High frequency transformers play a crucial role in numerous electronic devices and power systems, enabling efficient conversion and distribution of electrical energy. These specialized transformers operate at frequencies beyond the range of traditional power transformers, making them essential for applications such as telecommunications, renewable energy systems, and high-tech industrial equipment. However, like any complex equipment, high frequency transformers are susceptible to failures that can disrupt operations, compromise performance, and lead to costly downtime.
In this blog, we will explore the vital topic of “How to deal with high frequency transformer failure?” We will delve into the importance of these transformers and the common causes behind their failures. By understanding these aspects, we can equip ourselves with the knowledge and strategies needed to effectively address transformer failures and ensure the reliable and optimal operation of high frequency power systems.
What are the main causes of high frequency transformer failure?
The main causes of high frequency transformer failure can vary depending on various factors, including the design, operating conditions, and maintenance practices. Below 8 common causes of high frequency transformer failure include:
1.Overheating:
Overheating is one of the primary causes of transformer failure. It can result from factors such as inadequate cooling systems, excessive loads, poor ventilation, or insufficient thermal management. Prolonged exposure to high temperatures can degrade insulation materials, cause winding deformation, and lead to insulation breakdown, ultimately resulting in transformer failure.
2.Insulation breakdown:
Insulation breakdown can occur due to aging, electrical stresses, environmental factors, or manufacturing defects. When insulation materials deteriorate or fail, it can lead to short circuits, arcing, and electrical faults within the transformer, causing performance issues and eventual failure.
3.Overloading:
Overloading the transformer beyond its rated capacity can lead to increased heat generation, insulation degradation, and accelerated wear and tear on the components. Continuous overloading can cause winding damage, increased resistance, and eventually, transformer failure.
4.Voltage surges:
Sudden voltage surges, such as lightning strikes, power grid disturbances, or switching events, can result in excessive voltage levels that exceed the transformer’s insulation capabilities. These voltage surges can cause insulation breakdown, arcing, and internal faults, leading to transformer failure.
5.Electrical faults:
Internal electrical faults within the transformer, such as short circuits or insulation faults, can cause excessive current flow, overheating, and damage to the transformer components. These faults can result from insulation degradation, manufacturing defects, or external factors like power quality issues.
7.Environmental factors:
Harsh environmental conditions, such as extreme temperatures, humidity, corrosive atmospheres, or exposure to chemicals, can accelerate the deterioration of transformer components. These environmental factors can degrade insulation, corrode conductors, and contribute to transformer failure.
8.Poor maintenance:
Inadequate or insufficient maintenance practices, such as neglecting routine inspections, failing to perform necessary repairs or replacements, or disregarding recommended maintenance guidelines, can increase the risk of transformer failure. Lack of maintenance can lead to undetected faults, insulation degradation, and overall deterioration of transformer performance over time.
What are the common failure modes of high frequency transformers and their respective solutions?
Common failure modes of high frequency transformers can vary depending on several factors, including the design, operating conditions, and maintenance practices. Here are 8 common failure modes and their respective solutions:
1.Overheating:
Solution: Ensure proper cooling and ventilation systems for the transformer. Monitor and control the operating temperature within acceptable limits. Consider using additional cooling methods such as fans, heat sinks, or liquid cooling systems if necessary. Verify that the transformer is not overloaded and that the load is within its rated capacity.
2.Insulation breakdown:
Solution: Regularly inspect and test the insulation system of the transformer. Perform dielectric tests to detect any insulation weaknesses or breakdown. Replace or repair damaged insulation materials. Consider using advanced insulation materials with improved thermal and electrical properties. Ensure proper installation techniques to prevent insulation damage during assembly.
3.Overloading:
Solution: Ensure that the transformer is not operated beyond its rated capacity. Perform load calculations and monitoring to ensure that the transformer is adequately sized for the application. Consider upgrading to a higher-rated transformer if the load requirements exceed the current transformer’s capacity.
