High frequency transformer sleeves play a vital role in the efficient functioning of electrical systems. These sleeves, also known as insulating materials, provide essential insulation and protection to high frequency transformers, safeguarding them from potential damages and ensuring optimal performance. However, like any other component, transformer sleeves are susceptible to various issues that can impact their functionality and compromise the overall performance of the transformer.
In this blog, we will explore 17 effective ways to solve high frequency transformer sleeve defects. Before delving into the solutions, let us first understand the importance of these sleeves and the potential issues they may encounter.
High frequency transformer sleeves act as a barrier between the electrical conductors and the surrounding environment, preventing electrical leakage, short circuits, and damage from external factors. They are designed to withstand high temperatures, electrical stress, and provide reliable insulation to ensure safe and efficient power transmission.
However, despite their crucial role, transformer sleeves can face several potential issues that may affect their performance. Over time, sleeves may develop cracks, burns, or discoloration due to various factors such as excessive heat, environmental conditions, or electrical overloads. These defects can compromise the insulation properties of the sleeve, leading to decreased efficiency, increased power losses, and even potential risks of electrical hazards.
1.Visual Inspection
Visual inspection is a fundamental and essential method for detecting and solving high frequency transformer sleeve defects. This technique involves a careful examination of the transformer sleeve to identify any visible signs of damage, such as cracks, burns, or discoloration. By conducting a thorough visual inspection, you can quickly identify and address potential issues before they escalate and cause significant problems in the transformer’s operation.
The importance of visual inspection cannot be overstated when it comes to maintaining the integrity and performance of transformer sleeves. These sleeves act as a protective layer, ensuring insulation and preventing electrical leakage, short circuits, and other potential hazards. However, due to various factors such as environmental conditions, thermal stress, or electrical overloads, transformer sleeves may develop defects over time.
Visual inspection allows you to carefully scrutinize the transformer sleeve, looking for any visible signs of wear and tear. Cracks or fractures on the surface, burn marks indicating excessive heat exposure, or discoloration due to degradation are all indications that the sleeve may be defective and require immediate attention. By identifying these issues early on, you can prevent further damage to the sleeve and ensure the continued safe and efficient operation of the transformer.
During the visual inspection, it is important to examine the entire surface of the transformer sleeve, paying close attention to critical areas where defects are more likely to occur. This includes edges, corners, and any areas where stress concentration is known to be higher. Additionally, inspecting the sleeve during both powered and non-powered states can provide valuable insights into the condition of the insulation and the presence of any electrical discharges or arcing.
Once any defects or anomalies are identified through visual inspection, appropriate measures can be taken to address the issue. This may involve repairing or replacing the damaged sleeve, implementing additional insulation layers, or taking steps to mitigate the underlying causes of the defects.
2.Temperature Monitoring
Temperature monitoring is a crucial method for addressing high frequency transformer sleeve defects and ensuring the reliable operation of electrical systems. Transformers generate heat during normal operation, and excessive temperatures can lead to insulation breakdown, reduced efficiency, and potential damage to the transformer sleeve. By closely monitoring and controlling the temperature, you can proactively prevent and resolve sleeve defects, optimizing the performance and lifespan of the transformer.
The temperature within a high frequency transformer should be carefully regulated to ensure it remains within the recommended range. This range is typically specified by the transformer manufacturer and depends on factors such as the transformer’s design, load conditions, and ambient temperature. Excessive heat can accelerate the aging and degradation of the transformer sleeve, compromising its insulation properties and increasing the risk of electrical failures.
Temperature monitoring involves the use of temperature sensors strategically placed within the transformer to measure and monitor the temperature levels. These sensors can be placed on the core, windings, or other critical areas of the transformer where heat buildup is more likely to occur. The collected temperature data is then analyzed to assess the transformer’s thermal performance and identify any abnormal temperature rises.
By actively monitoring the temperature, you can detect any potential anomalies or deviations from the desired temperature range. If the temperature exceeds the recommended limits, it is essential to investigate and address the underlying causes promptly. Common reasons for excessive temperatures include overloading, inadequate cooling, or insulation degradation. By taking immediate corrective measures, such as reducing the load, improving cooling mechanisms, or replacing damaged insulation, you can prevent further damage to the transformer sleeve and ensure its longevity.
