What are the most significant cost factors in high-frequency transformer design?
There are several significant cost factors in high-frequency transformer design. Here are some of the most important ones:
- Core Material: The choice of core material for a high-frequency transformer can significantly affect its cost. Higher quality and more efficient core materials such as amorphous metal or nanocrystalline materials are more expensive compared to traditional silicon steel.
- Wire and Insulation: The choice of wire and insulation material for winding the transformer can impact its cost. Copper wire is commonly used in high-frequency transformers, but the gauge and number of wires used can affect the cost. The type of insulation material and its thickness can also impact the cost.
- Bobbin and Enclosure: The design and material of the bobbin or enclosure used to hold the transformer’s components can also impact its cost. More complex designs or higher quality materials will cost more.
- Manufacturing Processes: The manufacturing process used to produce the high-frequency transformer can also significantly impact its cost. The use of automated processes or more efficient production methods can reduce costs.
- Quantity: The quantity of high-frequency transformers being produced can also impact the cost per unit. Higher volume production can lead to lower unit costs due to economies of scale.
What are the benefits of using high-frequency transformers in electronic devices?
When used in electronic devices, high-frequency transformers offer a number of benefits, including the following:
- High Efficiency: High-frequency transformers are designed to operate at high frequencies, which allows for higher power transfer efficiency, resulting in lower energy losses and reduced operating costs.
- Compact Size: High-frequency transformers can be designed to be much smaller and lighter than traditional transformers, making them ideal for use in compact electronic devices.
- Improved Performance: High-frequency transformers can provide better performance in terms of noise reduction, voltage regulation, and waveform shaping, leading to better overall device performance.
- Reduced Electromagnetic Interference (EMI): High-frequency transformers can be designed to have lower EMI emissions, which can help reduce interference with other devices and improve overall system performance.
- Wide Range of Applications: High-frequency transformers can be used in a wide range of electronic devices, including power supplies, converters, inverters, and more, making them highly versatile and adaptable to various applications.
- Enhanced Safety: High-frequency transformers can provide enhanced safety by isolating the primary and secondary circuits, reducing the risk of electric shock, and protecting sensitive electronic components from power surges and overloads.
How can I reduce the cost of my high-frequency transformer design without sacrificing quality?
Reducing the cost of a high-frequency transformer design can be challenging, but there are several strategies that you can consider to reduce costs without sacrificing quality. Here are a few tips:
- Choose the Right Core Material: Core material is one of the most significant cost factors in transformer design. Consider using lower-cost materials such as traditional silicon steel, which is widely available and more affordable.
- Optimize the Design: Analyze the transformer design and identify areas that can be optimized to reduce costs, such as reducing the number of windings or using thinner wire gauge to reduce the amount of copper needed.
- Use Automation: Automating the transformer manufacturing process can reduce labor costs and increase production efficiency. Consider using automated winding machines or robotics to help reduce costs.
- Consider Sourcing from Lower-Cost Regions: Sourcing materials or components from lower-cost regions can help reduce costs. However, be sure to carefully evaluate the quality and reliability of the supplier to ensure that the cost savings do not come at the expense of quality.
- Use Simulation Tools: Use simulation tools to optimize the transformer design and evaluate different materials and configurations. This can help identify cost-effective solutions without sacrificing quality.
- Partner with a Skilled Manufacturer: Working with a skilled transformer manufacturer can help ensure that your design is optimized for cost and quality. A skilled manufacturer can help identify opportunities to reduce costs without sacrificing quality and can provide expertise in sourcing materials and components.
What materials are typically used in high-frequency transformer design, and how do they affect cost?
High-frequency transformers are designed to operate at frequencies above the range of traditional 50/60 Hz transformers. The materials used in high-frequency transformer design depend on the operating frequency, power level, and performance requirements of the transformer. Some common materials used in high-frequency transformer design include:
- Ferrite: Ferrite cores are made from a ceramic material that contains iron oxide. They are commonly used in high-frequency transformer design due to their high permeability, low losses, and low magnetic hysteresis. Ferrite cores are widely used in power supplies, converters, and inverters. The cost of ferrite cores is moderate.
- Powdered Iron: Powdered iron cores are made from compressed iron powder, and they have excellent magnetic properties at high frequencies. Powdered iron cores are used in applications that require high power levels, such as inductors for power electronics. The cost of powdered iron cores is moderate to high.
- Amorphous Metal: Amorphous metal cores are made from a thin ribbon of metal that is rapidly solidified to produce a non-crystalline structure. They have high magnetic permeability and low core losses, making them ideal for high-frequency transformer applications. The cost of amorphous metal cores is relatively high.
