Magnetic cores are a vital component in the design of high-frequency transformers, enabling efficient energy transfer between the primary and secondary windings. They play a critical role in determining the transformer’s performance and are often one of the most significant cost factors in the design process. As such, reducing the cost of magnetic cores is crucial to designing high-quality and affordable transformers.
At the same time, it’s essential to maintain the required performance levels, such as low losses, high permeability, and low magnetic saturation, to ensure that the transformer operates as intended. Achieving the right balance between cost and performance is key to creating a successful high-frequency transformer design.
In this blog post, we’ll explore some strategies for reducing magnetic core costs in high-frequency transformer design, without compromising on performance. By implementing these strategies, you can design efficient and cost-effective transformers that meet your specific needs.
Why is reducing magnetic core costs important in high-frequency transformer design?
Reducing magnetic core costs is important in high-frequency transformer design for several reasons:
- Cost-effectiveness: Magnetic cores can be a significant portion of the total cost of a high-frequency transformer. By reducing the cost of the magnetic core, the overall cost of the transformer can be reduced, making it more cost-effective.
- Efficiency: Magnetic cores play a critical role in the efficiency of a high-frequency transformer. The magnetic core is responsible for storing energy during the input cycle and releasing it during the output cycle. If the magnetic core is not designed properly or is too expensive, it can reduce the efficiency of the transformer, resulting in more energy losses and decreased performance.
- Size and weight: High-frequency transformers are often used in compact and lightweight devices such as power supplies and electronic equipment. By reducing the size and weight of the magnetic core, the overall size and weight of the transformer can be reduced, making it more suitable for use in these types of applications.
- Performance: The performance of a high-frequency transformer is dependent on the properties of the magnetic core. By reducing the cost of the magnetic core, it becomes possible to use higher quality materials in the core that can improve the performance of the transformer, such as reducing core losses or increasing the magnetic flux density.
What are the factors affecting magnetic core costs?
Several factors can affect the cost of magnetic cores used in high-frequency transformer design. Some of these factors include:
- Material cost: The cost of magnetic core materials, such as iron, nickel, cobalt, or various alloys, can significantly affect the cost of the core. Some materials are more expensive than others due to their availability, complexity of the manufacturing process, or desirable magnetic properties.
- Manufacturing process: The manufacturing process used to create the magnetic core can also impact its cost. The process may involve stamping, casting, extrusion, or other techniques, each with its own set of associated costs.
- Size and shape: The size and shape of the magnetic core can affect its cost, as larger cores require more material and may have more complex shapes that increase manufacturing costs.
- Frequency of operation: The operating frequency of the high-frequency transformer can also impact the cost of the magnetic core. Higher frequency transformers require cores with higher permeability and lower losses, which may be more expensive than those used in lower frequency transformers.
- Supplier and market conditions: The availability of materials and competition among suppliers in the market can impact the cost of magnetic cores. Changes in the supply chain or market demand can lead to fluctuations in pricing.
How to reduce magnetic core costs in high-frequency transformer design?
1.Material Selection
Material selection is a critical factor in reducing magnetic core costs in high-frequency transformer design. The choice of magnetic core material can significantly impact the overall cost of the transformer. Here are some ways to reduce costs through material selection:
- Identify cost-effective materials: When selecting magnetic core materials, it is important to consider the cost of the material relative to its magnetic properties. Some materials may be less expensive than others but may not have desirable magnetic properties, such as high permeability or low losses. By identifying cost-effective materials with acceptable magnetic properties, it is possible to reduce the cost of the magnetic core.
- Consider alternative materials: There may be alternative materials that can be used in place of traditional magnetic core materials, such as iron or nickel alloys. For example, amorphous and nanocrystalline magnetic alloys have become increasingly popular due to their high magnetic permeability, low losses, and lower material costs compared to traditional magnetic materials.
- Optimize the geometry of the magnetic core: The geometry of the magnetic core can significantly impact its magnetic properties and cost. By optimizing the geometry of the core, such as its shape or size, it is possible to reduce the amount of material required to achieve the desired magnetic properties. This can result in a lower overall cost for the magnetic core.
- Use thinner laminations: The magnetic core is typically made up of thin laminations of magnetic material, which are stacked together. Thinner laminations can reduce the amount of material required to make the magnetic core, thus lowering the cost. However, thinner laminations may increase manufacturing costs due to the difficulty in handling and assembling them.
- Consider the manufacturing process: The manufacturing process used to create the magnetic core can also impact the cost of the core. Some manufacturing processes may be more expensive than others, such as casting versus stamping. By selecting a cost-effective manufacturing process, it is possible to reduce the overall cost of the magnetic core.