3.Cleanliness
Maintaining cleanliness is a fundamental and often overlooked method for addressing high frequency transformer sleeve defects and ensuring the optimal performance of electrical systems. Transformers are prone to the accumulation of dust, dirt, and other contaminants, which can contribute to insulation breakdown and compromise the integrity of the transformer sleeve. By prioritizing cleanliness and implementing proper cleaning practices, you can proactively prevent and resolve sleeve defects, enhancing the overall reliability and efficiency of the transformer.
Cleanliness is essential for preserving the insulation properties of the transformer sleeve. Over time, dust particles, dirt, and other debris can accumulate on the sleeve’s surface and penetrate into its layers, potentially leading to electrical leakage, tracking, or even short circuits. These contaminants can also act as conductive paths, creating additional stress on the insulation and increasing the risk of sleeve defects.
When cleaning the transformer sleeve, it is crucial to use appropriate cleaning agents, tools, and techniques. Non-abrasive cleaning agents specifically designed for electrical insulation materials should be utilized to avoid damaging the sleeve’s surface or compromising its insulation properties. Soft brushes, lint-free cloths, or compressed air can be employed to gently remove dust and debris from the sleeve.
In addition to routine cleaning, it is essential to maintain a clean and dust-free environment around the transformer. Regularly vacuuming or dusting the surrounding area can help minimize the introduction of contaminants onto the transformer surface. Proper ventilation and filtration systems can also aid in reducing the ingress of airborne particles.
By prioritizing cleanliness and implementing regular cleaning practices, you can significantly reduce the risk of high frequency transformer sleeve defects. Clean sleeves ensure effective insulation, prevent electrical leakage, and promote optimal transformer performance. Moreover, by keeping the transformer environment clean, you can mitigate the potential negative impact of external contaminants and extend the lifespan of the sleeve.

4.Dielectric Testing
Dielectric testing is a crucial method for identifying and resolving high frequency transformer sleeve defects, ensuring the integrity and reliability of electrical systems. The dielectric strength of a transformer sleeve refers to its ability to withstand electrical stress and provide effective insulation. By subjecting the sleeve to rigorous dielectric testing, you can assess its insulation integrity, identify potential defects, and take appropriate measures to rectify any issues that may compromise the performance of the transformer.
Dielectric testing involves the application of high voltage to the transformer sleeve to evaluate its ability to withstand electrical stress without breakdown or failure. This testing process is typically performed using specialized equipment and follows standardized procedures and safety guidelines to ensure accurate results and minimize risks.
During dielectric testing, the transformer sleeve is subjected to voltage levels higher than its normal operating voltage. By carefully monitoring the response of the sleeve to this elevated voltage, any signs of insulation breakdown, such as electrical discharge, arcing, or voltage leakage, can be detected. These indicators serve as valuable evidence of potential defects within the sleeve, such as cracks, voids, or insufficient insulation layers.
Dielectric testing can be performed using various methods, including the use of high voltage testers, insulation resistance testers, or power frequency voltage tests. These tests evaluate the insulation properties of the transformer sleeve under different electrical stress conditions, helping to assess its performance and identify any weaknesses or defects.
If the dielectric testing reveals that the transformer sleeve fails to meet the required standards or exhibits signs of insulation breakdown, appropriate measures should be taken promptly. This may involve repairing or replacing the defective sleeve to ensure its optimal performance and prevent potential electrical hazards.
Regular dielectric testing is essential to verify the insulation integrity of transformer sleeves and identify potential defects before they escalate into more significant issues. By including dielectric testing as part of your maintenance routine, you can proactively address sleeve defects, maintain reliable insulation, and prolong the lifespan of your high frequency transformer.
5.Voltage Regulation
Voltage regulation is a vital method for addressing high frequency transformer sleeve defects and maintaining optimal performance in electrical systems. Transformers are designed to operate within specific voltage ranges, and deviations from these desired levels can lead to various issues, including insulation breakdown and degradation of the transformer sleeve. By implementing effective voltage regulation techniques, you can ensure that the transformer operates within the recommended voltage limits, minimizing the risk of sleeve defects and optimizing its overall performance.
