: The transformer’s winding arrangement will also be influenced by the sort of core material used in the device. High-frequency transformers frequently use ferrite cores, which call for specific winding configurations to work at their best.
- Interwinding capacitance: Signal loss and decreased transformer effectiveness can result from interwinding capacitance, which is a problem with high-frequency transformers. To reduce interwinding capacitance and keep signal integrity, the winding arrangement must be meticulously chosen.
- Efficiency: For high-frequency uses, the transformer’s efficiency is crucial. To minimize power losses and increase energy transfer between the windings, the winding arrangement must be optimized.
High-frequency transformers can produce a lot of heat, which can affect their performance and longevity. In order to guarantee proper cooling and avoid overheating, the winding arrangement must be created.