- Nanocrystalline Metal: Nanocrystalline metal cores are made from a thin ribbon of metal that is annealed to produce a nanocrystalline structure. They have high magnetic permeability, low core losses, and excellent thermal stability, making them ideal for high-frequency transformer applications. The cost of nanocrystalline metal cores is relatively high.
The cost of high-frequency transformer materials varies depending on the material type, core size, and core shape. Ferrite cores are generally the most cost-effective option, while amorphous and nanocrystalline metal cores are more expensive. In addition to the core material, other factors that can affect the cost of high-frequency transformer design include the wire used for winding, insulation materials, and manufacturing processes.
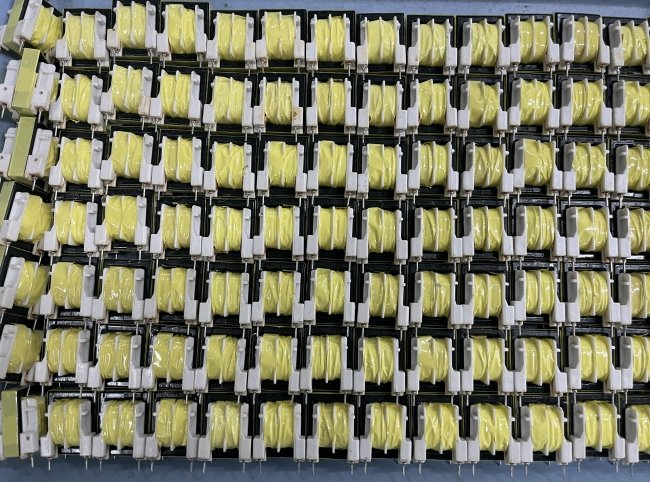
How do I balance the trade-off between cost and performance in high-frequency transformer design?
Balancing the trade-off between cost and performance in high-frequency transformer design requires careful consideration of several factors, including the transformer’s application, performance requirements, and budget. Here are some tips on how to balance cost and performance in high-frequency transformer design:
- Define the transformer’s performance requirements: Determine the transformer’s specifications, such as operating frequency, power rating, voltage rating, and efficiency. These specifications will guide the selection of the transformer’s core material, wire gauge, and other components.
- Identify the application: Determine the transformer’s application, including the environment, operating conditions, and reliability requirements. For example, if the transformer will be used in a harsh environment or high-temperature application, you may need to choose a material with better thermal properties, such as nanocrystalline metal.
- Compare the cost of different materials: Evaluate the cost of different core materials, wire types, and insulation materials. For example, ferrite cores are less expensive than nanocrystalline metal cores, but they have lower efficiency and higher losses.
- Optimize the design: Optimize the transformer’s design to maximize performance while minimizing cost. This can involve selecting the most cost-effective materials, optimizing the winding geometry, and using simulation software to optimize the design for the transformer’s specific application.
- Consider manufacturing and testing costs: Consider the cost of manufacturing and testing the transformer. Some materials may require more complex manufacturing processes, which can increase the overall cost of the transformer.
What are some common mistakes to avoid when designing high-frequency transformers to minimize costs?
Designing high-frequency transformers to minimize costs can be challenging, and there are several common mistakes that designers should avoid. Here are some of the most common mistakes to avoid when designing high-frequency transformers to minimize costs:
- Choosing the wrong core material: Selecting the wrong core material can result in lower performance and higher costs. It is important to select a core material that is appropriate for the application and operating conditions, such as ferrite cores for low power applications and nanocrystalline metal cores for high power applications.
- Overdesigning the transformer: Overdesigning the transformer can result in higher material and manufacturing costs. It is important to carefully evaluate the transformer’s performance requirements and select components that meet those requirements without adding unnecessary cost.
- Ignoring the wire size: Using the wrong wire size can lead to increased losses and lower efficiency. It is important to select the appropriate wire size based on the transformer’s specifications, such as the required current and voltage levels.
- Neglecting thermal considerations: High-frequency transformers can generate significant heat, which can degrade performance and reliability. It is important to consider the transformer’s thermal requirements and select materials and designs that can withstand the expected operating conditions.
- Skipping testing and validation: Skipping testing and validation can lead to costly mistakes and poor performance. It is important to test and validate the transformer design to ensure it meets the required performance and reliability specifications.
- Not considering manufacturing costs: Neglecting manufacturing costs can lead to unexpected expenses and delays. It is important to consider the manufacturing process when designing the transformer and select materials and designs that are cost-effective to produce.
How can I ensure the reliability and longevity of my high-frequency transformer design while keeping costs low?