Voltage regulation involves the control and maintenance of the transformer’s output voltage at a consistent and stable level. This is particularly important for high frequency transformers, as they are often used in sensitive electronic devices and systems that require precise voltage regulation for reliable operation.
Fluctuations in voltage can place additional stress on the transformer sleeve, potentially leading to insulation breakdown and the formation of defects. Excessive voltage levels can cause insulation aging, thermal stress, and accelerated degradation of the sleeve’s insulation properties. On the other hand, inadequate voltage levels can result in reduced efficiency, increased power losses, and potential operational issues.
Proper voltage regulation not only prevents the occurrence of sleeve defects but also helps optimize the transformer’s overall efficiency and performance. By maintaining a stable and regulated voltage, the insulation integrity of the transformer sleeve is preserved, minimizing the risk of electrical breakdown and enhancing the lifespan of the sleeve.
Additionally, voltage regulation can be achieved through proper design considerations and load management. Ensuring that the transformer is appropriately sized for the intended load and that the load distribution is balanced can help prevent voltage fluctuations and reduce the stress on the transformer sleeve.
6.Overcurrent Protection
Overcurrent protection is a critical method for addressing high frequency transformer sleeve defects and ensuring the safe and reliable operation of electrical systems. Transformers are designed to handle specific current levels, and excessive currents can lead to insulation breakdown, overheating, and potential damage to the transformer sleeve. By implementing effective overcurrent protection measures, you can prevent the occurrence of sleeve defects and mitigate the risks associated with excessive currents, ensuring the longevity and optimal performance of the transformer.
Overcurrent protection involves the use of protective devices, such as circuit breakers, fuses, or relays, to monitor and control the current flow within the transformer. These devices are designed to detect abnormal current conditions and interrupt the circuit when overcurrent events occur, preventing potential damage to the transformer and its sleeve.
When overcurrent events, such as short circuits or excessive load currents, occur, the protective devices swiftly respond by opening the circuit and isolating the transformer from the electrical supply. This action helps protect the transformer sleeve from the harmful effects of excessive currents, such as insulation breakdown, thermal stress, or even the risk of fire.
Proper selection and coordination of overcurrent protective devices are crucial for effective protection of the transformer and its sleeve. These devices should be appropriately sized and rated to handle the expected current levels while providing reliable and sensitive protection against overcurrent conditions.
By implementing effective overcurrent protection measures, you can safeguard the transformer sleeve from the damaging effects of excessive currents, ensuring its insulation integrity and minimizing the risk of defects. This protection not only extends the lifespan of the sleeve but also enhances the overall reliability and safety of the electrical system.
7.Insulation Enhancements
Insulation enhancements are a crucial method for addressing high frequency transformer sleeve defects and improving the insulation properties of electrical systems. The insulation of a transformer sleeve plays a vital role in preventing electrical breakdown, protecting against insulation failure, and ensuring the reliable operation of the transformer. By implementing various insulation enhancements, you can strengthen the insulation system, mitigate the risk of sleeve defects, and optimize the overall performance and lifespan of the transformer.
Insulation enhancements involve improving the insulation materials, design, or techniques used in the construction of the transformer sleeve. These enhancements aim to enhance the insulation strength, increase resistance to electrical stress, and improve the overall insulation performance.
One way to enhance the insulation of the transformer sleeve is through the selection of high-quality insulation materials. Advancements in insulation technology have led to the development of materials with improved dielectric properties, better thermal stability, and increased resistance to aging and breakdown. Opting for these advanced insulation materials can significantly enhance the insulation integrity of the sleeve, reducing the risk of defects and extending its lifespan.
Another approach to insulation enhancements is through design modifications. This includes optimizing the insulation system by ensuring proper insulation layer thickness, minimizing air gaps, and improving the overall insulation arrangement. By carefully designing the transformer sleeve with adequate insulation spacing and efficient insulation interfaces, the electrical stress on the insulation can be reduced, thereby minimizing the risk of insulation breakdown and defects.
