As an electronic component manufacturer, I understand the importance of having reliable and high-quality transformers in your designs. Encapsulated PCB transformers, in particular, offer a compact and robust solution for a wide range of applications, from power supplies to signal conditioning circuits. However, off-the-shelf options may not always meet your specific requirements, which is where custom encapsulated PCB transformers come into play.
Custom encapsulated PCB transformers are designed and manufactured to meet your unique specifications, ensuring optimal performance and seamless integration into your electronic systems. By following a systematic approach, you can navigate the process of purchasing custom encapsulated PCB transformers with confidence, ensuring you receive a product that meets your exact needs.
As an electronics manufacturer, I understand the frustration of trying to find the perfect off-the-shelf transformer that meets all your design requirements. You’ve likely spent countless hours scouring datasheets, only to realize that no standard option can provide the exact specifications you need. Whether it’s the right input voltage range, operating temperature, or safety certifications, those one-size-fits-all transformers always seem to fall short (Problem). This constant compromise can lead to suboptimal performance, increased development time, and even potential safety risks in your final product (Agitation).
But what if I told you there’s a solution that allows you to have a transformer tailored precisely to your application’s needs? Custom encapsulated PCB transformers offer the flexibility to specify every detail, from electrical parameters to mechanical dimensions and environmental ratings (Solution). In this blog post, I’ll guide you through the process of buying custom encapsulated transformers, ensuring you get a product that seamlessly integrates into your design and delivers reliable, efficient power conversion. Say goodbye to compromises and hello to a truly customized solution that unlocks new levels of performance and peace of mind.
Step 1: Define Your Requirements
The first and most critical step in purchasing custom encapsulated PCB transformers is to clearly define your requirements. This involves understanding the specific application and operating conditions in which the transformer will be used. By providing comprehensive specifications, you ensure that the manufacturer can design a product that meets your exact needs.
1.Input Voltage
115VAC or 230VAC, 50/60Hz
Specify any allowable voltage tolerance, e.g. ±10%
2.Output Voltage
12VAC, 24VAC or other common low voltages
Specify if multiple output windings are required
3.VA Rating
Typical range from 0.5VA to 30VA
Determine the required VA rating based on output voltage and current
For example, if you require a 24VAC output at 1A, the VA rating would be 24VA.
4.Operating Frequency
50Hz or 60Hz line frequency operation
5.Temperature Range
Operating Ambient: Typical 0°C to +40°C
Some models rated for -20°C to +70°C
6.Insulation Requirements
Primary to Secondary: Reinforced insulation per safety standards, e.g. 4000VAC for 1 minute
Primary to Core: Basic or reinforced as required, e.g. 1500VAC for 1 minute
7.Safety Approvals
IEC/EN/UL safety certification needed? E.g. IEC 61558-1, IEC 61558-2-16
Any additional regional safety standards? E.g. CCC for China
8.Mechanical Dimensions
Overall size: Length 50mm, Width 40mm, Height 30mm max
Mounting pattern: 4 holes, 3.2mm dia, 40mm x 30mm spacing
Terminal connections: 0.8mm² pins, 20mm lead lengths
9.Environmental
Operating humidity range: Typical 10-90% RH, non-condensing
Any special moisture, chemical, vibration requirements? IP67 rated for moisture resistance
10.Shielding
Faraday shield between primary and secondary windings for EMI reduction?
Electromagnetic shielding requirements? E.g. for medical or military applications

Step 2: Choose the Right Transformer Type
Once you have clearly defined your requirements, the next step is to select the most suitable type of encapsulated PCB transformer for your application. The two main types for low-frequency applications are:
1.EI Laminated Transformers
EI laminated transformers are constructed using stacked layers of insulated steel laminations, forming an “E” and “I” shape when assembled. They offer excellent performance and are widely used in various low-frequency applications, including power supplies, industrial control systems, and instrumentation.
