High-frequency transformers are vital components in various electrical systems, playing a crucial role in power conversion, signal amplification, and voltage regulation. They are widely used in industries such as telecommunications, power electronics, and renewable energy. The efficient operation of these transformers is essential for the reliable performance of countless devices and equipment.
However, high-frequency transformers are not immune to challenges, and one significant problem that can arise is ignition and arcing. Ignition refers to the sudden onset of a high-energy electrical discharge, while arcing is the sustained flow of current through an ionized air path. These phenomena can lead to severe consequences, including damage to the transformer, disruption of electrical systems, and even the risk of fire or electrical hazards.
In this blog, we will explore practical measures to effectively deal with high-frequency transformer ignition and arcing. We will discuss preventive measures that can be implemented to reduce the risk of ignition and arcing events. Additionally, we will outline the immediate actions to take in the event of ignition or arcing, emphasizing the importance of professional assistance and comprehensive inspections to determine the root cause and prevent future occurrences.
What causes ignition and arcing in high-frequency transformers?
Ignition and arcing in high-frequency transformers can be caused by various factors. Here are 7 common causes:
- Overheating: Excessive heat buildup within the transformer can lead to insulation degradation and eventual ignition. This can occur due to factors like inadequate cooling, overloading, or poor thermal management.
- Insulation breakdown: Over time, the insulation materials used in transformers can deteriorate due to factors such as moisture, dirt, or aging. When the insulation breaks down, it can create gaps or weak points that facilitate arcing.
- Contamination: The presence of conductive contaminants, such as dust, dirt, or conductive particles, can lead to arcing within the transformer. These contaminants can cause insulation breakdown and create paths for electrical discharge.
- Voltage spikes: High-voltage surges or spikes can occur due to lightning strikes, power grid disturbances, or faulty electrical equipment. These sudden increases in voltage can cause arcing if the transformer is unable to handle the excess energy.
- Poor design or manufacturing defects: Transformers with design flaws or manufacturing defects may be more prone to ignition and arcing. Issues such as inadequate insulation, improper winding techniques, or poor component quality can increase the risk of these problems.
- Incorrect installation or maintenance: Improper installation or inadequate maintenance practices can contribute to ignition and arcing. Inadequate grounding, incorrect wiring, loose connections, or neglecting routine inspections can all lead to electrical faults and arcing.
- Mechanical stress: Mechanical stresses, such as vibrations, shocks, or physical damage, can weaken the insulation or create electrical contact points where arcing can occur.
What are the signs or symptoms of ignition and arcing in a transformer?
There are 7 signs and symptoms that can indicate the presence of ignition and arcing in a transformer. These include:
- Unusual noises: Ignition and arcing can produce audible sounds such as buzzing, crackling, or humming. These noises may be heard from the transformer or associated electrical equipment.
- Odor: The occurrence of ignition and arcing can produce a distinct burning or ozone-like smell. If you detect a strong, unusual odor near the transformer, it may indicate a problem.
- Visible sparks or flashes: In some cases, you may actually see sparks or flashes of light coming from the transformer. These visual indications are clear signs of arcing and should be addressed immediately.
- Heat generation: Ignition and arcing can cause excessive heat buildup within the transformer. If you notice that the transformer feels unusually hot to the touch or if nearby components or enclosures are abnormally warm, it could be a sign of a problem.
- Tripping of circuit breakers or fuses: When arcing occurs, it can cause short circuits or overloads, leading to the tripping of circuit breakers or blowing of fuses. If you frequently experience tripped breakers or blown fuses associated with the transformer, it may be a sign of arcing.
- Voltage fluctuations or interruptions: Ignition and arcing can disrupt the electrical flow within the transformer, resulting in voltage fluctuations or complete power interruptions. If you observe inconsistent or unstable voltage levels, it could indicate a problem with the transformer.
- Abnormal operation of equipment: Arcing and ignition can impact the performance of equipment connected to the transformer. You may notice flickering lights, malfunctioning machinery, or other irregularities that can be attributed to electrical disturbances caused by arcing.
If you observe any of these signs or symptoms, it is crucial to take immediate action. Ignition and arcing pose serious safety risks and can lead to extensive damage to the transformer and surrounding equipment. Contact a qualified professional or an electrical technician to conduct a thorough inspection, diagnose the issue, and carry out the necessary repairs or maintenance to mitigate the problem.
How can I prevent ignition and arcing in high-frequency transformers?