Regular maintenance and testing of the insulation system also contribute to insulation enhancements. Performing insulation resistance tests, partial discharge tests, or other diagnostic tests on a routine basis can help identify potential insulation weaknesses or defects before they escalate into major issues. Prompt repair or replacement of damaged insulation can prevent further deterioration and ensure the continued integrity of the transformer sleeve.
8.Maintenance and Monitoring
Maintenance and monitoring are essential methods for addressing high frequency transformer sleeve defects and ensuring the reliable and efficient operation of electrical systems. Transformers play a crucial role in power distribution, and their sleeves serve as vital insulation barriers to prevent electrical breakdown and protect the internal components. By implementing comprehensive maintenance and monitoring practices, you can proactively detect and resolve sleeve defects, minimize the risk of insulation failure, and optimize the performance and longevity of the transformer.
Maintenance involves regular inspections, servicing, and upkeep of the transformer and its sleeve to identify and address any potential issues. It includes a range of activities such as cleaning, testing, lubrication, and repair or replacement of components when necessary. By adhering to a well-planned maintenance schedule, you can ensure that the transformer sleeve remains in optimal condition and mitigate the risk of defects arising from wear, aging, or environmental factors.
Regular visual inspections are an important aspect of maintenance. By visually examining the transformer sleeve, you can identify visible signs of defects such as cracks, discoloration, or physical damage. Visual inspections also help detect other indicators of potential problems, such as loose connections, oil leaks, or improper insulation conditions.
Monitoring the operating conditions of the transformer, including temperature, load, and voltage, is also a key part of maintenance. Continuous monitoring systems can provide real-time data on these parameters, allowing for early detection of abnormal conditions that could impact the insulation performance and lead to potential sleeve defects. By promptly addressing these deviations, you can prevent further damage and optimize the transformer’s operation.
Proactive maintenance and monitoring practices not only help detect and resolve existing sleeve defects but also aid in preventing future issues. Regular maintenance can prevent the accumulation of dust, dirt, or moisture that may compromise the insulation integrity. It can also help identify and rectify potential sources of stress on the transformer, such as excessive load or voltage fluctuations, which could contribute to sleeve defects.
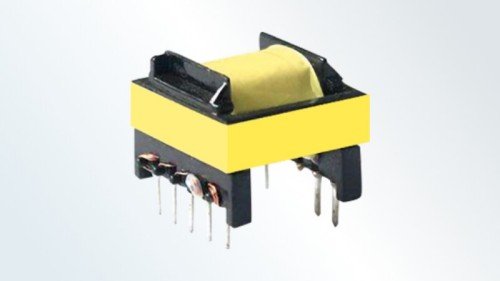
9.Professional Assistance
Professional assistance is a valuable method for addressing high frequency transformer sleeve defects and ensuring effective solutions for complex or critical issues. While some transformer sleeve defects can be resolved through basic maintenance or troubleshooting, others may require specialized knowledge, skills, and equipment that only professionals possess. By seeking the expertise of qualified professionals, you can access their in-depth understanding of transformer systems and benefit from their experience in diagnosing and rectifying sleeve defects.
Transformers and their sleeves are intricate components that operate under precise electrical and mechanical conditions. When faced with sleeve defects, it is crucial to rely on professionals who have the expertise and training to handle the complexities involved. Professional assistance can come in the form of electrical engineers, transformer specialists, or experienced technicians who specialize in transformer maintenance and repair.
One of the key advantages of seeking professional assistance is the ability to accurately diagnose the root cause of the sleeve defect. Professionals have the knowledge and experience to conduct comprehensive inspections, tests, and analyses to determine the underlying issues contributing to the defect. Their expertise allows them to identify defects that may not be readily apparent and develop an effective plan for resolution.
Moreover, professionals have access to specialized tools and equipment that are specifically designed for diagnosing and repairing transformer sleeve defects. These tools enable them to conduct detailed testing, measurements, and assessments with precision, ensuring accurate results and effective solutions. Professional assistance ensures that the most appropriate techniques and resources are utilized to address the specific type and extent of the sleeve defect.
Another significant advantage of professional assistance is the assurance of safety and compliance with industry standards. Professionals are well-versed in safety protocols and regulations associated with transformer maintenance and repair. They understand the potential hazards involved and take necessary precautions to protect themselves and the equipment while performing the required tasks. By engaging professionals, you can have peace of mind knowing that the repairs or modifications are conducted safely and in compliance with relevant codes and standards.
