We discuss common transformer faults and solutions in this article. The faults listed in the article are commonly faults in transformers, and some can only appear in large-capacity power transformers. Repair methods are limited to small faults and only available in professional repair factory/team. It is important to identify the situation based on the actual circumstances.
Types Transformer Faults
In general, the working fault types of transformers are divided into ten different categories as follows:
- Faults Type 1: Failure of the core
- Faults Type 2: Insulation failure
- Faults Type 3: Failure of a component
- Faults Type 4: Fault in the short circuit
- Faults Type 5: The failure of the discharge
- Faults Type 6: Faults in the protection system
- Faults Type 7: The oil spill
- Faults Type 8: A live fault with oil flow
- Faults Type 9: An attack by lightning
- Faults Type 10: Incident of flooding
Transformer Faults and Protection
1. Fault caused by short circuit current
Short-circuiting a transformer suddenly can cause its high-voltage and low-voltage windings to pass through the short-circuit current dozens of times of their rated value together, which generates a lot of heat. Short-circuit currents cannot be withstand by the transformer and its thermal stability is lacking, resulting in serious damage to its insulating material, causing a breakdown and failure.
There are four main types of transformer short circuits: three-phase, two-phase, single-phase ground, and two-phase ground. According to statistics, single-phase-to-ground short circuits account for about 65% of all short-circuit faults, while two-phase short circuits account for about 10% to 15% and two-phase ground short circuits account for about 15% to 20%. Three-phase short circuits account for about 5%. One of the largest short-circuit current values is that of a three-phase short-circuit.
The short-circuit impedance between the high, medium, and low voltages of a 220kV three-winding transformer is usually between 10% and 30%. Medium-voltage to low-voltage short-circuit impedances are usually below 10%, so a short-circuit fault in a transformer will damage the transformer insulation material by heating up.

2. Electromotive force during a short circuit leads to winding deformation
Transformers that are impacted by short-circuits have relay protection that will function properly if there is a small short-circuit current, and the windings will deform only slightly. When the slight deformation is not repaired in time, let it be restored to the original position, tighten up the pressure nails of the winding, tighten up the pull plate and pull rod of the iron yoke, and strengthen the clamping force of the lead wire. It will also damage the transformer.For this reason, diagnosing winding deformation and formulating a reasonable transformer maintenance cycle are important measures to improve short-circuit resistance.
When the winding is suddenly short-circuited, the current-carrying wire is subjected to the electromotive force due to magnetic leakage in the winding. Leakage of flux can usually be decomposed into vertical and horizontal components. Magnetic fields in the longitudinal direction induce radial forces on windings, while magnetic fields in the transverse direction induce axial forces. Axial force puts the entire winding under tension P1, causing tensile stress to develop in the wire. The inner winding is compressed by force P2, while the wire is stressed by compression.
Axial force is divided into two parts, one being due to the interaction between the radial component of the magnetic leakage bending part of the winding end and the current-carrying conductor. There is pressure applied to both the inner and outer windings: the pressure is greater at the end, but almost zero in the middle of the winding, and the direction of the force changes at the other end. The other part of the axial force is due to the radially leaky magnetic flux generated by the imbalance of the inner and outer ampere-turns and the current-carrying conductor, which compresses the inner winding and pulls the outer winding; Axial force increases with ampere-turn imbalance.
The transformer winding will be subjected to large axial and radial electrical forces when a short-circuit occurs. An electromotive force compresses the winding to the middle. This mechanical stress may result in damage to the insulation between turns; A radial electric force may cause the winding to expand outward and lose stability, damaging phase-to-phase insulation. Too much electrical force can tangle the winding or break the wire.