Preventing ignition and arcing in high-frequency transformers requires a combination of proactive measures and adherence to safety guidelines. Here are 10 preventive measures you can implement:
1.Regular maintenance:
Perform regular inspections, cleaning, and maintenance of the transformer to identify and address potential issues before they escalate. This includes checking for signs of insulation degradation, loose connections, or contaminants that can lead to arcing.
2.Follow manufacturer guidelines:
Adhere to the manufacturer’s recommendations and guidelines for installation, operation, and maintenance of the transformer. These guidelines often include specific instructions for proper grounding, cooling, and maintenance procedures.
3.Proper insulation:
Ensure that the transformer has adequate insulation to withstand the high-frequency electrical stresses. High-quality insulation materials and techniques should be used during manufacturing and installation to minimize the risk of ignition and arcing.
4.Adequate cooling:
Proper cooling is essential to prevent overheating and potential ignition. Ensure that the transformer has appropriate cooling mechanisms, such as fans or liquid cooling systems, and that they are functioning correctly.
5.Proper grounding:
Implement proper grounding techniques to ensure the safe dissipation of electrical charges and minimize the risk of arcing. Grounding the transformer and associated electrical equipment effectively reduces the chances of voltage spikes and electrical disturbances.
6.Shielding and enclosure:
Use appropriate shielding and enclosures to protect the transformer from external electromagnetic interference and to contain any potential arcing or ignition. This includes proper placement of the transformer within an adequately designed enclosure.
7.Avoid overloading:
Do not exceed the transformer’s rated capacity to prevent excessive heat buildup and potential ignition. Ensure that the load on the transformer is within its specified limits.
8.Surge protection:
Install surge protection devices, such as surge suppressors or lightning arrestors, to mitigate the risk of voltage spikes caused by external factors like lightning strikes or power grid disturbances.
9.Training and awareness:
Educate personnel working with or around the transformer about the risks associated with ignition and arcing. Train them on safe operating procedures, including how to recognize warning signs and the importance of reporting any abnormalities.
10.Professional assistance:
When in doubt or faced with complex issues, seek professional assistance from qualified electrical engineers or technicians specializing in high-frequency transformers. They can provide expert guidance, conduct thorough assessments, and propose appropriate preventive measures.
What are the potential risks and consequences of ignition and arcing events?
Ignition and arcing events in high-frequency transformers can pose significant risks and lead to various consequences. Here are some potential risks and consequences associated with ignition and arcing:
1.Fire and explosions:
Ignition events can result in fires and explosions, especially if flammable materials are present in the vicinity of the transformer. This poses a severe risk to the safety of personnel, surrounding infrastructure, and can cause extensive damage.
2.Electrical shocks and injuries:
Arcing events can generate high-intensity electrical currents that can cause electrical shocks to anyone in close proximity. These shocks can lead to serious injuries or even fatalities. Personnel working on or near the transformer are particularly at risk.
3.Equipment damage and downtime:
Ignition and arcing can cause significant damage to the transformer itself and other connected electrical equipment. This can result in costly repairs or replacements, leading to downtime in operations and disruptions to critical processes.
4.Power outages:
Ignition and arcing events can cause electrical disturbances, leading to power outages in the affected areas. These outages can result in inconvenience for consumers, loss of productivity for businesses, and potential safety hazards in critical facilities like hospitals or data centers.
5.Reduced system efficiency:
Arcing can cause electrical disturbances such as voltage fluctuations, harmonics, or electrical noise. These disturbances can impact the overall efficiency of the electrical system, leading to poor performance of equipment, increased energy consumption, and potential malfunctions.
6.Environmental impact:
In addition to the immediate risks, ignition events can release harmful substances and pollutants into the environment. Fires and explosions can generate toxic smoke, while electrical failures may result in the release of hazardous materials.
7.Financial losses:
Dealing with the aftermath of ignition and arcing events can result in significant financial losses. The costs associated with repairs, replacements, downtime, and potential legal liabilities can be substantial, impacting the financial stability of individuals or organizations.
It is crucial to recognize these risks and consequences, as they emphasize the importance of addressing and preventing ignition and arcing in high-frequency transformers. By implementing proper safety measures, regular maintenance, and seeking professional assistance, the potential risks and consequences can be minimized, ensuring the safety of personnel, preserving equipment integrity, and maintaining uninterrupted electrical operations.
Can improper insulation lead to ignition and arcing? How can insulation be improved?