Key advantages of EI laminated transformers include:
·High efficiency and low losses, typically 95-98%
·Good thermal performance and heat dissipation
·Ability to handle higher power levels, up to 3kVA
·Cost-effective for medium to high production volumes
For example, a common EI28 laminated transformer can handle up to 100VA at 50/60Hz with an efficiency of 96%.
2.Toroidal Transformers
Toroidal transformers feature a doughnut-shaped core made of wound strips of silicon steel. They are known for their low electromagnetic interference (EMI) emissions, compact size, and high efficiency, making them suitable for applications where space is limited or EMI is a concern.
Key advantages of toroidal transformers include:
·Excellent EMI shielding due to their circular design
·Compact size and low profile for space-constrained applications
·High efficiency, typically 97-99%
·Low external magnetic fields and low noise operation
For example, a typical 50VA toroidal transformer might have dimensions of 50mm OD x 25mm H, with an efficiency of 98%.
Both EI laminated and toroidal transformers can be encapsulated in various materials, such as epoxy resin or polyurethane, to provide protection against moisture, chemicals, and mechanical stress.
Step 3: Select a Reputable Manufacturer
Choosing the right manufacturer for your custom encapsulated PCB transformers is crucial to ensuring high quality, reliability, and timely delivery. At Unicreed, we pride ourselves on our expertise and commitment to meeting our customers’ unique requirements.
As a factory with five production lines and a focus on B2B wholesale, we have the capability to handle large-volume orders while maintaining strict quality control measures. Our team of experienced engineers works closely with customers to understand their specific needs and provide tailored solutions.
When selecting a manufacturer, consider the following 4 factors:
1.Experience and Expertise
Look for a manufacturer with a proven track record in designing and producing custom encapsulated PCB transformers. Experienced manufacturers like Unicreed have the knowledge and resources to tackle complex design challenges and deliver high-quality products.
For example, Unicreed has been manufacturing transformers for over 15 years and has supplied products to leading electronics companies worldwide.
2.Manufacturing Capabilities
Ensure that the manufacturer has the necessary equipment and facilities to produce your custom encapsulated PCB transformers. This includes advanced winding machines, vacuum impregnation systems, and testing equipment to ensure consistent quality.
At Unicreed, we have state-of-the-art winding machines capable of handling wire sizes from 0.05mm to 2.0mm, and our vacuum impregnation systems ensure complete encapsulation and protection.
3.Quality Control and Certifications
Prioritize manufacturers with robust quality control processes and relevant certifications, such as ISO 9001 or industry-specific certifications. These certifications demonstrate a commitment to quality and adherence to industry standards.
Unicreed is ISO 9001:2015 certified and follows strict quality control procedures, including 100% electrical testing and sample-based environmental stress testing.
4.Customer Support and Communication
Effective communication and responsive customer support are essential throughout the design and production process. Look for a manufacturer that values open communication and is willing to work closely with you to address any concerns or modifications.
At Unicreed, we assign a dedicated project manager to each customer to ensure seamless communication and prompt response to any inquiries or issues.
By partnering with a reputable manufacturer like Unicreed, you can have confidence in the quality and reliability of your custom encapsulated PCB transformers, ensuring optimal performance in your electronic systems.