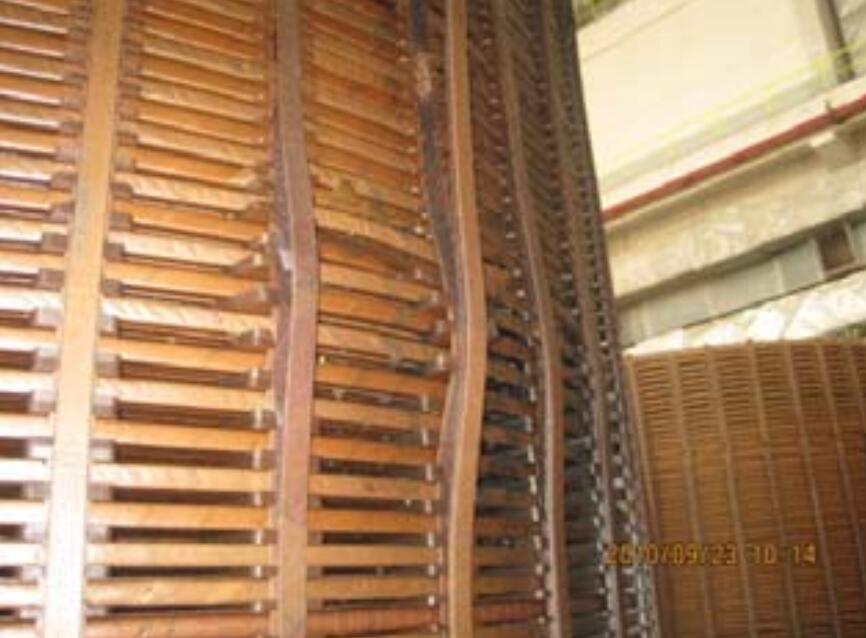
3. The characteristics of winding deformation
Several failures and accidents have been directly caused by deformation of transformer windings found by post-mortem analysis of faulty or accidental transformers. Transformer windings that are seriously deformed and continue to operate without diagnosis are very likely to cause an accident, and a power outage could cause the transformer to burn out. Winding deformation is mainly due to insufficient mechanical structure strength of the winding, rough winding process, poor ability to withstand short-circuit current impact, and poor external mechanical impact.The deformation of transformer windings is mainly influenced by electromotive force and external mechanical force, and electromotive force is more dominant. For example, the short-circuit impulse current created by the short circuit of the transformer outlet and the generated electromotive force will distort and deform the winding.
1)Electrodynamics affects deformation
a. High-voltage windings are subjected to axial tensile and radial expansion stress, causing pressure nails at the ends to loosen and pads to fly out. As the winding is relaxed, its height increases.
b. In the inner column or the middle, the position of the low voltage and middle windings is often affected by axial and radial compression forces, causing the fastening nails to loosen and the spacers to move; Besides the displaced spacers, the struts are inclined, and the pie is polygonally bent in the spoke direction. During light deformation, the outer circle of the 35kv wire cake does not deform, but the inner circle twists and protrudes inward, especially when the winding lining is soft paper. When the relay protection action exceeds 2 seconds when a transformer is shorted, the deformation will be more severe, resulting in a wire cake that has a large concave and upturning area. As the transformer is operated, the height of the entire winding decreases, and the vibration of the transformer box increases significantly.
c. The winding tap and correction areas of the wire cake are deformed. Due to the unbalanced ampere-turn of the tap and splice areas (usually at the head end of the windings), the transverse leakage magnetic field is generated, so the electric force received by the wire cake during short circuit is much larger than that in the normal area, so it is easy to cause deformation and damage. The winding in the tap area will deform into waves when the on-load tap switch causes a short-circuit fault in the tap section, which affects the smoothness of insulation and oil passages.
d. Lead displacement twist during winding. After a short-circuit fault occurs at the transformer outlet, the electrical power destroys the insulation distance of the winding leads as a result of the short-circuit fault. Leads that are too close to the box wall will discharge, and if the distance between the leads is too close, the insulation will be damaged due to friction, resulting in a latent fault and short circuit.
