As electronic devices become smaller, faster, and more powerful, the need for compact and efficient components becomes paramount. Inductor coils, those unassuming yet crucial elements found in transformers, motors, and various electronic circuits, play a pivotal role. However, these seemingly innocent coils can become unexpectedly hot, risking performance degradation, premature component failure, or even safety hazards. Understanding the reasons behind inductor coil heat is key to harnessing their potential without compromising reliability.
In this blog, we embark on a mission to unravel the secrets of inductor coil heat. We will delve into the factors that contribute to this phenomenon, from resistance and core losses to eddy currents and proximity effects. By demystifying the reasons behind inductor coil heat, we aim to equip you with knowledge and insights that will empower you to tackle this challenge effectively. Whether you’re an electronics enthusiast, a design engineer, or simply curious about the inner workings of electronic devices, join us as we uncover the hidden world of inductor coil heat and pave the way for efficient and reliable electronic systems.
What causes inductor coils to heat up?
Inductor coils can heat up due to several factors that contribute to heat generation. Here are five common causes:
1.Resistance:
The electrical resistance of the wire used in the inductor coil leads to the conversion of electrical energy into heat. As current flows through the coil, resistance causes a voltage drop and subsequent power dissipation in the form of heat.
2.Core Losses:
Inductor coils often utilize a magnetic core material, such as ferrite or iron, to enhance their inductance. However, these materials can experience energy losses known as core losses, which result in heat generation. Core losses include hysteresis losses (caused by the reversal of magnetization) and eddy current losses (caused by circulating currents within the core).
3.Eddy Currents:
When an alternating current flows through the inductor coil, it induces eddy currents in nearby conductive materials, such as the coil’s core or nearby metallic components. These eddy currents circulate within the conductive material and lead to resistive losses, converting electrical energy into heat.
4.Proximity Effects:
In some cases, the inductor coil may be located in close proximity to other conductive elements, such as other coils or metallic structures. The proximity effect refers to the interaction between these conductive elements, which can result in additional eddy current losses and heat generation.
5.Frequency and Current:
The operating frequency and current levels flowing through the inductor coil can impact the amount of heat generated. Higher frequencies and larger current magnitudes generally lead to increased resistive losses, core losses, and eddy current losses, resulting in higher temperatures.
How does resistance affect the heating of inductor coils?
Resistance plays a significant role in the heating of inductor coils. When an electric current flows through the coil, the resistance of the wire used in the coil results in power dissipation in the form of heat. Here’s how resistance affects the heating of inductor coils:
Joule Heating: According to Ohm’s law (V = I * R), the voltage drop (V) across a resistor is directly proportional to the current (I) passing through it and the resistance (R) of the resistor. In the case of an inductor coil, the wire used to construct the coil has inherent resistance. As current flows through the coil, the resistance of the wire causes a voltage drop, resulting in the conversion of electrical energy into heat. This phenomenon is known as Joule heating or resistive heating.
Power Dissipation: The power dissipated in an inductor coil can be calculated using the formula P = I^2 * R, where P represents power, I denotes current, and R signifies resistance. This formula demonstrates that power dissipation in the coil is directly proportional to the square of the current flowing through it and the resistance of the wire. As the current or resistance increases, the power dissipation and subsequent heat generation in the coil also increase.
Temperature Rise: The heat generated due to resistance contributes to the temperature rise of the inductor coil. The temperature rise is influenced by the power dissipation, the thermal properties of the coil’s materials, and the heat dissipation capabilities of the surrounding environment. If the heat generated exceeds the coil’s ability to dissipate it, the temperature can rise to a point where it affects the performance, reliability, and lifespan of the coil and the surrounding components.
To mitigate the effects of resistance on heating, designers can consider several strategies, such as using wires with lower resistance (higher conductivity), optimizing the wire gauge, and incorporating heat management techniques like thermal insulation, heat sinks, or cooling mechanisms to dissipate the generated heat effectively.
How does the current level passing through an inductor coil affect its temperature?