Yes, improper insulation can indeed lead to ignition and arcing in high-frequency transformers. Insulation plays a crucial role in preventing electrical current leakage and maintaining the integrity of the electrical system. When insulation is compromised or inadequate, it can result in the following issues:
- Insulation breakdown: Inadequate insulation can degrade over time due to factors such as moisture, dirt, or aging. This breakdown can create gaps or weak points in the insulation, which can lead to arcing and electrical discharge.
- Electrical flashover: Improper insulation can cause electrical flashover, which occurs when the electrical current arcs across the surface of the insulation rather than flowing through it. This can result in electrical disturbances, equipment damage, and safety hazards.
To improve insulation in high-frequency transformers and reduce the risk of ignition and arcing, the following steps can be taken:
- High-quality insulation materials: Ensure that high-quality insulation materials are used during the manufacturing or repair process of the transformer. High-frequency transformers often require specialized insulation materials designed to withstand the specific electrical stresses and operating conditions.
- Proper insulation thickness: The insulation thickness should be designed to handle the voltage and current levels present in the transformer. Insufficient insulation thickness can result in breakdown and arcing, while excessive insulation thickness can lead to increased heat buildup.
- Effective insulation techniques: Employ proper insulation techniques during the manufacturing or repair process. This includes ensuring that the insulation is correctly applied, evenly distributed, and securely fastened. Winding techniques should also be carefully executed to maintain consistent insulation coverage.
- Insulation testing: Regularly perform insulation testing using appropriate methods such as insulation resistance testing or partial discharge measurements. This helps identify any insulation weaknesses or degradation and allows for timely repairs or replacements before they escalate into ignition and arcing issues.
- Moisture and contamination control: Implement measures to prevent moisture ingress and the accumulation of conductive contaminants within the transformer. Proper sealing, adequate ventilation, and regular cleaning help maintain the integrity of the insulation and reduce the risk of arcing.
- Temperature monitoring: Install temperature sensors to monitor the temperature levels of the transformer and its insulation. Excessive heat can degrade insulation and increase the likelihood of ignition and arcing. Monitoring allows for prompt identification of overheating issues and the implementation of corrective measures.
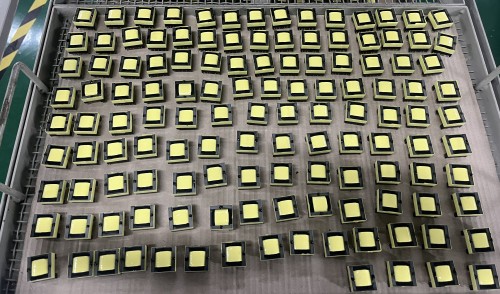
How does grounding and bonding affect the occurrence of ignition and arcing?
Grounding and bonding play crucial roles in preventing the occurrence of ignition and arcing in high-frequency transformers. Here’s how grounding and bonding affect the risk of ignition and arcing:
1.Electrical fault protection:
Proper grounding ensures that electrical faults, such as short circuits or overloads, are safely dissipated to the ground. In the event of a fault, grounding provides a low-resistance path for the electrical current, allowing it to flow away from the transformer and preventing excessive currents that can lead to arcing and ignition.
2.Voltage stabilization:
Grounding helps stabilize the voltage levels within the transformer and the electrical system as a whole. It provides a reference point, or a zero potential, for the electrical system. This helps mitigate voltage imbalances and fluctuations that can contribute to arcing events.
3.Surge and lightning protection:
Grounding systems, including lightning rods and grounding electrodes, help divert excessive electrical energy, such as lightning strikes or power surges, directly to the ground. By providing a low-impedance path, these grounding systems prevent the destructive effects of high voltages that could otherwise cause arcing and subsequent ignition.
4.Reduction of electromagnetic interference:
Proper grounding and bonding help reduce electromagnetic interference (EMI) in the electrical system. EMI can disrupt the proper functioning of sensitive equipment and create conditions that promote arcing and ignition. Grounding and bonding techniques, such as shielding and proper grounding of equipment, help mitigate EMI-related issues.
5.Control of static electricity:
Grounding and bonding also aid in controlling static electricity. In high-frequency transformer systems, static charges can build up and create conditions conducive to arcing. Proper grounding and bonding techniques help dissipate static charges, minimizing the risk of arcing and ignition.
6.Equipment protection:
Grounding and bonding systems protect the transformer and associated electrical equipment from damage. By establishing a common ground reference, these systems help prevent potential differences between grounded and ungrounded parts, reducing the risk of arcing due to voltage imbalances.
It is important to follow proper grounding and bonding practices, including adherence to applicable electrical codes and standards, to ensure effective grounding and minimize the risk of ignition and arcing. Consulting with qualified electrical engineers or technicians who specialize in high-frequency transformers can help ensure the correct implementation of grounding and bonding systems for optimal safety and performance.