2.Core Optimization
Core optimization is a key factor in reducing magnetic core costs in high-frequency transformer design. By optimizing the magnetic core design, it is possible to achieve the desired magnetic properties while using less material, resulting in a lower cost. Here are some ways to optimize the magnetic core design:
- Reduce the core size: The size of the magnetic core is directly proportional to the amount of material used, and therefore, the cost. By reducing the size of the core while maintaining the desired magnetic properties, it is possible to use less material, resulting in a lower cost.
- Optimize the core shape: The shape of the magnetic core can also impact its magnetic properties and cost. By optimizing the shape of the core, such as using a toroidal or E-I shape, it is possible to improve its magnetic properties and reduce the amount of material required.
- Use higher-permeability materials: Magnetic cores with higher permeability require less material to achieve the desired magnetic properties. By using higher-permeability materials, it is possible to reduce the amount of material required, resulting in a lower cost.
- Optimize the winding configuration: The winding configuration of the transformer can also impact the magnetic properties and cost of the core. By optimizing the winding configuration, such as using a multi-layer winding instead of a single-layer winding, it is possible to achieve the desired magnetic properties with less material, resulting in a lower cost.
- Minimize air gaps: Air gaps in the magnetic core can significantly impact its magnetic properties and cost. By minimizing the air gaps, it is possible to improve the magnetic properties of the core while using less material, resulting in a lower cost.
- Use interleaved windings: Interleaved windings can improve the magnetic properties of the core while reducing the amount of material required. By interleaving the windings, it is possible to reduce the leakage inductance of the transformer and use less material, resulting in a lower cost.
3.Utilization Improvement
Utilization improvement is an important factor in reducing magnetic core costs in high-frequency transformer design. Utilization refers to the ratio of the power delivered to the load to the power drawn from the source. A higher utilization means that more of the energy is being effectively used, reducing the overall amount of energy required and, therefore, the size of the transformer core. Here are some ways to improve utilization:
- Increase the turns ratio: Increasing the turns ratio of the transformer can improve its utilization, resulting in a smaller magnetic core size. By increasing the number of turns on the secondary winding, it is possible to increase the output voltage while reducing the input current, resulting in a higher utilization.
- Use high-frequency switching: High-frequency switching can improve the efficiency of the transformer and its utilization. By using high-frequency switching, it is possible to reduce the size of the transformer and its core, resulting in a lower cost.
- Use resonant circuits: Resonant circuits can improve the efficiency of the transformer by reducing the amount of power lost during switching. By using resonant circuits, it is possible to increase the utilization of the transformer, resulting in a smaller magnetic core size.
- Increase the power density: Increasing the power density of the transformer can improve its utilization and reduce the size of the magnetic core. By increasing the amount of power that can be delivered per unit of volume, it is possible to reduce the overall size of the transformer and its core, resulting in a lower cost.
- Use advanced materials: Advanced materials, such as nanocrystalline or amorphous magnetic alloys, can improve the efficiency of the transformer and its utilization. By using advanced materials with high permeability and low losses, it is possible to reduce the size of the transformer and its core, resulting in a lower cost.
4.Manufacturing Process Optimization
Magnetic core costs in high-frequency transformer design can be reduced through various means, including optimizing the manufacturing process. Here are some ways manufacturing process optimization can help reduce magnetic core costs in high-frequency transformer design:
- Material Selection: Choosing the right material for the core is critical to reducing costs. The core material should have low hysteresis and eddy current losses, which can be achieved through careful selection of materials such as laminated silicon steel or ferrite cores. The optimal material selection can be made based on the transformer’s operating frequency, power requirements, and other design factors.
- Core Design: The design of the core can also impact manufacturing costs. By optimizing the design of the core to minimize the amount of material needed, costs can be reduced. This can be achieved through techniques such as using toroidal cores, which have a higher packing density and therefore require less material, or by using stacked laminations rather than solid cores.
- Manufacturing Process: The manufacturing process itself can also be optimized to reduce costs. This can be done through techniques such as using automated manufacturing processes that reduce the amount of labor required and minimize material waste. It can also involve improving the quality of the manufacturing process to reduce the number of defective cores produced, thereby reducing scrap and rework costs.
- Quality Control: Implementing quality control measures can also help reduce costs. By detecting and addressing defects early in the manufacturing process, scrap and rework costs can be minimized. Quality control measures can include visual inspections, testing of the magnetic properties of the cores, and statistical process control.

How can I improve core utilization to reduce costs?
Core utilization refers to the effective use of the magnetic core in a transformer design. The higher the core utilization, the less core material is required, which can help reduce costs. Here are some ways to improve core utilization:
- Reduce Air Gap: The air gap between the core and winding can reduce core utilization by increasing the magnetic reluctance of the circuit. By minimizing the air gap, the magnetic flux can be concentrated in the core, increasing its utilization. This can be achieved through careful design of the winding and insulation system.
