Why is it important to choose the right copper wire diameter for a high frequency transformer?
Choosing the right copper wire diameter for a high-frequency transformer is crucial for five reasons:
- Electrical Efficiency: Copper wire is commonly used in transformers due to its high electrical conductivity. The wire diameter directly affects the electrical resistance of the wire. When operating at high frequencies, the resistance of the wire becomes more significant. By selecting an appropriate wire diameter, you can minimize resistance and maximize electrical efficiency. Lower resistance leads to reduced power losses in the form of heat, resulting in more efficient energy transfer.
- Skin Effect: At high frequencies, the skin effect becomes prominent. The skin effect refers to the tendency of alternating current (AC) to concentrate near the surface of a conductor, rather than being evenly distributed throughout its cross-section. This phenomenon causes increased resistance in the wire, reducing the effective conductor diameter. Choosing an appropriate wire diameter helps mitigate the skin effect, ensuring optimal current distribution and minimizing energy losses.
- Space Constraints: High-frequency transformers often have specific size limitations due to space constraints in their intended applications. Selecting the right wire diameter allows you to balance the necessary current-carrying capacity with space limitations. Smaller wire diameters can save space, but they must still be capable of carrying the required current without excessive resistance and losses.
- Mechanical Strength: The wire diameter also influences the mechanical strength of the transformer winding. A thicker wire can provide better structural integrity and resistance to breakage during manufacturing, transportation, and operation. This is particularly important for high-frequency transformers that may experience vibrations, thermal expansion/contraction, and other mechanical stresses.
- Thermal Considerations: The wire diameter affects the heat dissipation capabilities of the transformer. High-frequency transformers can generate significant heat during operation, and an appropriately chosen wire diameter helps ensure efficient heat transfer away from the windings. This prevents excessive temperature rise, which can degrade insulation, affect electrical performance, and reduce the lifespan of the transformer.
What factors should be considered when choosing the copper wire diameter for a high frequency transformer?
When choosing the copper wire diameter for a high-frequency transformer, seven factors should be considered:
- Operating Frequency: The operating frequency of the transformer is a critical factor in determining the appropriate wire diameter. As the frequency increases, the skin effect becomes more significant, leading to increased resistance. To minimize losses, the wire diameter should be selected to account for the skin effect at the specific operating frequency.
- Current Carrying Capacity: The wire diameter should be chosen to handle the maximum expected current without excessive resistance. A thicker wire can carry more current, reducing resistive losses. It is essential to consider the expected load conditions and select a wire diameter that can handle the current requirements without exceeding its ampacity limits.
- Power Losses: The choice of wire diameter impacts power losses in the transformer. Thicker wires generally have lower resistance, resulting in reduced copper losses. However, thicker wires may also increase proximity effect losses due to increased inter-wire capacitance. It is crucial to strike a balance between copper losses and proximity effect losses to achieve optimal efficiency.
- Space Constraints: The available space within the transformer’s design must be considered. Larger wire diameters occupy more space, which can be a limitation in compact or miniaturized transformer designs. Balancing the required current-carrying capacity with space constraints is important when selecting the wire diameter.
- Manufacturing Considerations: The wire diameter should align with the manufacturing capabilities and processes. Thicker wires may require special winding techniques, larger winding formers, or different insulation methods. Considering the manufacturing constraints and capabilities ensures the chosen wire diameter can be effectively implemented during production.
- Mechanical Strength: The wire diameter influences the mechanical strength and robustness of the transformer winding. Thicker wires offer better structural integrity and resistance to breakage or damage during handling, installation, and operation. This factor is particularly important in applications where the transformer may be subjected to vibrations, mechanical stresses, or thermal expansion/contraction.
- Thermal Considerations: The wire diameter affects the heat dissipation capabilities of the transformer winding. Thicker wires typically have better heat transfer properties, allowing for efficient dissipation of heat generated during operation. It is crucial to choose a wire diameter that can handle the expected heat load and prevent excessive temperature rise, which can degrade insulation and affect the transformer’s performance and reliability.