Can electromagnetic interference (EMI) contribute to ignition and arcing? How can EMI be mitigated?
Electromagnetic interference (EMI) can contribute to ignition and arcing in high-frequency transformers. EMI refers to the disruption of electrical signals by electromagnetic fields generated by external sources or internal equipment.
Here’s how EMI can contribute to ignition and arcing and how it can be mitigated:
- Insulation breakdown: EMI can induce voltage and current fluctuations in the transformer, which can stress the insulation system. These fluctuations can lead to insulation breakdown, creating paths for arcing and ignition to occur.
- Voltage spikes: EMI can introduce high-voltage spikes or transients in the electrical system. These sudden increases in voltage can exceed the insulation’s breakdown threshold and cause arcing and subsequent ignition.
- Component damage: EMI can cause electrical disturbances that affect the performance of sensitive components within the transformer. These disturbances can damage electronic components, compromise insulation integrity, and increase the risk of arcing and ignition.
To mitigate EMI and reduce the risk of ignition and arcing, the following measures can be taken:
- Shielding: Implement proper shielding techniques to minimize the impact of external electromagnetic fields. Shielding materials, such as conductive enclosures or grounded shields, can help contain and redirect electromagnetic energy away from sensitive areas of the transformer.
- Grounding and bonding: Ensure proper grounding and bonding practices, as mentioned earlier. By establishing a low-impedance path to the ground, grounding and bonding systems help reduce EMI and prevent voltage imbalances that can lead to arcing.
- Filter and suppress EMI: Install filters and suppression devices in the electrical system to attenuate EMI. This includes the use of EMI filters, surge protectors, or ferrite cores to mitigate high-frequency noise and transient voltage spikes.
- Cable routing and separation: Properly route and separate electrical cables to minimize electromagnetic coupling between them. By avoiding close proximity and crossing of cables carrying different signals, the risk of EMI-induced arcing can be reduced.
- Equipment selection: Choose equipment and components that are designed to minimize EMI generation and susceptibility. Opt for products that meet relevant EMI standards and have appropriate shielding and filtering mechanisms built-in.
- EMI testing and compliance: Conduct EMI testing during the design and commissioning stages to identify potential EMI issues. Ensure that the transformer complies with relevant EMI regulations and standards to minimize the risk of ignition and arcing.
What maintenance practices should be followed to prevent ignition and arcing?
To prevent ignition and arcing in high-frequency transformers, it is crucial to follow proper maintenance practices. Regular maintenance helps identify potential issues, address them promptly, and ensure the safe and reliable operation of the transformer. Here are 9 keys maintenance practices to follow:
1.Inspections:
Conduct regular visual inspections of the transformer and associated components. Look for signs of degradation, damage, or contamination that could lead to ignition or arcing. Inspect insulation, connections, cooling systems, and other critical components for any abnormalities.
2.Cleaning:
Keep the transformer and its surroundings clean. Regularly remove dust, dirt, and debris from the transformer to prevent contamination that can compromise insulation or hinder heat dissipation. Pay attention to cooling fins, ventilation openings, and air filters.
3.Insulation testing:
Perform insulation resistance testing or other suitable tests to assess the condition of the insulation system. Insulation testing helps identify insulation degradation, weak points, or potential breakdowns that could lead to arcing. Regular testing allows for timely repairs or replacements.
4.Connection checks:
Ensure all electrical connections, including terminals, busbars, and wiring, are secure and free from corrosion or loose connections. Loose or corroded connections can create resistance, generate heat, and increase the risk of arcing. Verify torque levels and follow manufacturer’s specifications for tightening connections.
5.Cooling system maintenance:
Maintain the cooling system of the transformer in proper working condition. Clean or replace cooling fans, filters, or heat exchangers regularly to ensure optimal heat dissipation. Monitor coolant levels and pressures if a liquid cooling system is used.
6.Lubrication:
If the transformer has moving parts such as fans or mechanical switches, follow manufacturer guidelines for lubrication. Regularly inspect and lubricate these components to ensure smooth operation and prevent mechanical failures that could lead to arcing.
7.Environmental considerations:
Assess the environment in which the transformer is located. Take measures to protect the transformer from excessive humidity, temperature extremes, or corrosive atmospheres. Ensure proper ventilation and adequate clearance around the transformer for proper cooling and maintenance access.
8.Record keeping:
Maintain detailed records of maintenance activities, inspections, and test results. This documentation helps track the maintenance history of the transformer, identify patterns, and plan future maintenance tasks effectively.