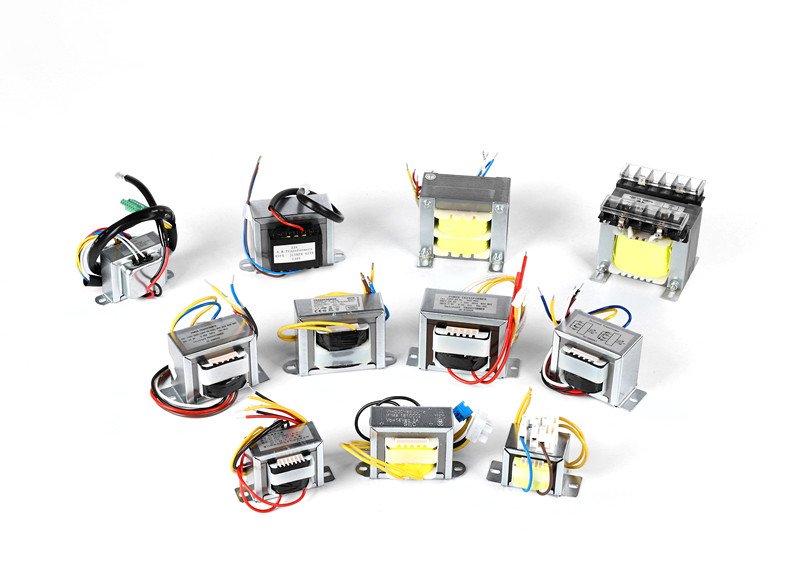
Step 4: Provide Detailed Specifications
Once you have selected a manufacturer, the next step is to provide detailed specifications for your custom encapsulated PCB transformer. Clear and comprehensive specifications are crucial to ensuring that the manufacturer fully understands your requirements and can deliver a product that meets your exact need.
When providing specifications, include the following 5 information:
1.Electrical Parameters
Specify the input and output voltage levels, current ratings, operating frequency range, and any other relevant electrical parameters, such as insulation requirements or voltage regulation.
For example:
·Input: 230VAC ±10%, 50Hz
·Output: 24VAC, 2A continuous
·Insulation: Primary to Secondary 4000VAC for 1 minute
2.Mechanical Dimensions
Provide detailed mechanical dimensions, including the overall size, mounting hole locations, and any specific shape or form factor requirements. This information is essential for ensuring proper fit and integration into your electronic system.
For example:
·Overall Size: 60mm x 40mm x 30mm (L x W x H) max
·Mounting: 4 holes, 3.2mm dia, 50mm x 30mm spacing
·Terminals: 0.8mm² pins, 20mm lead lengths
3.Environmental Conditions
Outline the expected operating temperature range, humidity levels, and any other environmental conditions the transformer will be exposed to. This information will guide the selection of appropriate materials and insulation.
For example:
·Operating Temperature: -20°C to +60°C
·Humidity: 10% to 90% RH, non-condensing
·IP67 rated for moisture resistance
4.Safety and Regulatory Compliance
If your application requires compliance with specific safety standards or regulations, clearly communicate these requirements to the manufacturer. This may include certifications such as UL, CE, or RoHS.
For example:
·Safety Approvals: IEC 61558-1, IEC 61558-2-16, UL 506
·RoHS compliant
5.Special Requirements
Specify any additional requirements or constraints, such as EMI shielding, moisture resistance, or mechanical robustness. These factors can significantly impact the transformer’s design and construction.
For example:
·Faraday shield between primary and secondary windings
·Vacuum impregnated with opaque epoxy resin for moisture protection
Effective communication and collaboration with the manufacturer are key to ensuring that your specifications are accurately understood and translated into a custom encapsulated PCB transformer that meets your exact needs.
Step 5: Review Prototypes and Samples
Before approving mass production, it is essential to review prototypes and samples provided by the manufacturer. This step allows you to thoroughly evaluate the custom encapsulated PCB transformer and ensure it meets your specifications and performance requirements.
When reviewing prototypes and samples, consider the following:
1.Electrical Performance Testing
Conduct comprehensive electrical performance testing to verify that the transformer meets the specified input/output voltage levels, current ratings, and operating frequency range. This may involve load testing, efficiency measurements, and other relevant tests specific to your application.
For example, you might perform a load test at 24VAC, 2A to verify the output voltage regulation and temperature rise.
2.Mechanical Inspection
Carefully inspect the mechanical dimensions, mounting holes, and overall form factor to ensure proper fit and integration into your electronic system. Check for any deviations from the provided specifications.
For example, you would measure the overall dimensions and mounting hole locations against the specified tolerances.
3.Environmental Testing
If your application requires operation in specific environmental conditions, such as extreme temperatures or humidity levels, perform relevant environmental testing to ensure the transformer’s performance remains stable under these conditions.