- Increase Winding Density: Increasing the winding density can help improve core utilization by reducing the amount of space between the windings and the core. This can be achieved through techniques such as using stranded wire, interleaved windings, or multiple layers of winding.
- Optimize Core Design: The design of the core itself can also impact core utilization. Using toroidal cores or stacked laminations can increase the packing density of the core, reducing the amount of material required and improving core utilization.
- Use High-Permeability Material: High-permeability core materials can help increase core utilization by allowing more flux to flow through the core. This can be achieved through the use of materials such as laminated silicon steel or ferrite cores.
- Minimize Fringing Flux: Fringing flux refers to the magnetic field lines that extend outside the core. By minimizing fringing flux, more flux can be directed through the core, improving core utilization. This can be achieved through careful design of the winding and insulation system.
What manufacturing processes can help to reduce magnetic core costs?
There are several manufacturing processes that can help to reduce magnetic core costs:
- Design optimization: The first step to reduce magnetic core costs is to optimize the design. This can be done by choosing the most suitable magnetic material, determining the optimal shape and size of the core, and minimizing the number of turns required in the winding.
- Material selection: The choice of magnetic material can have a significant impact on the cost of the core. Using lower-cost magnetic materials can help to reduce costs, but this must be balanced against the desired performance requirements.
- Bulk purchasing: Buying magnetic core materials in bulk can help to reduce costs. Manufacturers may be able to negotiate better prices with suppliers by purchasing larger quantities.
- Automation: Automating the manufacturing process can help to reduce labor costs and increase efficiency. This can include the use of automated machinery and robots to perform repetitive tasks.
- Lean manufacturing: Implementing lean manufacturing principles can help to reduce waste, increase efficiency, and reduce costs. This involves identifying and eliminating unnecessary steps in the manufacturing process, reducing inventory, and streamlining production.
- Recycling: Recycling magnetic core materials can help to reduce costs by reducing the amount of waste generated during the manufacturing process. This can include reusing scrap material and recycling old cores.
- Outsourcing: Outsourcing the manufacturing process to a lower-cost location can help to reduce labor costs. However, this must be balanced against the potential for increased shipping costs and longer lead times.
How do I balance cost and performance when designing a high-frequency transformer?
Designing a high-frequency transformer requires balancing cost and performance. Here are some steps you can take to achieve this balance:
- Define the performance requirements: The first step is to define the performance requirements for your high-frequency transformer. This includes factors such as the required power output, efficiency, operating frequency range, and temperature range. Once you have defined the performance requirements, you can select the most cost-effective materials and manufacturing processes that meet those requirements.
- Choose the right core material: The core material plays a critical role in the performance of a transformer. Selecting the right core material can help to achieve the desired performance at a reasonable cost. Ferrite and powdered iron are commonly used in high-frequency transformers due to their high permeability and low losses.
- Optimize the transformer design: The design of the transformer can also impact its cost and performance. You can optimize the design by selecting the right winding configuration, the number of turns, and the wire size. Using simulation tools can help you optimize the design for maximum efficiency and minimal cost.
- Consider manufacturing processes: The manufacturing processes used to produce the transformer can also impact its cost. For example, automated winding processes can reduce labor costs, while batch processing can reduce material costs. Choosing the right manufacturing processes can help to minimize the cost of the transformer without sacrificing performance.
- Perform cost-benefit analysis: It’s essential to perform a cost-benefit analysis to determine the most cost-effective design. This involves comparing the cost of different designs against their performance to identify the most cost-effective option that meets your requirements.
By following these steps, you can balance cost and performance when designing a high-frequency transformer, ensuring that you achieve the desired performance at a reasonable cost.
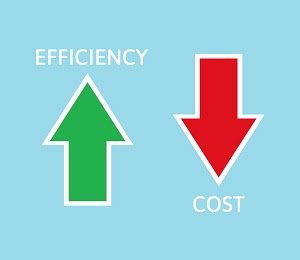
Can I still achieve high performance while reducing magnetic core costs?
Yes, it is possible to achieve high performance while reducing magnetic core costs by optimizing the design of the magnetic circuit. Magnetic cores are an important component in many electrical devices, including transformers and inductors. They provide a low reluctance path for the magnetic flux, which is necessary for efficient operation of these devices.
One way to reduce the cost of magnetic cores is to optimize the design of the core itself. This can involve choosing the appropriate core material, selecting the appropriate size and shape of the core, and using advanced modeling techniques to predict the behavior of the core.
In addition, it is important to minimize the amount of material used in the core, without compromising the performance of the device. This can be achieved by using advanced winding techniques, such as interleaving or layering, to maximize the amount of copper wire that can be wound on the core.