4.Voltage surges:
Solution: Implement surge protection devices such as surge arresters or transient voltage suppressors to protect the transformer from sudden voltage surges. Install proper grounding systems to dissipate excess electrical energy. Consider using isolation transformers or voltage regulators to stabilize voltage levels.
5.Electrical faults:
Solution: Conduct regular inspections and electrical tests to identify and rectify any internal electrical faults. Perform insulation resistance tests, short-circuit tests, and partial discharge tests to detect potential faults. Repair or replace damaged components or windings as necessary.
6.Mechanical damage:
Solution: Handle the transformer with care during transportation, installation, and maintenance. Avoid excessive vibrations, impacts, or mechanical stresses that can damage the transformer. Provide proper support and protection for the transformer to prevent physical damage. Repair or replace damaged components promptly.
7.Environmental factors:
Solution: Protect the transformer from harsh environmental conditions such as extreme temperatures, humidity, or corrosive atmospheres. Consider using protective enclosures or environmental control systems. Perform regular inspections to identify and address any corrosion, moisture ingress, or environmental damage.
8.Poor maintenance:
Solution: Implement a comprehensive and proactive maintenance program for the transformer. Follow manufacturer’s guidelines and industry standards for inspections, cleaning, and maintenance tasks. Conduct regular tests, such as insulation resistance tests and winding resistance measurements. Address any maintenance issues promptly to prevent further deterioration.

How can I detect early signs of transformer failure?
Detecting early signs of transformer failure is crucial for timely intervention and preventing major issues. Here are 10 common methods to detect early signs of transformer failure:
- Visual Inspection: Regular visual inspections can reveal visible signs of damage, such as oil leaks, discoloration, corrosion, loose connections, or physical deformities. Look for any abnormal conditions that may indicate potential problems.
- Temperature Monitoring: Monitor the operating temperature of the transformer using temperature sensors or thermal imaging cameras. Elevated temperatures can be a sign of overloading, inadequate cooling, or internal faults.
- Dissolved Gas Analysis (DGA): Analyze the concentration of gases dissolved in the transformer oil. Abnormal gas levels, such as increased levels of hydrogen, methane, ethylene, or carbon monoxide, can indicate insulation degradation, arcing, or overheating.
- Power Quality Monitoring: Monitor the power quality parameters, such as voltage, current, harmonics, and transient events. Unusual voltage fluctuations, harmonic distortion, or sudden spikes can be indicative of electrical faults or system issues affecting the transformer.
- Insulation Resistance Testing: Conduct regular insulation resistance tests to measure the insulation condition of the transformer. Decreasing insulation resistance values may suggest insulation deterioration or moisture ingress.
- Winding Resistance Testing: Measure the winding resistance of the transformer to detect any changes in resistance values. An increase in resistance may indicate loose connections or winding damage.
- Partial Discharge (PD) Monitoring: Monitor and measure partial discharge activities within the transformer. PDs are localized electrical discharges that can occur due to insulation degradation or breakdown. Continuous monitoring can help identify insulation weaknesses early on.
- Oil Analysis: Perform routine oil sampling and analysis to assess the condition of the transformer oil. Oil analysis can detect the presence of contaminants, moisture, oxidation, or degradation byproducts, which can provide insights into the overall health of the transformer.
- Vibration Analysis: Monitor the vibrations of the transformer using vibration sensors. Unusual vibration patterns can indicate mechanical issues, loose components, or structural problems within the transformer.
- Noise Analysis: Listen for abnormal noises or buzzing sounds during transformer operation. Unusual noises can indicate loose windings, loose core laminations, or mechanical issues.
How do temperature monitoring techniques help in identifying potential failures?
Temperature monitoring techniques can play a crucial role in identifying potential failures in various systems and processes. By monitoring temperature changes, deviations, and patterns, these techniques provide valuable insights into the health and performance of equipment, machinery, and even biological systems. Here are 6 ways temperature monitoring can help in identifying potential failures:
- Early Warning Signs: Temperature monitoring can detect abnormal temperature variations that might indicate an impending failure or malfunction. By establishing baseline temperature ranges for different components or systems, any significant deviations can be identified as early warning signs of potential problems.
