This article delves into the reasons behind this widespread issue as well as the solutions that can be implemented to fix it. It investigates the causes of DC losses in high-frequency transformers and provides some of the more workable solutions. Acquire a deeper comprehension of the underlying mechanisms that are responsible for DC losses in transformers and learn effective methods that can be used to mitigate or prevent these losses. This enlightening article is an absolute necessity to read in its entirety if your goal is to improve the efficiency and dependability of high-frequency transformers.
What is DC loss?
DC loss, which is also called direct current loss, is the loss of energy in a device or circuit caused by direct current. In the case of high-frequency transformers, DC loss is the energy lost as heat in the windings or core of the transformer when a direct current part of the electrical signal is present. This energy loss can make the transformer less effective and may cause it to break down over time.To improve their performance and make them last longer, high-frequency transformers should have as little DC loss as possible.
What are the causes of DC loss in high-frequency transformers?
There are several causes of DC (direct current) loss in high-frequency transformers. Some of the common causes are:
- Core losses: As was already said, one of the main reasons why high-frequency transformers lose DC power is because of core losses. These losses are caused by the energy that is lost as heat in the transformer’s magnetic core.Hysteresis and eddy current losses in the material of the core cause energy to be lost and heat to be produced.
- Skin effect: When AC current flows through a conductor, the skin effect happens. In high-frequency transformers, the skin effect makes the current concentrate near the surface of the conductor. This makes the cross-sectional area of the conductor smaller. This results in increased resistance and energy loss.
- Proximity effect: Another thing that can happen when AC current flows through a conductor is the proximity effect. In high-frequency transformers, the magnetic fields of conductors next to each other interfere with each other because of the proximity effect.This increases resistance and wastes energy.
- Leakage flux: Leakage flux is the magnetic flux that does not link the primary and secondary windings of a transformer. Leakage flux can cause energy loss in high-frequency transformers because it makes heat but doesn’t help move energy between the windings.
- Parasitic capacitance: parasitic capacitance refers to the capacitance that exists between the different parts of a transformer, such as between the windings and the core. In high-frequency transformers, parasitic capacitance can cause energy loss as it results in capacitive reactance that reduces the effective impedance of the transformer.
To minimize DC losses in high-frequency transformers, it is important to consider these factors during the design and construction processes. Optimal material selection, winding configuration, and insulation techniques can help reduce DC losses and improve transformer efficiency.

How do DC losses affect the performance of high-frequency transformers?
DC losses in high-frequency transformers can have several negative effects on their performance. First, DC losses cause a reduction in the efficiency of the transformer, as the energy that is lost as heat is not available for useful work. This can result in increased power consumption and decreased output power. Second, DC losses can lead to increased operating temperatures in the transformer, which can cause thermal stress and potentially lead to premature failure. Third, DC losses can cause distortion in the electrical signal passing through the transformer, which can negatively impact the quality of the output signal. Overall, minimizing DC losses in high-frequency transformers is critical to achieving optimal performance and reliability.
What are some common solutions to reduce DC losses in high-frequency transformers?
There are several common solutions to reduce DC losses in high-frequency transformers, including:
- Using high-quality magnetic materials in the transformer’s core, such as laminated steel or ferrite, to minimize core losses.
- Increasing the number of windings in the transformer to reduce winding resistance and decrease copper losses.
- Using larger wire gauge for the windings to decrease resistance and reduce copper losses.
- Minimizing the amount of direct current in the electrical signal passing through the transformer.
- Using a filtering circuit to remove any direct current component from the input signal before it reaches the transformer.
- Implementing active or passive cooling systems to dissipate the heat generated by DC losses.
- Optimizing the transformer’s design to reduce eddy current losses and hysteresis losses.
- Using a soft magnetic material for the transformer’s core to reduce core losses.
- Choosing a transformer with a higher voltage rating to reduce resistive losses.
- Performing regular maintenance and inspections to identify and address any issues that may contribute to DC losses over time.
How can I test for DC losses in my high-frequency transformer?
To test for DC losses in a high-frequency transformer, you can perform a simple DC resistance test using a multimeter. For this test, a direct current is run through the transformer while the resistance of its windings is measured.
To perform the test, follow these steps:
Step 1: Disconnect the transformer from the power source and any other circuits.
Step 2: Set your multimeter to measure resistance.
Step 3: Place the multimeter leads on the transformer’s primary and secondary windings, one lead on each end.
Step 4: Turn on the power supply and pass a small direct current through the transformer.
Step 5: Observe the multimeter reading and record the value.
Step 6: Repeat the test for each winding and compare the results to the transformer’s specifications.
If the resistance readings are much higher than what the transformer is supposed to be, this could mean that the transformer has DC losses.However, it’s important to note that this test may not be able to identify all types of DC losses, and additional testing may be necessary to fully evaluate the transformer’s performance.