2)Forces affecting deformation
Overall displacement deformation of transformer windings. A sudden braking of the transport vehicle or the impact and shaking of the transport ship during transportation are the main causes of this deformation. In appropriate reports, gravitational accelerations greater than 3g (g is gravitational acceleration) on the transformer’s body can cause its coil to displaced significantly in one direction in the radial direction.
5 Power Transformer Faults and Solution:
The most common faults and causes of power transformers are listed below:
Faults 1:Sounds that are unusual
Reason:
- Noise problems may be caused by a problem with the transformer core. For example,a clamp or screw holding down the core is loose.
- A boiling sound is heard in the audio, as well as “gurgling” bubbles erupting. It may be that the winding has a serious fault, causing nearby parts to heat up and vaporize. There is a bad connection or severe overheating at a local point with the tap changer, or there is a short circuit between the turns of the transformer. In this case, the transformer should be stopped immediately for inspection.
- Continuous and regular impact or friction in the sound may be caused by mechanical contact with some parts of the transformer due to vibrations of the iron core, or abnormal noises caused by electrostatic discharge. Despite the fact that this kind of sound is abnormal, it does not cause serious harm to the operation. It is not necessary to stop the operation immediately, and it can be eliminated during planned maintenance.
Faults 2:Temperatures that are abnormal
Reason:
- Inter-turn, inter-layer, and inter-strand short circuits in transformers;
- Core of transformer partially shorted;
- Magnetic leakage or eddy current causes the fuel tank and cover to heat up;
- Overload operations for a long period of time, accident overloads;
- The degradation of thermal conditions etc.
Faults 3:The line surge current
Reason:
Inrush of line voltage (or disturbance of line voltage) is the leading cause of transformer failure. The category includes anomalies such as voltage peaks, voltage surges, and line faults.
Faults 4: A lack of manufacturing quality
Reason:
There are loose or unsupported wire ends, loose spacers, poor welding, poor insulation of the core, and insufficient short-circuit strength.
Faults 5:Aging of insulation
Reason:
The transformer has been operating over its nameplate power for a long time. It eventually overloads the transformer, and the high temperature prematurely ages the insulation. The strength of the paperboard on the transformer decreases as it ages. The impact of an external fault can result in the insulation breaking.
The Method of detection and solutions are as follows:

Faults 1. The lead wire failed
Method of detection:
A three-phase DC resistor is unbalanced or the resistance of a single phase is infinite, so it will not conduct.
Solutions:
Find the fault location and regrind and press the parts that have poor contact. If there is a bad solder, resolder it. If the weld surface is insufficient, it should be increased. Insufficient lead cross section needs to be replaced (increased) to meet demand.
Faults 2. Coil failed
Method of detection:
Burnt smell usually occurs when a coil fails. Measures insulation resistance and DC resistance; insulation resistance is zero, DC resistance increases and does not remain constant.
Solutions:
Analyze the fault condition, if the damage is minor, it may be repaired; In severe cases, the coil should be replaced.
Faults 3. An insulation drop
Method of detection:
Transformers are tested routinely for their insulation resistance. If the measured value changes significantly or falls below the requirements of the “Regulations”, then the transformer is damp or the oil insulation resistance has dropped.
Solutions:
If the transformer’s insulation resistance drops, it should be thoroughly dried. If the oil insulation drops, the oil should be changed or filtered. If the transformer is not tightly sealed and the moisture absorber is faulty, it should be repaired.
Faults 4. Core failed
Method of detection:
Check the insulation resistance of the grommet; if it is less than 10 megohms, it should be repaired.
Solutions:
Using a pulley, remove the damaged grommet before replacing the insulation.
Faults 5. In low-voltage coils with double layers, the insulation is damaged at the elbow, and cracks appear.
Solutions:
Removing the old insulation at the elbow or replacing the entire coil will solve the problem.
Faults 6. A core failure led to a breakdown.