How does the frequency of the transformer affect the choice of copper wire diameter?
The frequency of the transformer influences the choice of copper wire diameter due to the skin effect, proximity effect, magnetic field penetration, core losses, and mechanical considerations. By selecting an appropriate wire diameter, these effects can be managed, resulting in improved electrical performance, reduced losses, and enhanced overall efficiency of the high-frequency transformer.
The frequency of the transformer significantly influences the choice of copper wire diameter. Here’s how the frequency impacts the selection process:
- Skin Effect: The skin effect refers to the tendency of alternating current (AC) to concentrate near the surface of a conductor at higher frequencies. This phenomenon causes the effective conductor diameter to reduce, resulting in increased resistance. To mitigate the skin effect and minimize resistance, a larger wire diameter is typically chosen for high-frequency transformers. The larger diameter ensures that an adequate cross-sectional area of the conductor is available to carry the current without significant resistance-induced losses.
- Proximity Effect: At high frequencies, the proximity effect becomes more pronounced. The proximity effect occurs due to the interaction between adjacent conductors carrying AC currents. It leads to an uneven distribution of current within each conductor, resulting in increased resistance and losses. To mitigate the proximity effect, larger wire diameters are preferred. The increased diameter helps reduce the current density within each conductor, minimizing the effects of proximity-induced losses.
- Magnetic Field Penetration: The frequency of the transformer affects the penetration depth of the magnetic field within the conductor. At higher frequencies, the magnetic field tends to penetrate less into the conductor. This phenomenon influences the effective utilization of the conductor material for carrying the magnetic flux and can affect the overall performance of the transformer. Therefore, an appropriate wire diameter should be chosen to ensure sufficient conductor material is available for effective magnetic flux linkage.
- Skin Effect and Core Losses: In addition to the skin effect on the conductor, higher frequencies can also impact core losses in the transformer’s magnetic core. The core losses are affected by the eddy currents induced in the core material. To minimize core losses, the wire diameter and winding arrangement should be chosen to balance the effects of the skin effect and core losses at the given operating frequency.
- Mechanical Considerations: The frequency of operation can impact the mechanical stresses on the wire due to rapid changes in current direction. Thicker wire diameters offer better mechanical strength and can withstand the mechanical stresses associated with high-frequency operation more effectively. Thus, the wire diameter should be chosen to ensure mechanical robustness and durability under the anticipated operating conditions.
Can a smaller diameter copper wire be used for a high frequency transformer to save costs?
Using a smaller diameter copper wire for a high-frequency transformer may be a consideration to save costs, but it must be done with caution. Here are some factors to consider:
- Current Carrying Capacity: Smaller wire diameters have lower current-carrying capacities compared to larger diameters. When selecting a smaller diameter wire, it is crucial to ensure that it can handle the maximum expected current without exceeding its ampacity limits. Failure to do so may result in excessive resistance, heat generation, and potential damage to the wire or transformer.
- Power Losses: Smaller wire diameters generally have higher resistance, which leads to increased power losses in the form of heat. This can reduce the overall efficiency of the transformer. It is essential to balance the cost-saving considerations with the increased losses and potential impact on the transformer’s performance.
- Voltage Drop: The resistance of the wire contributes to voltage drop along the length of the wire. Using a smaller wire diameter increases resistance, which can result in a more significant voltage drop. If precise voltage regulation is critical for the transformer’s application, a smaller wire diameter may not be suitable as it can negatively affect the voltage output.
- Thermal Considerations: Smaller wire diameters may have limited heat dissipation capabilities compared to larger diameters. This can lead to higher temperatures in the transformer winding, potentially causing insulation degradation or other thermal issues. Adequate heat dissipation measures, such as proper cooling or insulation systems, must be implemented when using smaller wire diameters to manage the heat generated during operation.