- Overheating Detection: Many devices and systems have temperature limits beyond which they can malfunction or even fail catastrophically. By continuously monitoring temperatures, potential overheating issues can be identified before they cause significant damage. This is especially critical in high-power electrical systems, engines, or industrial processes where overheating can lead to fires, equipment damage, or safety hazards.
- Thermal Stress Analysis: Temperature monitoring helps assess thermal stress levels on components and materials. Excessive temperature fluctuations, rapid heating or cooling, or temperature differentials can lead to thermal fatigue, material degradation, or even structural failures. By analyzing temperature data, engineers can identify areas prone to thermal stress and take preventive measures to avoid failures.
- Predictive Maintenance: By monitoring the temperature of various components or systems, predictive maintenance programs can be established. Temperature data, combined with other sensor readings or performance indicators, can help predict the remaining useful life of equipment, detect abnormal wear and tear, or identify potential failure modes. This proactive approach allows for planned maintenance or repairs, reducing downtime and optimizing operational efficiency.
- Process Optimization: In industrial processes, temperature monitoring plays a vital role in optimizing efficiency and identifying potential bottlenecks or inefficiencies. By analyzing temperature profiles, engineers can determine optimal temperature ranges for various stages of a process, identify areas with suboptimal heat transfer, or detect abnormal temperature gradients that could indicate issues with equipment or process design.
- Environmental Monitoring: Temperature monitoring is also essential in environmental monitoring and control systems. For example, in server rooms or data centers, monitoring the temperature helps prevent overheating of critical IT infrastructure and ensures the proper functioning of servers and networking equipment. Similarly, in laboratories or medical facilities, temperature monitoring is vital for preserving the integrity of sensitive samples, medications, or biological materials.
Can transformer failure be prevented by upgrading cooling systems?
Upgrading cooling systems can help mitigate the risk of transformer failure and increase the overall reliability of transformers. Transformers generate heat during operation due to losses in the core and windings. If the heat is not adequately dissipated, it can lead to excessive temperature rise, accelerated aging, insulation degradation, and ultimately transformer failure. Upgrading cooling systems can address these issues by improving heat dissipation and maintaining optimal operating temperatures. Here’s how upgrading cooling systems can help prevent transformer failure:
- Enhanced Heat Dissipation: Upgrading cooling systems can involve the installation of more efficient cooling mechanisms such as fans, pumps, or heat exchangers. These systems help increase the rate of heat transfer from the transformer, improving heat dissipation and reducing the operating temperature. By maintaining lower temperatures, the aging process of insulation materials is slowed down, prolonging the transformer’s lifespan and reducing the risk of failures.
- Increased Cooling Capacity: Transformers are typically designed with a specific cooling class, such as ONAN (Natural Air), ONAF (Forced Air), or OFAF (Forced Oil-Air). Upgrading the cooling system can involve increasing the cooling capacity, such as adding additional cooling fins, increasing the airflow, or using more efficient cooling fluids. This allows the transformer to handle higher heat loads and reduces the chances of overheating and failure, particularly during periods of increased demand or higher ambient temperatures.
- Temperature Monitoring and Control: Upgraded cooling systems often include advanced temperature monitoring and control mechanisms. These systems provide real-time temperature data from different parts of the transformer, enabling operators to closely monitor and control the operating temperatures. Alarms or automated shutdown mechanisms can be implemented to prevent the transformer from operating beyond safe temperature limits, thereby averting potential failures.
- Cooling System Redundancy: Upgraded cooling systems may include redundancy features such as multiple fans, pumps, or cooling circuits. Redundancy ensures that if one component or circuit fails, there is a backup system in place to maintain cooling functionality. This redundancy reduces the risk of cooling system failures, which can otherwise lead to rapid temperature rise and transformer damage.
- Improved Maintenance Practices: Upgraded cooling systems can facilitate improved maintenance practices for transformers. For example, the installation of oil cooling systems with efficient filtration and oil circulation can help remove contaminants and extend the life of the insulating oil. Regular maintenance tasks such as cleaning cooling fins, inspecting fans, or checking coolant levels become more accessible with upgraded systems, ensuring the cooling system remains in optimal working condition.