10.Core Replacement
Core replacement is a significant method for solving high frequency transformer sleeve defects when the issues are severe or irreparable through other means. Transformers play a critical role in electrical power distribution, and their sleeves act as essential insulation barriers. However, over time, the sleeve may suffer from extensive damage, insulation breakdown, or other defects that compromise the integrity of the transformer. In such cases, core replacement offers an effective solution by replacing the damaged or defective core, ensuring the transformer’s reliable operation and preserving its performance.
The core of a transformer is a crucial component that facilitates the efficient transfer of electrical energy. It consists of laminated iron or steel plates, known as laminations, which form a closed magnetic circuit. The core’s function is to channel the magnetic flux generated by the primary winding to the secondary winding, allowing for the transformation of voltage and current. When the core becomes damaged or compromised, it can result in a range of issues, including insulation breakdown, increased power losses, or even complete transformer failure.
Core replacement involves the removal and replacement of the damaged or defective core with a new one. This process requires expertise, precision, and careful coordination to ensure a seamless transition and optimal performance. The new core must be selected based on the specific transformer’s requirements, including its size, voltage rating, and operating conditions. It should be manufactured using high-quality materials and adhere to industry standards to ensure the best possible performance and longevity.
The core replacement process typically involves several steps. First, the transformer is carefully de-energized, and the necessary safety precautions are taken. The existing core is then dismantled, with each lamination being carefully removed to minimize any further damage. Once the old core is completely removed, the new core is carefully installed, ensuring proper alignment and spacing between the laminations. It is crucial to maintain the correct magnetic circuit geometry and minimize any air gaps to optimize the transformer’s efficiency and minimize losses.
After the core replacement, the transformer undergoes thorough testing and commissioning to ensure its proper functioning. Various tests, such as insulation resistance, transformer ratio, and impedance tests, are performed to verify the integrity of the new core and the overall performance of the transformer. This comprehensive testing ensures that the replacement has been successful and the transformer is ready to resume its normal operation.
11.Winding Repair
Winding repair is a crucial method for solving high frequency transformer sleeve defects that specifically relate to the transformer’s windings. Transformers rely on their windings to facilitate the transfer of electrical energy between the primary and secondary coils. However, over time, the windings can experience various issues, such as insulation degradation, mechanical damage, or electrical faults, leading to sleeve defects and potential transformer failure. Winding repair offers an effective solution by addressing these specific problems and restoring the functionality and performance of the transformer.
The windings of a transformer are typically made of copper or aluminum conductors insulated with a layer of insulation material, such as enamel or paper. These windings are wound around the transformer’s core to create the necessary electromagnetic fields for energy transfer. When the windings become damaged or compromised, it can result in insulation breakdown, increased resistance, or even short circuits, jeopardizing the transformer’s operation.
Winding repair involves identifying and addressing the specific issues affecting the windings to rectify the sleeve defects. This method requires expertise in transformer repair and a thorough understanding of winding construction, insulation materials, and electrical principles. The repair process may involve different techniques, depending on the nature and extent of the winding defects.
One common issue that may require winding repair is insulation degradation. Over time, the insulation materials used in the windings can deteriorate due to factors such as heat, moisture, or mechanical stress. Insulation degradation can result in reduced insulation resistance and compromised electrical insulation properties, leading to potential sleeve defects. Winding repair techniques can include the removal and replacement of damaged insulation, reconditioning of existing insulation, or applying additional insulation layers to strengthen the windings.

12.Resin Impregnation
Resin impregnation is a valuable method for solving high frequency transformer sleeve defects by enhancing the insulation properties and structural integrity of the transformer’s windings. Transformers rely on the insulation surrounding the windings to prevent electrical breakdown and ensure safe and efficient operation. However, over time, the insulation may degrade, leading to reduced insulation resistance and an increased risk of sleeve defects. Resin impregnation offers an effective solution by saturating the windings with a specialized resin, improving insulation performance, and protecting the transformer from potential failures.