The current level passing through an inductor coil has a direct impact on its temperature. Here’s how the current level affects the temperature of an inductor coil:
Joule Heating: When current flows through the wire in an inductor coil, it encounters resistance, which leads to power dissipation in the form of heat. According to Joule’s law, the power dissipated in a resistor is given by P = I^2 * R, where P is the power, I is the current, and R is the resistance. As the current passing through the inductor coil increases, the power dissipation and subsequent heat generation also increase. Therefore, higher current levels result in higher temperatures.
Increased I^2R Losses: The power dissipated in the form of heat, as mentioned above, is directly proportional to the square of the current (I^2) passing through the coil. This means that even a small increase in current can lead to a significant increase in power dissipation and temperature rise. Therefore, as the current level through the inductor coil increases, the I^2R losses also increase, resulting in higher temperatures.
Temperature Rise: The heat generated due to the power dissipation in the inductor coil leads to a temperature rise. The temperature rise is influenced by various factors, including the power dissipation, the thermal properties of the coil’s materials, and the heat dissipation capabilities of the surrounding environment. Higher current levels result in higher power dissipation and, consequently, a more substantial temperature rise.
Are there any strategies to prevent or minimize inductor coil heat?
Yes, there are several strategies you can employ to prevent or minimize inductor coil heat. Here are eight effective approaches:
1.Component Selection:
Choose materials with low resistivity and low core losses for the inductor coil. High-conductivity wire and magnetic core materials with low hysteresis and eddy current losses can help reduce heat generation.
2.Thermal Management:
Implement effective thermal management techniques to dissipate heat from the inductor coil. This can include proper component placement, utilizing heat sinks, adding thermal insulation, employing forced convection (such as fans or blowers), or using liquid cooling systems.
3.Design Optimization:
Optimize the design of the inductor coil and its surrounding components. Consider factors such as wire size, winding technique, core material selection, and coil layout to minimize resistance and maximize heat dissipation capabilities.
4.Current and Frequency Considerations:
Carefully select the operating current and frequency levels for the inductor coil. Higher currents and frequencies can lead to increased heat generation. If possible, choose lower current levels or spread the load across multiple coils to distribute the heat dissipation.
5.Airflow and Ventilation:
Ensure proper airflow and ventilation around the inductor coil. Allow sufficient space for air circulation to remove heat and prevent heat buildup. Avoid enclosing the coil in areas with limited airflow or high ambient temperatures.
6.Thermal Insulation:
Apply thermal insulation materials or coatings to isolate the inductor coil from heat sources or other components that may contribute to heat buildup.
7.Temperature Monitoring:
Incorporate temperature monitoring mechanisms to keep track of the inductor coil’s temperature. This can include using thermal sensors or thermal imaging to detect any excessive temperature rise and trigger necessary actions for heat management.
8.Simulation and Analysis:
Utilize software tools or simulations to analyze and predict the thermal behavior of the inductor coil under different operating conditions. This can help identify potential hotspots and optimize the design for better heat dissipation.
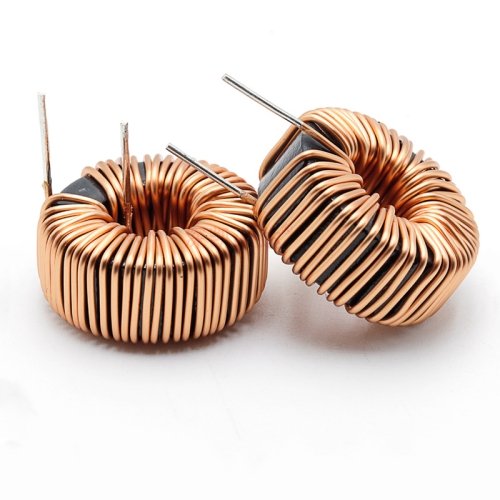
What considerations should be taken into account when designing inductor coils to mitigate heat generation?
When designing inductor coils to mitigate heat generation, several considerations should be taken into account. Here are eight key factors to consider:
1.Wire Selection:
Choose a wire with low resistivity and high conductivity to minimize resistive losses and subsequent heat generation. Copper is commonly used due to its excellent conductivity. Consider the wire gauge and diameter, as thicker wires generally have lower resistance.
2.Core Material:
Select a magnetic core material with low hysteresis and eddy current losses. Different core materials have varying magnetic properties and associated losses. Ferrite cores are commonly used for their low losses, while iron cores have higher losses but higher permeability.