While upgrading cooling systems can significantly reduce the risk of transformer failure, it is important to consider other factors as well. Transformers are complex systems, and failures can also result from issues like insulation breakdown, overloading, or electrical faults. Therefore, a holistic approach that includes regular inspections, maintenance, and monitoring of various transformer parameters, in addition to upgrading cooling systems, is necessary to prevent failures effectively.
How can insulation enhancements help in addressing transformer failures?
Insulation enhancements can play a crucial role in addressing transformer failures by improving the insulation system’s performance and increasing the transformer’s reliability. The insulation system in transformers serves to electrically insulate the various windings, core, and other components while also providing mechanical support. By upgrading and enhancing the insulation, several benefits can be achieved, mitigating the risk of failures. Here are some ways insulation enhancements can help:
- Increased Dielectric Strength: Upgrading insulation materials can improve the dielectric strength, which is the ability of the insulation to withstand high voltages without breakdown. Higher dielectric strength reduces the risk of insulation failure due to electrical stress or transient voltage spikes. This is particularly important in transformers that operate at higher voltage levels.
- Improved Thermal Conductivity: Enhancing the thermal conductivity of the insulation system helps in dissipating heat more efficiently. Heat generated during transformer operation can cause localized hotspots, accelerating insulation degradation. By using insulation materials with better thermal conductivity, the heat is spread more evenly, reducing the risk of hotspots and preventing insulation breakdown.
- Enhanced Mechanical Strength: Transformer insulation needs to withstand mechanical stresses caused by electrical and thermal variations, as well as transportation and operational vibrations. Upgrading insulation materials can provide improved mechanical strength, reducing the risk of insulation failure due to mechanical stress or vibrations. This is especially important in large power transformers or transformers subjected to severe operational conditions.
- Reduced Moisture Absorption: Moisture can be detrimental to transformer insulation as it can lead to reduced dielectric strength and accelerated aging. Upgraded insulation materials can have lower moisture absorption properties, minimizing the risk of insulation failures caused by moisture ingress. Additionally, improved moisture resistance can help mitigate the effects of humidity, moisture condensation, or environmental exposure.
- Enhanced Thermal Stability: Insulation enhancements can include using materials with higher thermal stability, which can withstand elevated temperatures for longer durations without significant degradation. This is particularly important in transformers that operate at high loads or during transient conditions. Improved thermal stability of the insulation system reduces the risk of insulation breakdown, insulation aging, and the associated failures.
- Compatibility with Environmental Requirements: Upgrading insulation materials can ensure compliance with environmental regulations and requirements. For example, the use of insulation materials with low or no halogen content can help address concerns related to fire safety and environmental impact. Such enhancements reduce the risk of transformer failures caused by fire or toxic gas emissions during operation.
It’s worth noting that insulation enhancements should be considered in conjunction with other preventive measures and maintenance practices. Regular inspections, diagnostic tests, and appropriate maintenance procedures are essential for identifying potential insulation weaknesses or degradation. Implementing insulation enhancements should be done in accordance with industry standards and best practices to ensure compatibility and optimal performance with the specific transformer design and operating conditions.
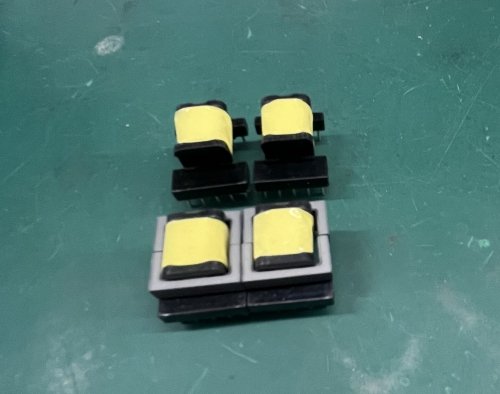
What measures can be taken to prevent overloading and overvoltage issues?