- Mechanical Strength: Smaller wire diameters are generally more fragile and have lower mechanical strength compared to larger wires. This can make them more susceptible to breakage or damage during handling, installation, or operation. If the transformer is subjected to mechanical stresses or vibrations, using a smaller wire diameter may increase the risk of wire failure.
While cost-saving considerations are important, compromising too much on the wire diameter can lead to detrimental effects on the transformer’s electrical performance, reliability, and longevity. It is crucial to carefully evaluate the specific requirements of the transformer, such as current-carrying capacity, power losses, voltage drop, thermal considerations, and mechanical strength, before deciding on a smaller wire diameter. It is recommended to consult with experienced professionals or engineers to ensure the appropriate wire diameter is chosen for the high-frequency transformer while balancing cost-saving objectives.
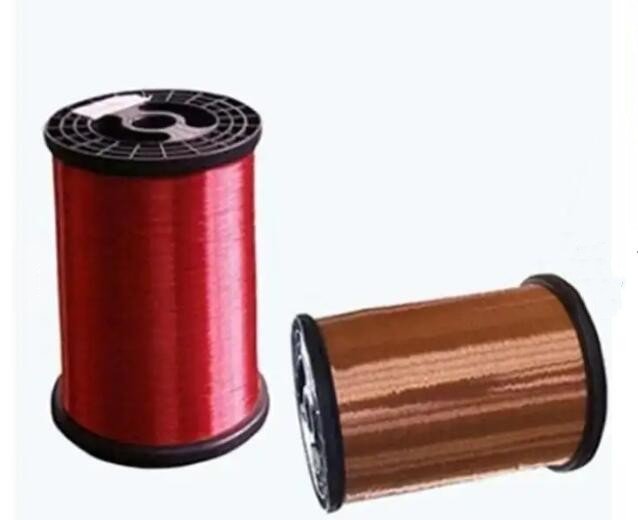
How do I calculate the appropriate copper wire diameter for a high frequency transformer?
Calculating the appropriate copper wire diameter for a high-frequency transformer involves considering several factors. Here’s a general approach to help you calculate the wire diameter:
1.Determine the Current Requirements:
Start by determining the maximum expected current that the wire needs to carry in the transformer. This depends on the load connected to the transformer and the desired output.
2.Ampacity Calculation:
Check the ampacity rating of copper wire based on the desired operating temperature and the insulation type. The ampacity is the maximum current a wire can carry without exceeding its temperature limits. Calculate the required wire diameter using the ampacity equation:
Wire Diameter (mm) = √(I / (K * A)
Where:
I = Maximum current in amperes
K = Ampacity constant based on the insulation type (consult manufacturer’s specifications)
A = Cross-sectional area of the wire (mm²)
3.Skin Effect Consideration:
If the transformer operates at a high frequency, account for the skin effect. The skin effect increases resistance and reduces the effective conductor diameter. Adjust the wire diameter calculated in step 2 to compensate for the skin effect. This adjustment may involve multiplying the wire diameter by a correction factor based on the operating frequency and the desired skin depth.
4.Mechanical Strength and Space Constraints:
Consider the mechanical strength requirements of the wire based on factors such as vibrations, thermal expansion/contraction, and space limitations within the transformer. Choose a wire diameter that provides the necessary mechanical strength while fitting within the available space.
It’s important to note that calculating the wire diameter involves trade-offs between electrical performance, thermal considerations, mechanical strength, and space limitations. Consult with experienced professionals or electrical engineers who have expertise in high-frequency transformer design to ensure the accurate calculation and selection of the appropriate wire diameter for your specific transformer application.
What are the tips for selecting the correct copper wire diameter for high-frequency transformer?
Selecting the correct copper wire diameter for a high-frequency transformer is an important consideration to ensure optimal performance. Here are 8 tips to help you with this process:
- Determine the operating frequency: The first step is to identify the operating frequency of your transformer. High-frequency transformers typically operate in the range of several kilohertz (kHz) to megahertz (MHz).