3.Inductance and Current Rating:
Determine the desired inductance value and current-carrying capacity of the coil. Oversizing the inductor can lead to higher resistance and heat generation. Balance the inductance requirement with the space and current constraints to optimize the design.
4.Coil Geometry:
Optimize the coil’s geometry, including the number of turns, winding technique, and coil shape, to minimize resistance and maximize heat dissipation. Proper spacing between the turns can help reduce proximity effects and minimize eddy current losses.
5.Thermal Management:
Implement effective thermal management techniques to dissipate heat from the inductor coil. Consider the placement of the coil within the circuit or system to facilitate heat dissipation. This can include incorporating heat sinks, utilizing thermal pads or insulators, or providing adequate ventilation.
6.Operating Conditions:
Consider the operating frequency and current levels of the inductor coil. Higher frequencies and larger current magnitudes generally lead to increased heat generation. Design the coil to accommodate these operating conditions and ensure the components can handle the associated power dissipation.
7.Simulation and Analysis:
Utilize software tools or simulations to analyze the thermal behavior of the inductor coil under different operating conditions. This can help identify potential hotspots and optimize the design for better heat dissipation.
8.Compliance with Standards:
Consider any industry standards or guidelines for inductor coil design and thermal management. Compliance with relevant standards ensures the coil’s performance, reliability, and safety.
Are there specific materials or components that help dissipate heat from inductor coils more effectively?
Yes, there are specific materials and components that can help dissipate heat from inductor coils more effectively. Here are seven examples for your reference:
1.Heat Sinks:
Heat sinks are commonly used components to dissipate heat. They provide a larger surface area for heat transfer and can be made of materials such as aluminum or copper. Heat sinks are often attached to the inductor coil or its surrounding components to absorb and dissipate heat through conduction and convection.
2.Thermal Pads and Insulators:
Thermal pads or insulating materials with good thermal conductivity can be used to improve heat transfer between the inductor coil and its surroundings. These materials help reduce thermal resistance and facilitate efficient heat dissipation.
3.Thermal Vias:
In PCB (Printed Circuit Board) designs, thermal vias can be incorporated to enhance heat dissipation. These are small holes filled with thermally conductive materials that connect different layers of the PCB, allowing heat to transfer more efficiently from the inductor coil to the board and its underlying layers.
4.Liquid Cooling Systems:
In high-power applications, liquid cooling systems can be employed to dissipate heat effectively. These systems circulate a coolant, such as water or a specialized fluid, through channels or pipes in close proximity to the inductor coil, absorbing heat and carrying it away from the coil.
5.Fans and Blowers:
Fans or blowers can be utilized to create airflow around the inductor coil, promoting convective heat transfer. By directing air over the coil, these components enhance heat dissipation and help maintain lower temperatures.
6.Thermal Conductive Adhesives:
Thermal conductive adhesives can be used to bond the inductor coil to other components or heat sinks, improving thermal coupling and facilitating heat transfer between surfaces.
7.Thermal Management Materials:
Various thermal management materials, such as thermal interface materials (TIMs), thermal greases, or phase change materials (PCMs), can be applied between the inductor coil and adjacent components to enhance thermal conductivity and improve heat dissipation.
The selection and implementation of these materials and components depend on the specific application, available space, and thermal management requirements. It is recommended to consider the thermal characteristics, compatibility, and reliability of these materials while designing and optimizing the heat dissipation of inductor coils.
How can I measure the temperature of an inductor coil accurately?
Measuring the temperature of an inductor coil accurately can be achieved using various temperature sensing techniques. Here are five commonly used methods:
1.Thermocouples:
Thermocouples are temperature sensors that utilize the principle of the Seebeck effect. They consist of two dissimilar metal wires joined together at one end to form a junction. The temperature difference between the junction and the other end generates a voltage, which is measured to determine the temperature. Thermocouples can be attached to the surface of the inductor coil or placed in close proximity to it for temperature measurement.
2.Resistance Temperature Detectors (RTDs):
RTDs are temperature sensors that utilize the change in electrical resistance of a metal wire with temperature. Typically, platinum is used as the sensing element in RTDs due to its stable and predictable resistance-temperature relationship. RTDs can be bonded to the surface of the inductor coil or positioned nearby to monitor the temperature accurately.