Designing a reliable and long-lasting high-frequency transformer while keeping costs low can be challenging. However, there are several steps you can take to increase the chances of success:
- Properly size your transformer: Ensure that your transformer is appropriately sized for the application, taking into account factors such as input voltage, output voltage, current requirements, and frequency. Oversizing or undersizing the transformer can result in poor efficiency, increased heat generation, and reduced reliability.
- Use high-quality materials: The choice of materials used in the transformer can have a significant impact on its performance and longevity. Choose materials with low core loss and high magnetic permeability, such as ferrite or laminated cores, and use high-quality copper wire for the windings. Also, consider using high-temperature insulation materials to ensure the transformer can handle the heat generated during operation.
- Optimize the winding configuration: The winding configuration can have a significant impact on the transformer’s performance and reliability. Consider using interleaved or multi-layer windings to reduce winding resistance and improve efficiency. Also, ensure that the windings are well-insulated to prevent short circuits and reduce losses.
- Use proper cooling techniques: High-frequency transformers generate heat, which can impact their reliability and longevity. Ensure that the transformer is adequately cooled by using appropriate cooling techniques, such as forced-air cooling, liquid cooling, or heat sinks.
- Test and validate the design: Before moving to production, test and validate the transformer design to ensure it meets performance specifications and reliability requirements. Use simulation software to predict the transformer’s behavior under different operating conditions and perform physical testing to verify the simulation results.
How do I select the appropriate high-frequency transformer topology for my application to minimize costs?
Selecting the appropriate high-frequency transformer topology for your application can help minimize costs while meeting performance requirements. Here are some factors to consider when selecting the topology:
- Power rating: Consider the power rating of the transformer required for your application. Some topologies are better suited for high-power applications, while others are more suitable for low-power applications.
- Operating frequency: Consider the operating frequency of the transformer required for your application. Some topologies are better suited for high-frequency applications, while others are more suitable for low-frequency applications.
- Efficiency: Consider the efficiency requirements for your application. Some topologies have higher efficiency than others, which can help reduce power losses and lower costs.
- Size and weight: Consider the size and weight requirements for your application. Some topologies are more compact and lightweight than others, which can help reduce costs.
- Complexity: Consider the complexity of the topology required for your application. Some topologies are simpler than others, which can help reduce costs.
Based on these factors, here are some popular high-frequency transformer topologies:
- Flyback transformer: This topology is suitable for low-to-medium power applications and is commonly used in power supplies for consumer electronics. Flyback transformers are simple and cost-effective but have lower efficiency than other topologies.
- Forward transformer: This topology is suitable for high-power applications and is commonly used in power supplies for industrial applications. Forward transformers have higher efficiency than flyback transformers but are more complex and expensive.
- Push-pull transformer: This topology is suitable for high-power applications and is commonly used in high-frequency inverters and converters. Push-pull transformers have high efficiency but are more complex and expensive than flyback transformers.
- Half-bridge transformer: This topology is suitable for medium-to-high power applications and is commonly used in high-frequency inverters and converters. Half-bridge transformers have high efficiency and are less complex and expensive than push-pull transformers.
By considering these factors and selecting the appropriate topology for your application, you can minimize costs while meeting performance requirements.
What are some cost-effective alternatives to high-frequency transformer design that I can consider?
It is possible to design a high-frequency transformer using several cost-effective alternatives. Some of these alternatives are:
- Inductors: Inductors are a cost-effective alternative to high-frequency transformers. They can be used to store energy in a magnetic field and are commonly used in low-frequency applications. They are smaller in size and cheaper than high-frequency transformers, making them an attractive option for cost-sensitive designs.
- Capacitors: Capacitors can be used to store energy in an electric field and are also a cost-effective alternative to high-frequency transformers. They are commonly used in low-frequency applications and can be used to filter out noise from the power supply.
- Switched-mode power supplies (SMPS): SMPS are a cost-effective alternative to high-frequency transformers. They are commonly used in low to medium power applications and are highly efficient. They use high-frequency switching to regulate the output voltage and current, eliminating the need for a high-frequency transformer.
- Flyback converters: Flyback converters are another cost-effective alternative to high-frequency transformers. They are commonly used in low to medium power applications and can operate at high frequencies. They use a transformer to store energy in a magnetic field and are highly efficient.
- Buck-boost converters: Buck-boost converters are another cost-effective alternative to high-frequency transformers. They are commonly used in low to medium power applications and can operate at high frequencies. They use an inductor to store energy and are highly efficient.
In summary, there are several cost-effective alternatives to high-frequency transformer design, including inductors, capacitors, switched-mode power supplies (SMPS), flyback converters, and buck-boost converters. The choice of alternative will depend on the specific requirements of your design.