- Consider skin effect: At high frequencies, the skin effect becomes significant, causing current to concentrate near the surface of the wire. This reduces the effective cross-sectional area available for conducting current and increases resistance. Take the skin effect into account when selecting wire diameter by referring to skin depth calculations.
- Calculate maximum current: Determine the maximum current that will flow through the wire based on your transformer’s design specifications. This will help you determine the minimum wire diameter required to handle the current without excessive resistance or overheating.
- Consider thermal constraints: Copper wire has a maximum current-carrying capacity based on its thermal characteristics. Ensure that the selected wire diameter can handle the anticipated current without exceeding the temperature limits of the wire insulation or causing significant power losses due to resistive heating.
- Check wire gauge standards: Consult industry standards and wire gauge charts to identify the appropriate wire diameter options for your desired current capacity. Commonly used standards include the American Wire Gauge (AWG) and International Electrotechnical Commission (IEC) standards.
- Consider space constraints: If your transformer has limited space for winding, you may need to select a smaller wire diameter to accommodate the required number of turns within the available winding area. However, be cautious about selecting wire diameters that are too small, as they can increase resistance and reduce efficiency.
- Consider cost: Thicker copper wire has a lower resistance but can be more expensive. Balance the cost of copper wire with the desired performance and the constraints of your transformer design.
- Seek expert advice if needed: If you are unsure about the appropriate wire diameter for your specific high-frequency transformer design, consult with experienced electrical engineers or transformer manufacturers who can provide guidance based on their expertise.
Remember that selecting the correct copper wire diameter involves a trade-off between various factors, including current capacity, skin effect, thermal constraints, space limitations, and cost. Carefully evaluate these factors to determine the optimal wire diameter for your high-frequency transformer.
What are the consequences of using a copper wire with the wrong diameter for a high frequency transformer?
Using a copper wire with the wrong diameter for a high-frequency transformer can have several consequences, impacting the performance and reliability of the transformer. Here are 7 potential consequences:
- Increased resistance: If the wire diameter is too small for the desired current capacity, it can result in increased resistance. Higher resistance leads to greater power losses in the form of heat, reducing the transformer’s overall efficiency. Additionally, increased resistance can cause voltage drops and affect the regulation of the transformer.
- Excessive heat generation: Inadequate wire diameter may not be able to handle the current flowing through the transformer effectively. This can lead to excessive heat generation due to the higher current density, potentially causing overheating of the wire and other transformer components. Excessive heat can degrade insulation, reduce lifespan, and even result in insulation breakdown or insulation-to-insulation shorts.
- Reduced power handling capacity: Using a wire with an insufficient diameter may limit the transformer’s power handling capacity. The wire may not be able to carry the required current without excessive voltage drops or overheating. This can result in reduced output power capability and limitations in the transformer’s overall performance.
- Increased skin effect: High-frequency transformers operate at frequencies where the skin effect becomes significant. If the wire diameter is not selected appropriately, the skin effect can worsen. The current tends to concentrate near the wire’s surface, reducing the effective cross-sectional area available for conducting current and increasing resistance. This effect can further exacerbate power losses, reduce efficiency, and adversely impact the transformer’s performance.
- Voltage breakdown or insulation failure: If the wire diameter is too small, leading to excessive current density and heat generation, it can pose a risk to the insulation system of the transformer. The increased heat can weaken or degrade the insulation materials, potentially resulting in insulation breakdown, short circuits, or even catastrophic failure of the transformer.
- Increased electromagnetic interference (EMI): Inadequate wire diameter can contribute to higher EMI emissions and susceptibility. Improper wire sizing can lead to increased resistance, voltage drops, and unwanted impedance variations, causing electromagnetic noise and interference that can affect the performance of nearby electronic devices or circuits.
- Reduced overall efficiency: The combination of increased resistance, heat generation, and power losses due to the wrong wire diameter can significantly reduce the overall efficiency of the high-frequency transformer. Efficiency is a crucial factor in transformer design, affecting power consumption, heat dissipation, and overall system performance.