3.Thermistors:
Thermistors are temperature-sensitive resistors that exhibit a large change in resistance with temperature. They are commonly made of ceramic or semiconductor materials. Thermistors can be mounted on or near the inductor coil to measure temperature. They provide a relatively quick response and can be cost-effective for temperature monitoring.
4.Infrared (IR) Temperature Sensors:
Infrared temperature sensors, also known as non-contact or pyrometers, measure the infrared radiation emitted by an object to determine its temperature. These sensors can be used to measure the surface temperature of the inductor coil without physical contact. However, it’s important to ensure that the inductor coil’s emissivity and other factors are considered to obtain accurate temperature readings.
5.Integrated Circuit (IC) Temperature Sensors:
Some ICs come equipped with built-in temperature sensors, often referred to as on-chip temperature sensors. These sensors provide temperature readings based on the temperature-dependent characteristics of the integrated circuit itself. They can be useful for monitoring the temperature of the coil and the surrounding components.
When selecting a temperature measurement method, consider factors such as measurement range, accuracy requirements, response time, sensor compatibility, and cost. It’s recommended to refer to the sensor’s datasheet and follow the manufacturer’s guidelines for installation and calibration to ensure accurate temperature measurements of the inductor coil.
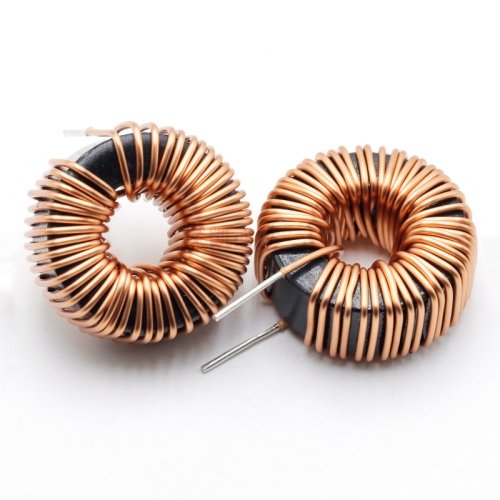
Can changing the operating conditions, such as frequency or current levels, help reduce inductor coil heat?
Yes, changing the operating conditions, such as frequency or current levels, can help reduce inductor coil heat. Here’s how:
- Frequency: Lowering the operating frequency can help reduce inductor coil heat. Higher frequencies generally lead to increased power dissipation and heat generation in the coil due to increased resistive losses. By operating at a lower frequency, the current passing through the coil can be reduced, resulting in lower heat generation.
- Current Levels: Reducing the current levels flowing through the inductor coil can effectively decrease heat generation. As discussed earlier, the power dissipated in the coil is directly proportional to the square of the current (P = I^2 * R). Therefore, by decreasing the current, the power dissipation and subsequent heat generation can be significantly reduced.
- Current Distribution: If possible, distributing the load across multiple inductor coils instead of relying on a single coil can help reduce heat generation. By splitting the current between multiple coils, the power dissipation in each coil is reduced, resulting in lower heat buildup.
- Duty Cycle: For applications involving pulse-width modulation (PWM), adjusting the duty cycle can impact heat generation. By reducing the duty cycle (i.e., reducing the ON time of the PWM signal), the average current flowing through the coil decreases, leading to lower heat generation.
How can I balance the trade-off between minimizing heat generation and maximizing inductor coil performance?
Balancing the trade-off between minimizing heat generation and maximizing inductor coil performance requires careful consideration and a systematic approach. Here are seven strategies to help achieve this balance:
- Optimize Coil Design: Start by optimizing the design of the inductor coil itself. Consider factors such as wire gauge, number of turns, core material, and winding technique. By selecting appropriate parameters, you can minimize resistance, core losses, and other factors that contribute to heat generation while maintaining the desired inductance and performance characteristics.
- Material Selection: Choose materials with low resistivity and low core losses for the inductor coil. High-conductivity wire and magnetic core materials with low hysteresis and eddy current losses can help reduce heat generation. Select materials that strike a balance between thermal efficiency and electrical performance.