The windings of a transformer are typically made of copper or aluminum conductors, which are insulated with materials such as enamel or paper. These insulation materials provide the necessary electrical insulation and mechanical support to the windings. However, exposure to environmental factors, temperature variations, and aging can cause the insulation to degrade, leading to a higher risk of short circuits, insulation breakdown, or other sleeve defects.
Resin impregnation is typically performed using specialized equipment and under controlled conditions to ensure proper impregnation and resin curing. The windings are carefully prepared and cleaned before the resin is applied. After impregnation, the transformer undergoes a curing process, allowing the resin to solidify and form a stable insulation layer within the windings. Comprehensive testing and analysis are conducted to verify the effectiveness of the impregnation process and ensure the improved insulation performance.
13.Shielding
Grounding is a fundamental method for solving high frequency transformer sleeve defects by providing a safe and reliable path for electrical currents to flow to the earth. Transformers play a critical role in electrical power systems, facilitating the transfer of energy between different voltage levels. However, improper grounding or lack of effective grounding can lead to various issues, including increased noise, voltage imbalances, and potential sleeve defects. Grounding offers an effective solution by ensuring electrical safety, reducing electromagnetic interference (EMI), and protecting the transformer from potential failures.
Grounding involves connecting specific components of the transformer to the earth or a designated ground system. This connection establishes a low-resistance path for electrical currents to flow to the earth, allowing for the dissipation of excess energy and the prevention of hazardous conditions. The grounding system typically includes grounding electrodes, conductors, and other components that facilitate the safe discharge of fault currents or unwanted electrical energy.
Proper grounding is essential for high frequency transformers to maintain a stable reference point and mitigate the risk of sleeve defects. Here are some key benefits of effective grounding:
- Electrical Safety: Grounding provides a path for fault currents to flow safely to the earth in the event of a fault or short circuit. By establishing a low-resistance grounding connection, excessive currents are diverted away from the transformer, preventing damage to the windings and minimizing the risk of sleeve defects. Proper grounding helps protect both the transformer and personnel working on or near the equipment, ensuring a safe operating environment.
- Reduction of Electromagnetic Interference (EMI): Grounding helps minimize electromagnetic interference by providing a reference point for electrical signals and reducing the potential for voltage fluctuations. Unwanted currents or noise induced by external sources can be redirected to the ground, reducing their impact on the transformer’s operation. By mitigating EMI, grounding helps maintain signal integrity, reduces the risk of sleeve defects caused by electrical disturbances, and ensures the transformer functions optimally in high frequency applications.
- Voltage Stabilization: Proper grounding helps maintain voltage stability by providing a reference potential for the transformer. It helps prevent voltage imbalances, transient voltages, or fluctuations that could lead to insulation breakdown or other sleeve defects. By establishing a reliable ground connection, grounding helps maintain the desired voltage levels and improves the overall performance and lifespan of the transformer.
- Lightning Protection: High frequency transformers, like any electrical equipment, are vulnerable to lightning strikes. Effective grounding plays a crucial role in providing a safe path for lightning currents to dissipate into the ground. A well-designed grounding system, with appropriate lightning protection measures, helps minimize the risk of lightning-induced damage to the transformer’s windings, insulation, and other components.
14.Grounding
Grounding is a critical method for solving high frequency transformer sleeve defects by establishing a safe and reliable path for electrical currents to flow to the earth. Transformers play a vital role in electrical power systems, facilitating the efficient transfer of energy between different voltage levels. However, improper grounding or the lack of effective grounding can lead to various issues, including increased noise, voltage imbalances, and potential sleeve defects. Grounding offers an effective solution by ensuring electrical safety, reducing electromagnetic interference (EMI), and protecting the transformer from potential failures.
Grounding involves connecting specific components of the transformer to the earth or a designated ground system. This connection establishes a low-resistance path for electrical currents to flow to the earth, allowing for the dissipation of excess energy and the prevention of hazardous conditions. The grounding system typically includes grounding electrodes, conductors, and other components that facilitate the safe discharge of fault currents or unwanted electrical energy.