Furthermore, reducing the size of the core can also help to reduce the cost of the device. This can be achieved by using high-frequency switching techniques, which allow for smaller magnetic cores to be used, without sacrificing performance.
What are some case studies that demonstrate successful implementation of strategies to reduce magnetic core costs?
Here are a couple of case studies that demonstrate successful implementation of strategies to reduce magnetic core costs:
Case Study 1: Core Reduction in a Power Transformer
A manufacturer of power transformers needed to reduce the cost of the transformer cores without sacrificing performance. They achieved this by optimizing the design of the core, which involved using thinner laminations and reducing the cross-sectional area of the core. The design also included interleaving of the windings to maximize the use of the available space in the core.
The result was a 20% reduction in the cost of the transformer cores without sacrificing performance. The transformers met all the required standards and were able to handle the same power output as the previous design.
Case Study 2: Using Nanocrystalline Cores to Reduce Core Costs
A manufacturer of inductors needed to reduce the cost of the magnetic cores used in their products. They achieved this by switching to nanocrystalline cores, which are made of a high-permeability magnetic material that is less expensive than traditional core materials.
The nanocrystalline cores also provided higher performance than the previous cores, with lower losses and higher saturation flux density. This resulted in a 30% reduction in the cost of the cores, while also improving the performance of the inductors.
Overall, these case studies demonstrate that it is possible to successfully implement strategies to reduce magnetic core costs without sacrificing performance or reliability. By optimizing the design of the core, using advanced materials, and maximizing the use of available space, manufacturers can achieve significant cost savings while still meeting the requirements of their products.
How do I choose a manufacturing partner that can balance cost and quality?
Choosing a manufacturing partner that can balance cost and quality is an important decision that can have a significant impact on the success of your product. Here are some tips to help you choose the right manufacturing partner:
- Look for experience and expertise: Look for a manufacturer who has experience in your industry and has expertise in the specific manufacturing processes required for your product. This can help ensure that the manufacturer can produce your product efficiently and effectively.
- Consider their capabilities: It is important to ensure that the manufacturer you choose has the capabilities to produce your product at the required volume, quality, and cost. Ask for samples or prototypes to assess their quality standards and evaluate their production process to ensure it meets your requirements.
- Evaluate their pricing model: Ask for detailed pricing information from the manufacturer, including all costs involved in the production process. This will help you understand their pricing model and determine whether they can produce your product at a cost that works for your budget.
- Check their references: Ask the manufacturer for references from previous clients and speak to them about their experience working with the manufacturer. This can give you an idea of the manufacturer’s quality standards, delivery times, and customer service.
- Communication and transparency: Ensure the manufacturer communicates with you transparently and frequently throughout the manufacturing process. This can help to avoid misunderstandings and ensure that you are kept up-to-date with any changes or issues that arise.
Are there any trade-offs to consider when implementing strategies to reduce magnetic core costs?
Yes, there are trade-offs to consider when implementing strategies to reduce magnetic core costs. Here are some of the key trade-offs to keep in mind:
- Performance: One of the main trade-offs to consider is the impact of cost reduction strategies on the performance of the device. For example, reducing the size of the core may result in increased losses, which can affect the overall efficiency of the device. Therefore, it is important to carefully evaluate the impact of cost reduction strategies on the performance of the device.
- Reliability: Another trade-off to consider is the impact of cost reduction strategies on the reliability of the device. For example, reducing the size of the core may result in increased thermal stresses, which can affect the long-term reliability of the device. Therefore, it is important to carefully evaluate the impact of cost reduction strategies on the reliability of the device.
- Complexity: Some cost reduction strategies, such as interleaving or layering of windings, can increase the complexity of the manufacturing process, which can affect the overall cost and time required to produce the device. Therefore, it is important to carefully evaluate the impact of cost reduction strategies on the complexity of the manufacturing process.
- Material availability: Choosing a less expensive core material may be a cost-effective option, but it could also result in supply chain challenges or longer lead times for the materials, which can affect the overall cost and time required to produce the device.
- Design flexibility: Some cost reduction strategies, such as using a standardized core size, may limit the design flexibility of the device, which can affect its overall functionality and performance.
In conclusion, reducing magnetic core costs is a critical aspect of designing high-quality and affordable high-frequency transformers. By implementing cost reduction strategies such as optimizing the core design, using advanced materials, and maximizing the use of available space, manufacturers can achieve significant cost savings without sacrificing performance or reliability. These cost savings can ultimately lead to more affordable and accessible high-frequency transformers, which can benefit a wide range of industries and applications. As such, it is important for designers and manufacturers to prioritize cost reduction strategies when designing high-frequency transformers, in order to create products that are both high-quality and affordable.