Method of detection:
The most common faults related to iron cores are insulation damage between the iron cores, partial melting of the iron core, broken ground tabs, and loose clamps.Normally, partial melting of the iron core is caused by the insulation damage of the iron core bolts shorting the iron chip, severe damage to the interchip insulation, and improper grounding.
Solutions:
You need to scrape the burned area, and then paint it with insulating paint.
Transformer Secondary Fault
Most transformer failures are caused by short circuits in the secondary.
Short circuits in transformer secondary are caused by: Electric power and mechanical force may combine to deform the winding of the transformer, causing it to short circuit. When the transformer winding is deformed, a damaged fault can occur quickly. Most transformers will still run for a long time despite winding deformation and deformed parts. As a result of the secondary short-circuit, the primary coil needs a current from the power supply close to the short-circuit to balance the magnetic field. However, the large current exceeds the rated current by many times, causing the coil to burn. Once the transformer is short-circuited, there are hidden dangers in the safety of the power system.

Electrical Transformer Faults
1. Failure of the winding
There are mainly inter-turn short circuits, winding groundings, phase-to-phase short circuits, wire breakages, and joint weld. Here are the reasons for these failures:
- During manufacture or overhaul, local insulation may have been damaged;
- Sundries fall into the windings during operation, causing the temperature to rise and the insulation to age due to poor heat dissipation;
- Poor manufacturing processes, poor pressing, and weak mechanical strength cause winding deformation and insulation damage from short circuit impacts;
- Overheating occurs in the local area due to damp windings and insulation expansion blocking oil passages;
- Moisture has deteriorated the insulating oil, or the contact area with the air is too large, lowering the insulation level, lowering the oil level, exposing some windings to the air and preventing their timely handling;
If insulation breakdown occurs during operation, the winding will be shorted or ground faulted due to the above reasons. During the inter-turn short circuit, the transformer’s oil temperature increases, the power supply side current increases slightly, the DC resistance of each phase is unbalanced, and sometimes there’s a creaking or bubbling sound in the oil. Short circuits between turns can cause gas protection to operate. There will also be differential protection or overcurrent protection on the power supply side in severe cases. In case an inter-turn short circuit is found, it should be corrected immediately, because it can cause more serious single-phase grounding or inter-phase short circuits.
2. Failure of the sleeve
Oil spills, explosions, and flashovers all involve failures of this type,Here are the reasons for these failures:
- A poor seal, a low moisture ratio in the insulation, or an oil leak;
- Inhalation of moisture or improper configuration of respirators;
- Due to poor porcelain quality, the capacitor bushings on the high-voltage side of the transformer (110kV and above) are usually trachoma-filled or cracked;
- The capacitor core has a defect, causing a free discharge;
- Sleeve fouling of extreme severity;
3. Failed core
Here are the reasons for these failures:
- There is a problem with the insulation between the silicon steel sheets, resulting in a partial overheating and melting of the iron core;
- There is a short circuit between the iron core silicon steel sheet and the through-bolt due to damaged insulation on the through-bolt;
- A two-point grounding of the iron core is formed by residual welding slag;
- The top and middle of the transformer tank, between the flange, barrel skin, and bushings. As a result of local magnetic leakage, the internal iron core, winding clips, etc., become heated, causing insulation damage;
Transformers should be checked if the windings or iron core fail during operation.It is necessary to measure the DC resistance of each phase winding and compare them. If the difference is large, it is a winding fault. A winding fault can be identified by measuring the DC resistance of each phase winding and comparing the results. The damaged area can be painted if it is minor.
4. Failure of gas protection
Light gas acts on the signal, while heavy gas acts on trip gas protection faults. This is the main protection of the transformer. Following is an analysis of the reasons and solutions for gas protection actions:
- Possibly, the gas protection action is a result of inaccurate oil filtering, fueling, and cooling systems;
- There is a slow drop in oil level due to a drop in temperature and oil leakage, or a small amount of gas is generated due to a transformer failure;
- The result of a traversing short-circuit fault;
- The secondary circuit of the protection device failed;
Light gas protection signal after action. The reason is : A minor fault has been detected inside the transformer, Transformers contain air, secondary circuits are faulty, etc. Immediately check for abnormal phenomena, and if there is none, sample and analyze the gas. The gas protection action trips.