Preventing overloading and overvoltage issues in electrical systems is crucial to ensure the safe and reliable operation of equipment and to avoid potential failures or damage. Here are some measures that can be taken to prevent overloading and overvoltage issues:
1.Load Analysis and Planning:
Conduct a thorough load analysis to determine the electrical demands and requirements of the system. This includes considering the anticipated load levels, peak demands, and future growth projections. By properly planning the electrical system, including sizing transformers, conductors, and protective devices, the risk of overloading can be minimized.
2.Load Management and Balancing:
Implement load management strategies to distribute and balance the electrical load across different phases or circuits. This helps prevent overloading on specific lines or components. Techniques such as load shedding, load leveling, or demand response programs can be employed to manage peak demands and avoid excessive load on the system.
3.Proper Equipment Sizing and Selection:
Ensure that electrical equipment, such as transformers, circuit breakers, and conductors, are correctly sized and selected to handle the anticipated load and voltage levels. Equipment should have sufficient capacity and be rated appropriately for the expected electrical demands. Oversized equipment can lead to inefficient operation, while undersized equipment can be prone to overloading and failures.
4.Voltage Regulation:
Maintain proper voltage regulation within the electrical system. Overvoltage conditions can occur due to external factors, such as utility voltage fluctuations, or internal factors, such as reactive power imbalances. Employ voltage regulation techniques, such as automatic voltage regulators (AVRs), tap changers, or power factor correction devices, to maintain voltage levels within acceptable limits and prevent overvoltage issues.
5.Protective Devices and Relays:
Install protective devices, such as circuit breakers, fuses, or relays, throughout the electrical system. These devices are designed to detect and interrupt excessive currents or voltage surges that can lead to overloading or overvoltage conditions. Proper coordination and setting of protective devices ensure timely and selective operation to isolate faulty circuits and protect the system.
6.Monitoring and Control Systems:
Implement monitoring and control systems that provide real-time information on load levels, voltage levels, and system performance. Advanced metering systems, supervisory control and data acquisition (SCADA), or building management systems (BMS) can provide valuable insights into the electrical system’s status and help identify potential overloading or overvoltage issues. Alarms, alerts, and automated control mechanisms can be implemented to take corrective actions or initiate protective measures when abnormal conditions are detected.
7.Regular Maintenance and Inspections:
Conduct regular maintenance and inspections of electrical equipment and systems. This includes checking for loose connections, damaged insulation, or worn-out components that can contribute to overloading or overvoltage problems. Regular preventive maintenance ensures the system is in optimal condition, reduces the risk of failures, and helps identify potential issues before they escalate.
8.Employee Training and Awareness:
Educate personnel about overloading and overvoltage risks and train them on proper load management practices, equipment operation, and safety procedures. Promote awareness of energy efficiency practices and the importance of load monitoring to prevent overloading. Well-informed and trained staff can contribute to maintaining the integrity and reliability of the electrical system.
Is it possible to upgrade the core of a high frequency transformer to avoid failure?
Upgrading the core of a high-frequency transformer can be a viable approach to improve its performance and reliability, and potentially mitigate the risk of failure. The core plays a critical role in the transformer’s operation, as it provides a magnetic path for the transfer of energy between the primary and secondary windings. Upgrading the core can involve various enhancements aimed at addressing specific issues or improving overall performance. Here are five possibilities:
- Core Material Selection: The choice of core material is crucial in high-frequency transformers. Upgrading the core can involve selecting materials with improved magnetic properties, such as high-permeability alloys or ferrite cores designed for high-frequency operation. These materials can minimize core losses, improve energy transfer efficiency, and reduce the risk of overheating or saturation.
- Core Design Optimization: Upgrading the core design can involve optimizing its shape, dimensions, and winding configurations to reduce core losses and improve magnetic flux distribution. This can be achieved through advanced modeling and simulation techniques that help identify potential issues and find optimal core designs for specific frequency ranges and power levels.