To ensure optimal performance and reliability, it is important to select the correct wire diameter for high-frequency transformers based on the design specifications, current requirements, thermal constraints, and other relevant factors. Consulting with experienced electrical engineers or transformer manufacturers can help in making the appropriate wire diameter selection for your specific application.
Is it necessary to use enameled wire for a high frequency transformer, or can regular copper wire be used?
For high-frequency transformers, it is generally necessary to use enameled wire rather than regular copper wire. Here’s why:
- Insulation: High-frequency transformers operate at frequencies where the proximity effect and skin effect are significant. Enameled wire has a thin layer of insulation (typically made of enamel) that provides electrical isolation between the wire turns and prevents short circuits. The insulation also helps reduce the effects of the skin effect by confining the current flow to the wire’s surface.
- Reduced losses: Enameled wire is designed to have low dielectric losses, which is essential for minimizing power losses in high-frequency applications. The thin insulation layer and carefully selected materials used in enameled wire reduce the dielectric losses and improve the efficiency of the transformer.
- Thermal management: Enameled wire offers better thermal management compared to regular copper wire. The thin insulation layer acts as a thermal barrier, helping to dissipate heat and prevent excessive temperature rise in the wire. This is crucial for maintaining the reliability and longevity of the transformer.
- Space utilization: Enameled wire allows for compact winding configurations due to its thin insulation layer. The reduced insulation thickness enables more turns to be accommodated within a given winding space, allowing for higher inductance or increased power density in the transformer.
Regular copper wire without proper insulation, on the other hand, does not provide the necessary electrical isolation and thermal management required for high-frequency transformer applications. It can lead to short circuits, increased power losses, overheating, and reduced overall performance and reliability.
It is recommended to use enameled wire specifically designed for high-frequency applications to ensure proper insulation, reduced losses, improved thermal management, and efficient performance of the transformer at high frequencies.
Can different types of copper wire be used for a high frequency transformer?
Yes, different types of copper wire can be used for high-frequency transformers. The choice of copper wire type depends on specific design requirements and the operating conditions of the transformer. Here are four common types of copper wire that are suitable for high-frequency transformer applications:
- Enameled Copper Wire: Enameled wire, also known as magnet wire, is a widely used type of copper wire for high-frequency transformers. It is coated with a thin layer of insulation, typically made of enamel, which provides electrical isolation between wire turns. Enameled wire helps mitigate the skin effect and reduce power losses in high-frequency applications.
- Litz Wire: Litz wire is a specialized type of copper wire designed to address the skin effect and minimize power losses at high frequencies. It consists of multiple strands of individually insulated copper wires twisted together. The twisting arrangement helps distribute the current across the individual strands, reducing the skin effect and minimizing resistance.
- Rectangular Wire: In some high-frequency transformers, rectangular wire is used instead of round wire. Rectangular wire offers advantages in terms of maximizing space utilization and reducing proximity effects. The flat shape of rectangular wire allows for tighter winding configurations and higher packing density.
- Stranded Wire: Stranded wire consists of multiple small-gauge copper wires bundled together. It offers increased flexibility and can handle higher currents compared to single solid-core wire. Stranded wire can be advantageous for high-frequency transformers that require flexibility for winding or have stringent current-carrying capacity requirements.
Selecting the correct copper wire diameter is crucial for high-frequency transformers to ensure optimal performance and reliability. Key points to consider include understanding the operating frequency, calculating maximum current, considering thermal constraints, consulting wire gauge standards, and accounting for space and cost limitations.
Using the wrong wire diameter can result in increased resistance, heat generation, power limitations, skin effect issues, insulation failure, EMI problems, and reduced efficiency. Therefore, making an informed decision based on these factors is essential.
By choosing the right wire diameter, high-frequency transformers can achieve efficient power transfer, minimize losses, manage heat effectively, and perform reliably. Seeking advice from experts can provide valuable insights for optimal design.