Proper grounding is essential for high frequency transformers to maintain a stable reference point and mitigate the risk of sleeve defects. Here are some key benefits of effective grounding:
- Electrical Safety: Grounding provides a path for fault currents to flow safely to the earth in the event of a fault or short circuit. By establishing a low-resistance grounding connection, excessive currents are diverted away from the transformer, preventing damage to the windings and minimizing the risk of sleeve defects. Proper grounding helps protect both the transformer and personnel working on or near the equipment, ensuring a safe operating environment.
- Reduction of Electromagnetic Interference (EMI): Grounding helps minimize electromagnetic interference by providing a reference point for electrical signals and reducing the potential for voltage fluctuations. Unwanted currents or noise induced by external sources can be redirected to the ground, reducing their impact on the transformer’s operation. By mitigating EMI, grounding helps maintain signal integrity, reduces the risk of sleeve defects caused by electrical disturbances, and ensures the transformer functions optimally in high frequency applications.
- Voltage Stabilization: Proper grounding helps maintain voltage stability by providing a reference potential for the transformer. It helps prevent voltage imbalances, transient voltages, or fluctuations that could lead to insulation breakdown or other sleeve defects. By establishing a reliable ground connection, grounding helps maintain the desired voltage levels and improves the overall performance and lifespan of the transformer.
- Lightning Protection: High frequency transformers, like any electrical equipment, are vulnerable to lightning strikes. Effective grounding plays a crucial role in providing a safe path for lightning currents to dissipate into the ground. A well-designed grounding system, with appropriate lightning protection measures, helps minimize the risk of lightning-induced damage to the transformer’s windings, insulation, and other components.
15.Environmental Control
Environmental control is a crucial method for solving high frequency transformer sleeve defects by ensuring that the operating environment meets the necessary conditions for optimal performance and longevity. Transformers are essential components in electrical power systems, responsible for efficient energy transfer between different voltage levels. However, environmental factors can significantly impact transformer performance, leading to insulation degradation, overheating, and potential sleeve defects. Environmental control offers an effective solution by creating a favorable operating environment that mitigates the risks associated with temperature, humidity, dust, and other external influences.
High frequency transformers are particularly sensitive to environmental conditions due to their compact size, increased power densities, and frequent use in electronic and telecommunications applications. Therefore, maintaining an appropriate operating environment becomes paramount to prevent sleeve defects and ensure the transformer’s reliability.
Environmental control encompasses several key factors that need to be considered:
- Temperature Control: Temperature is a critical parameter that directly affects the performance and lifespan of a transformer. Excessive heat can accelerate insulation aging, increase losses, and degrade the mechanical and electrical properties of the sleeve. On the other hand, extremely low temperatures can cause stiffness and brittleness in the insulation material. Implementing effective temperature control measures, such as proper ventilation, cooling systems, and temperature monitoring, is essential to maintain the transformer within its recommended temperature range and minimize the risk of sleeve defects.
- Humidity Control: High humidity levels can lead to moisture absorption, which can compromise the insulation’s dielectric properties and promote corrosion. Conversely, excessively dry conditions can cause static buildup and increase the risk of electrical arcing. Controlling humidity through the use of dehumidifiers, humidity sensors, and moisture barriers helps maintain an optimal moisture level, preventing insulation degradation and potential sleeve defects.
- Dust and Contaminant Control: Dust, dirt, and other contaminants can accumulate on the transformer’s surface and within the sleeve, affecting its insulation performance. These contaminants can lead to electrical tracking, reduced dielectric strength, and increased stress on the insulation. Implementing effective dust control measures, such as regular cleaning, air filtration, and maintaining a clean operating environment, helps minimize the risk of sleeve defects caused by contaminants.
- Vibration and Mechanical Stress Control: Transformers can be subject to mechanical vibrations and stress due to various factors, such as nearby machinery, transportation, or inadequate mounting. Excessive vibrations and mechanical stress can lead to insulation displacement, increased friction, and potential sleeve defects. Proper mounting techniques, vibration dampening measures, and mechanical stress analysis are essential to mitigate these risks and ensure the integrity of the transformer’s sleeve.
In conclusion, the information shared in this blog provides valuable insights into addressing high frequency transformer sleeve defects. By implementing these 15 effective solutions, you are taking significant steps toward achieving optimal transformer performance and ensuring a reliable power supply for your operations.