- Core Cooling Enhancement: In high-frequency transformers, the core can generate significant heat due to eddy currents and hysteresis losses. Upgrading the cooling system around the core can help dissipate this heat effectively. This can include using improved cooling techniques such as forced air cooling, liquid cooling, or incorporating cooling channels within the core structure itself. Adequate cooling helps maintain the core temperature within safe limits, reducing the risk of thermal failures.
- Core Insulation and Protection: Upgrading the core insulation can enhance the electrical insulation between the core and windings, reducing the risk of insulation breakdown and corona discharge. This can be achieved through the use of insulating materials with improved dielectric strength and resistance to high frequencies. Additionally, protecting the core against environmental factors such as moisture, dust, or contaminants can help prevent core degradation and improve long-term reliability.
- Core Shielding and EMI Reduction: High-frequency transformers can be susceptible to electromagnetic interference (EMI). Upgrading the core can involve incorporating additional shielding techniques, such as magnetic shielding or electromagnetic interference filters, to minimize the impact of external electromagnetic fields on the transformer’s performance. Effective EMI reduction measures can help avoid issues related to noise, signal degradation, or interference-induced failures.
How can electromagnetic interference be mitigated to prevent transformer failure?
Mitigating electromagnetic interference (EMI) is crucial to prevent transformer failure and ensure the reliable operation of electrical systems. EMI can introduce noise, voltage spikes, and other disturbances that can negatively impact transformers and associated equipment. Here are several measures that can be taken to mitigate EMI and prevent transformer failure:
- Shielding: Implement electromagnetic shielding to minimize the effects of external electromagnetic fields on the transformer. This can involve using conductive enclosures, metallic shields, or shielding materials to create a barrier that blocks or redirects electromagnetic radiation. Proper shielding helps reduce the coupling of external EMI sources with the transformer, minimizing the risk of interference-induced failures.
- Grounding and Bonding: Establish proper grounding and bonding practices to mitigate EMI. Ensuring solid and low-impedance grounding connections helps redirect unwanted electrical currents and provides a safe discharge path for EMI. Bonding conductive components and enclosures together helps maintain consistent electrical potential and reduces the risk of EMI coupling.
- Filtering: Install electromagnetic interference filters or suppressors to attenuate unwanted high-frequency noise and voltage spikes. These filters can be placed at various points within the electrical system, including input power lines, communication lines, and control circuits. Properly designed filters help block or divert EMI, protecting the transformer and sensitive equipment from the harmful effects of interference.
- Cable Routing and Separation: Carefully plan and route cables to minimize the proximity of high-frequency and low-voltage signal cables with high-power or high-frequency sources. Separating or physically routing cables in a manner that reduces cross-coupling and electromagnetic induction helps minimize EMI propagation and interference.
- Proper Equipment Installation: Follow best practices for equipment installation to minimize EMI risks. This includes ensuring adequate spacing between sensitive equipment and high-power or high-frequency sources. Proper shielding, grounding, and routing of cables during installation help maintain electromagnetic compatibility and prevent EMI-related failures.
- .Surge Protection: Implement surge protection devices to prevent voltage spikes and transients from reaching the transformer. Surge protectors or surge suppression circuits can be installed at critical points within the system to divert excessive energy away from the transformer. This helps prevent insulation breakdown, reduces the risk of overvoltage failures, and enhances the transformer’s lifespan.
- Compliance with EMI Standards: Adhere to relevant electromagnetic compatibility (EMC) standards and regulations. These standards define limits for electromagnetic emissions and susceptibility, as well as provide guidelines for EMI mitigation strategies. Complying with these standards ensures that the transformer and associated equipment meet acceptable levels of electromagnetic compatibility and are less susceptible to EMI-related failures.
In conclusion, dealing with high frequency transformer failure requires a proactive and vigilant approach. By emphasizing the importance of regular maintenance, prompt action, and optimizing performance, you can minimize the risk of failures, enhance system reliability, and ensure the uninterrupted operation of high frequency power systems. By implementing the strategies discussed in this blog, you are on your way to effectively managing transformer failures and maximizing the efficiency and lifespan of your high frequency transformers.