- Thermal Management: Implement effective thermal management techniques to dissipate heat from the inductor coil. This includes considerations such as proper component placement, heat sinks, ventilation, and thermal insulation. By efficiently managing heat dissipation, you can minimize temperature rise while maintaining optimal performance.
- Operating Conditions: Optimize the operating conditions of the inductor coil based on the specific requirements of your application. Consider factors such as frequency, current levels, and duty cycle. Carefully select the operating parameters to balance the desired performance with acceptable heat generation.
- Simulation and Analysis: Utilize software tools or simulations to analyze and predict the thermal behavior of the inductor coil under different operating conditions. This can help identify potential hotspots and optimize the design for better heat dissipation while evaluating the impact on performance.
- Component Selection: Choose high-quality components with suitable power ratings and thermal characteristics. Components that are designed to handle higher temperatures and power dissipation can help maintain performance while minimizing the impact of heat generation.
- Testing and Validation: Perform thorough testing and validation to ensure that the inductor coil meets the required performance criteria while managing heat effectively. Monitor temperature during operation and validate that it remains within acceptable limits.
Are there any alternative technologies or components that can be used to mitigate inductor coil heat?
Yes, there are alternative technologies and components that can be used to mitigate inductor coil heat. Here are six examples:
1.Magnetic Core Materials:
Using advanced magnetic core materials can help reduce core losses and, subsequently, heat generation in inductor coils. Some examples include soft magnetic composites (SMCs) and nanocrystalline cores, which have lower core losses compared to traditional materials like ferrites or iron cores.
2.Air-Core Inductors:
Air-core inductors do not use a magnetic core and rely on the self-inductance of the coil. Since there is no core material present, there are no core losses, resulting in reduced heat generation. However, air-core inductors may have lower inductance values and can be physically larger compared to traditional core-based inductors.
3.High-Frequency Inductors:
Operating at higher frequencies can allow for the use of smaller inductor coils, which inherently generate less heat due to reduced resistive losses. High-frequency inductors, designed specifically for high-frequency applications, can have lower resistance and core losses, resulting in improved efficiency and reduced heat generation.
4.Integrated Magnetics:
Integrated magnetics is a technology that combines inductors, transformers, or other magnetic components with power electronics on a single substrate or chip. By integrating these components, the parasitic resistive losses and heat generation can be minimized. Integrated magnetics can be used in applications such as power converters and voltage regulators.
5.Planar Inductors:
Planar inductors are constructed using flat, layered structures, typically with printed circuit board (PCB) technology. They offer low profile, compact size, and efficient heat dissipation due to their planar geometry. Planar inductors can be designed with low resistance and improved thermal characteristics.
6.Soft-Switching Techniques:
Soft-switching techniques, such as zero-voltage switching (ZVS) or zero-current switching (ZCS), can be employed in power electronic circuits. These techniques reduce switching losses and, subsequently, heat generation in the inductor coil and other components. By optimizing the switching waveforms, the overall efficiency can be improved, leading to reduced heat dissipation.
Where can I find further resources or expert advice on addressing inductor coil heat-related issues?
Check the websites of Unicreed, they are inductor manufacturers. They often provide application notes, design guides, and technical resources that address heat-related issues in inductor coils. We can provide valuable insights into selecting the right inductor, thermal management techniques, and best practices for minimizing heat generation. Here is our website: www.unicreed-transformer.com
Understanding the reasons for inductor coil heat is of utmost significance in the field of electronics and power systems. Excessive heat generation can lead to performance degradation, reduced efficiency, and even failure of electronic components. By comprehending the factors that contribute to inductor coil heat, engineers and designers can make informed decisions to minimize heat-related issues, enhance system reliability, and optimize the overall performance of their circuits and devices.
Now armed with knowledge about the reasons for inductor coil heat, we encourage you to apply this understanding to your own projects or situations. Consider the design and operating conditions of your inductor coils, assess potential heat-generating factors, and implement appropriate measures to mitigate heat. Refer to recommended resources, consult experts, and leverage simulation tools to enhance your understanding and decision-making process.
In conclusion, unraveling the reasons behind inductor coil heat empowers you to optimize your designs, enhance system performance, and ensure the longevity of your electronic devices. With a thorough understanding of the factors at play, you are well-equipped to tackle heat-related challenges and create more efficient, reliable, and robust electronic systems.