9.Professional expertise:
Engage qualified electrical engineers or technicians with expertise in high-frequency transformers for comprehensive inspections and maintenance. They can provide specialized knowledge, perform in-depth assessments, and identify potential issues that may go unnoticed otherwise.
Can ignition and arcing be repaired, or is replacement necessary?
The repair or replacement of a high-frequency transformer depends on the extent of the damage caused by ignition and arcing. In some cases, minor instances of ignition or arcing may be repairable, while severe damage may necessitate replacement. Here are 5 factors to consider when deciding whether repair or replacement is appropriate:
- Extent of damage: Assess the extent of the damage caused by ignition and arcing. If the damage is limited to specific components or localized areas, it may be possible to repair or replace those specific parts while preserving the overall integrity of the transformer.
- Safety considerations: Prioritize safety when evaluating the damage. If the damage compromises the safety of the transformer or poses a risk of future ignition or arcing events, replacement may be necessary to ensure the reliability and safety of the electrical system.
- Cost-effectiveness: Consider the cost-effectiveness of repair versus replacement. Compare the cost of repairs, including labor, parts, and potential downtime, with the cost of a new transformer. In some cases, the cost of repairs may be prohibitive or uneconomical, making replacement a more viable option.
- Age and condition: Take into account the age and overall condition of the transformer. If the transformer is already approaching the end of its expected lifespan or has significant pre-existing issues, replacement may be a more practical choice to avoid recurring problems and ensure long-term reliability.
- Manufacturer recommendations: Consult the manufacturer’s recommendations regarding repairability. Some manufacturers provide guidelines on when repairs are feasible and when replacement is advised based on specific models or types of transformers.
It is crucial to involve qualified electrical engineers or technicians with expertise in high-frequency transformers during the evaluation process. They can assess the damage, provide a professional opinion on the repairability, and offer recommendations on the best course of action.
Ultimately, the decision to repair or replace a high-frequency transformer should be based on a thorough assessment of the damage, safety considerations, cost-effectiveness, and the expertise of professionals.
How frequently should inspections and testing be conducted to identify potential ignition and arcing risks?
The frequency of inspections and testing to identify potential ignition and arcing risks in high-frequency transformers depends on several factors, including the transformer’s size, age, operating conditions, and industry standards or regulations. Here are six general guidelines:
- Regular visual inspections: Conduct visual inspections of the transformer and associated components on a regular basis. The frequency can vary, but a general recommendation is to perform visual inspections quarterly or semi-annually. This allows for the detection of any visible signs of degradation, damage, or contamination that could lead to ignition or arcing.
- Insulation testing: Perform insulation resistance testing or other suitable insulation tests on a periodic basis. The recommended frequency for insulation testing can range from annually to every few years, depending on factors such as the transformer’s criticality, operating conditions, and manufacturer recommendations.
- Maintenance cycles: Coordinate inspections and testing with routine maintenance cycles. For instance, if the transformer undergoes annual maintenance, it is advisable to conduct comprehensive inspections and testing during that maintenance period.
- Criticality and operating conditions: Consider the criticality of the transformer and the severity of the operating conditions it is subjected to. Transformers in high-risk environments or those critical for essential operations may require more frequent inspections and testing. Industries such as power generation, oil and gas, or critical infrastructure may have specific regulations or guidelines mandating inspection frequencies
- Historical performance and maintenance records: Review the historical performance and maintenance records of the transformer. If there have been previous instances of ignition or arcing, it may be necessary to increase the frequency of inspections and testing to closely monitor the transformer’s condition and mitigate any potential risks.
- Manufacturer recommendations and industry standards: Consult the transformer manufacturer’s recommendations and applicable industry standards or guidelines for inspection and testing frequencies. Manufacturers often provide guidelines specific to their products, taking into account their design, materials, and expected lifespan.
In conclusion, dealing with high-frequency transformer ignition and arcing is of paramount importance for the safe and reliable operation of electrical systems. Ignition and arcing events can lead to severe consequences such as equipment damage, power outages, and even fire hazards. It is crucial to take proactive steps to prevent these incidents and prioritize safety above all else.
Above all, safety should always be the top priority. It is essential to prioritize safety in every aspect of dealing with high-frequency transformer ignition and arcing. This includes following industry standards, adhering to manufacturer recommendations, and seeking professional assistance when needed. Qualified electrical engineers or technicians can provide valuable expertise, conduct thorough assessments, and guide you in implementing effective preventive measures.