For example, you might conduct a high-temperature test at 70°C for 1000 hours to verify insulation integrity.
4.Safety and Compliance Verification
If applicable, verify that the custom encapsulated PCB transformer meets the required safety and regulatory compliance standards, such as UL or CE certifications.
For example, you would review the safety test reports and certifications provided by the manufacturer.
Functional Testing
Integrate the prototype or sample into your electronic system and perform functional testing to ensure seamless operation and compatibility with other components.
For example, you might test the transformer in your product’s power supply circuit and verify proper operation under various load conditions.
By thoroughly evaluating prototypes and samples, you can identify and address any issues or deviations before approving mass production. This step helps ensure that the final product meets your exact requirements and performs as expected in your application.
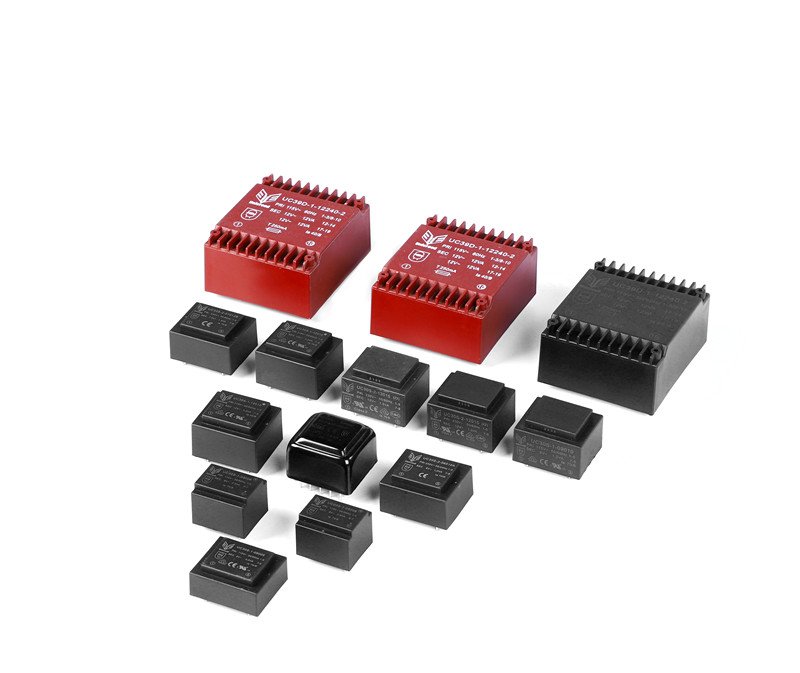
Step 6: Place the Order and Monitor Production
After reviewing and approving the prototypes or samples, you can proceed to place the order for your custom encapsulated PCB transformers. At this stage, it is important to provide any necessary documentation, such as purchase orders or technical specifications, to ensure a smooth production process.
During the production phase, maintain open communication with the manufacturer to address any concerns or changes that may arise. Regular updates and progress reports can help you stay informed and make any necessary adjustments.
Once the production run is complete, the manufacturer should provide you with detailed documentation, including test reports and certifications, if applicable. Thoroughly review this documentation to ensure compliance with your specifications and requirements.
Conclusion:
Purchasing custom encapsulated PCB transformers may seem like a daunting task, but by following a systematic approach and partnering with a reputable manufacturer like Unicreed, you can navigate the process with confidence.
At Unicreed, we understand the importance of delivering high-quality, customized solutions that meet our customers’ unique requirements. With our expertise, state-of-the-art facilities, and commitment to customer satisfaction, we are well-equipped to handle your custom encapsulated PCB transformer needs.
Whether you require transformers for power supplies, industrial control systems, or any other electronic application, our team is ready to work closely with you to understand your specifications and provide tailored solutions
If you have any further questions or would like to discuss your custom encapsulated PCB transformer requirements, please don’t hesitate to contact us at sales@unicreed-transformer.com or visit our website at www.unicreed-transformer.com. We look forward to partnering with you and delivering exceptional products that meet your exact needs.