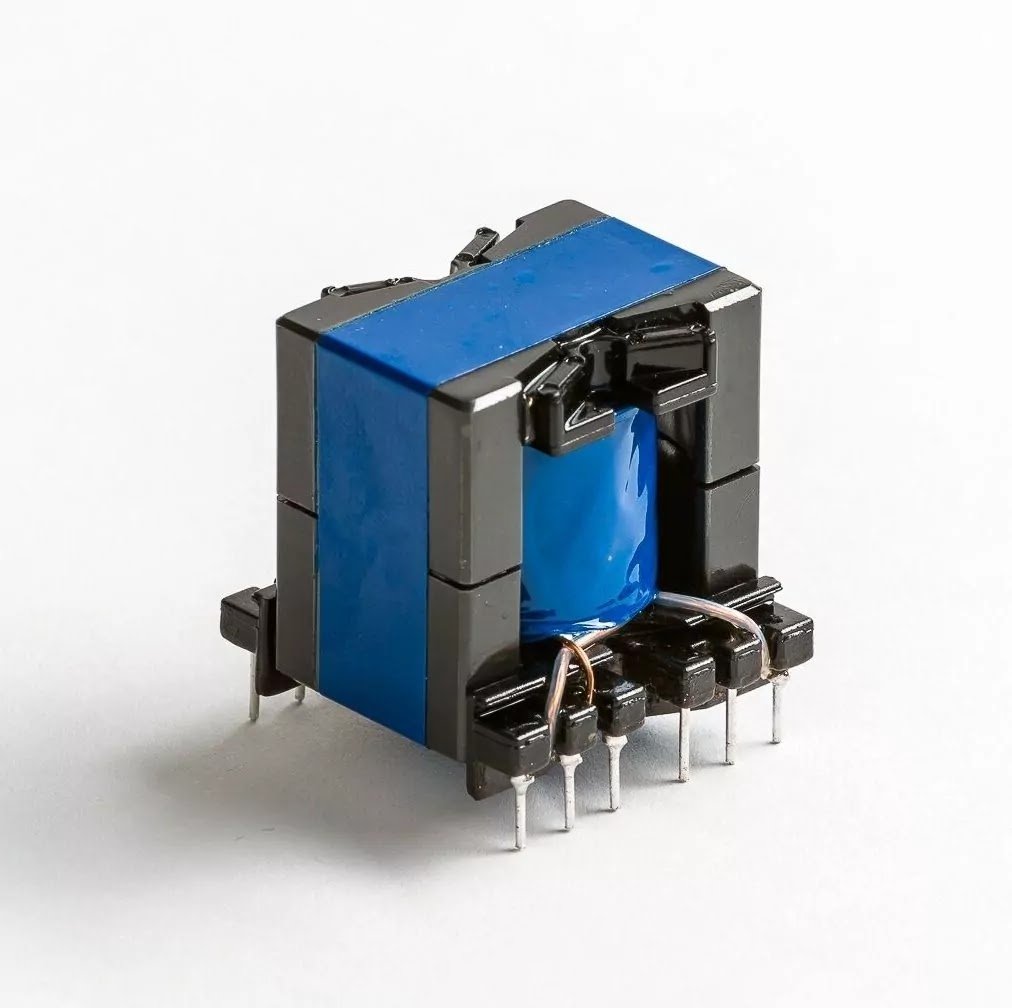
How can I optimize the efficiency of my high-frequency transformer?
There are several ways to optimize the efficiency of a high-frequency transformer:
- Choose high-quality magnetic materials for the transformer’s core, such as laminated steel or ferrite, to minimize core losses.
- Design the transformer with a high fill factor, which is the ratio of copper to core volume, to reduce winding resistance and decrease copper losses.
- Use a larger wire gauge for the windings to reduce resistance and copper losses.
- Reduce the number of windings in the transformer to decrease losses due to leakage inductance and winding capacitance.
- Minimize the amount of direct current in the electrical signal passing through the transformer.
- Implement a filtering circuit to remove any direct current component from the input signal before it reaches the transformer.
- Choose a transformer with a higher voltage rating to reduce resistive losses.
- Implement active or passive cooling systems to dissipate the heat generated by losses.
- Optimize the transformer’s design to reduce eddy current losses and hysteresis losses.
- Perform regular maintenance and inspections to identify and address any issues that may impact the transformer’s efficiency over time.
- By implementing these strategies, you can improve the efficiency of your high-frequency transformer and minimize energy losses.
Can DC losses be completely eliminated in high-frequency transformers?
It is not possible to get rid of all DC losses in high-frequency transformers because the resistance of the windings and core means that some energy is always lost as heat.But DC losses can be kept to a minimum to a large extent through careful design and choice of materials, as well as through the use of good cooling and filtering systems.
By reducing DC losses, the transformer’s efficiency and performance can be greatly improved. This means that the transformer will use less energy, make less heat, and have better output quality.But it’s important to keep in mind that optimizing for the least amount of DC losses may not always be the most cost-effective solution, as it may require using expensive materials or complex design features.So, the best way to do something will depend on the needs and limitations of each application.
How can I choose the best high-frequency transformer for my application to minimize DC losses?
There are a few things to think about to choose the best high-frequency transformer for your application and minimize DC losses:
- Frequency: The transformer’s frequency range should match the frequency of the electrical signal it will be handling. Using a transformer with a frequency range outside of the signal’s range can result in significant DC losses.
- Core material: Choose a core material that has low hysteresis and eddy current losses. Common core materials include laminated steel, ferrite, and amorphous metal.
- Copper wire gauge: Use a larger wire gauge for the transformer’s windings to reduce winding resistance and copper losses.
- Transformer design: Choose a transformer with a high fill factor and fewer windings to minimize copper losses due to winding resistance.
- Cooling: Implement an effective cooling system to dissipate heat generated by losses and prevent overheating.
- Filtering: Use a filtering circuit to remove any direct current component from the input signal to minimize DC losses.
- Efficiency: Look for transformers with high efficiency ratings, which are typically specified as a percentage of input power that is converted into usable output power.
By taking these things into account, you can choose a high-frequency transformer that is best for your application and has the least amount of DC losses, which will improve its performance and efficiency.