The transformer may have a serious fault, causing the oil to decompose into a large amount of gas, or the secondary circuit may break down.The backup transformer should be switched on first, then the external inspection should be conducted when the gas protection action trips. Make sure that the oil pillow’s explosion-proof door is in good condition; that no welding seams are cracked; that the transformer shell is not deformed; and that the gas is not flammable.
5. Automatic tripping of transformers: treatment
Following are the steps an operator should take when a transformer automatically trips:
- After the trip circuit breakers on each side of the transformer automatically trip, move the trip circuit breaker’s control switch to the position after the trip, and quickly start the backup transformer, adjust the load distribution and operation mode, and maintain the operation system;
- Make sure that the dropped card has the correct protective action;
- Determine whether the system is faulty and the nature of the fault;
- The test can be sent without inspection if the following circumstances apply and the leader consents:Circuit breakers are tripped by accidental touch protection; protections are tripped by obvious malfunctions; At the same time, the lower-level equipment of the tripping transformer breaks down, but its protection doesn’t kick in, and the fault has been removed, but only one test transmission can be conducted;
- There should be a comprehensive inspection of the transformer and its system, power outage, and insulation measurement if it is a main protection action, such as differential, heavy gas or current quick-break. Unidentified causes must be identified before the transformer can be operated. The transformer cannot be put into operation until the cause has been identified.
6. Fire breaks out in a transformer
The explosion or expansion of a transformer fire is also a dangerous accident because transformers contain many combustible substances. Fires caused by transformers are mainly caused by:
- Sleeve breaks and flashes off, oil seeps out under the pressure of the oil pillow and burns on the top cover;
- Transformer oil overflowed as a result of an internal fault in the casing or radiator;
The following actions should be taken immediately if a transformer catches fire:
- Cut off the power supply on each side of the transformer, disconnect the circuit breakers, and quickly restore power to the standby transformer;
- Turn off the cooling unit;
- The generator should be disconnected first when the main transformer and high power plant are on fire;
- Open the lower accident drain valve if the oil burns on the top cover of the transformer. A transformer that catches fire cannot be drained to prevent it from exploding;
- Extinguish the fire quickly. You can use a dry fire extinguisher or a foam extinguisher, for example.Notify the fire brigade if necessary. Transformer protection should open a circuit breaker in the event of such an accident. A circuit breaker that is not open due to the fault should be opened manually by hand, and the isolating switch that leads to the transformer’s power supply should be opened;
7. The tap changer is faulty
Typical failures include surface melting and burns, interphase contact discharges, or individual joint discharges. These are the main reasons:
- Connecting screws that are loose;
- The belt load adjustment device was not adjusted properly;
- Boards used to insulate taps are not well insulated;
- Insufficient spring pressure, poor joint solder, poor contact, and poor manufacturing process;
- Oil with a high acid value corrodes the tap changer’s contact surface;
Main transformer accidents are generally not single, but multiple and evolving, and the potential main fault points are relatively hidden, plus the particular nature of the fault. To ensure transformer and power grid safety and stability, as well as handle accidents correctly, we must keep informed about the following:
- Load type, load status, and system operation mode;
- Temperature rise and voltage of transformer upper oil;
- At the time of the accident, the weather conditions;
- Transformer maintenance and other work;
- Any wrong operation by the operator;
- Incorrect operation of the system;
- Describe the type of protection action, accident phenomenon, etc. Ensure transformer operation is patrolled, perform regular maintenance, eliminate equipment defects on a timely basis, conduct regular maintenance and preventive tests, and reduce the impact of transformer accidents on power grids and electrical equipment;